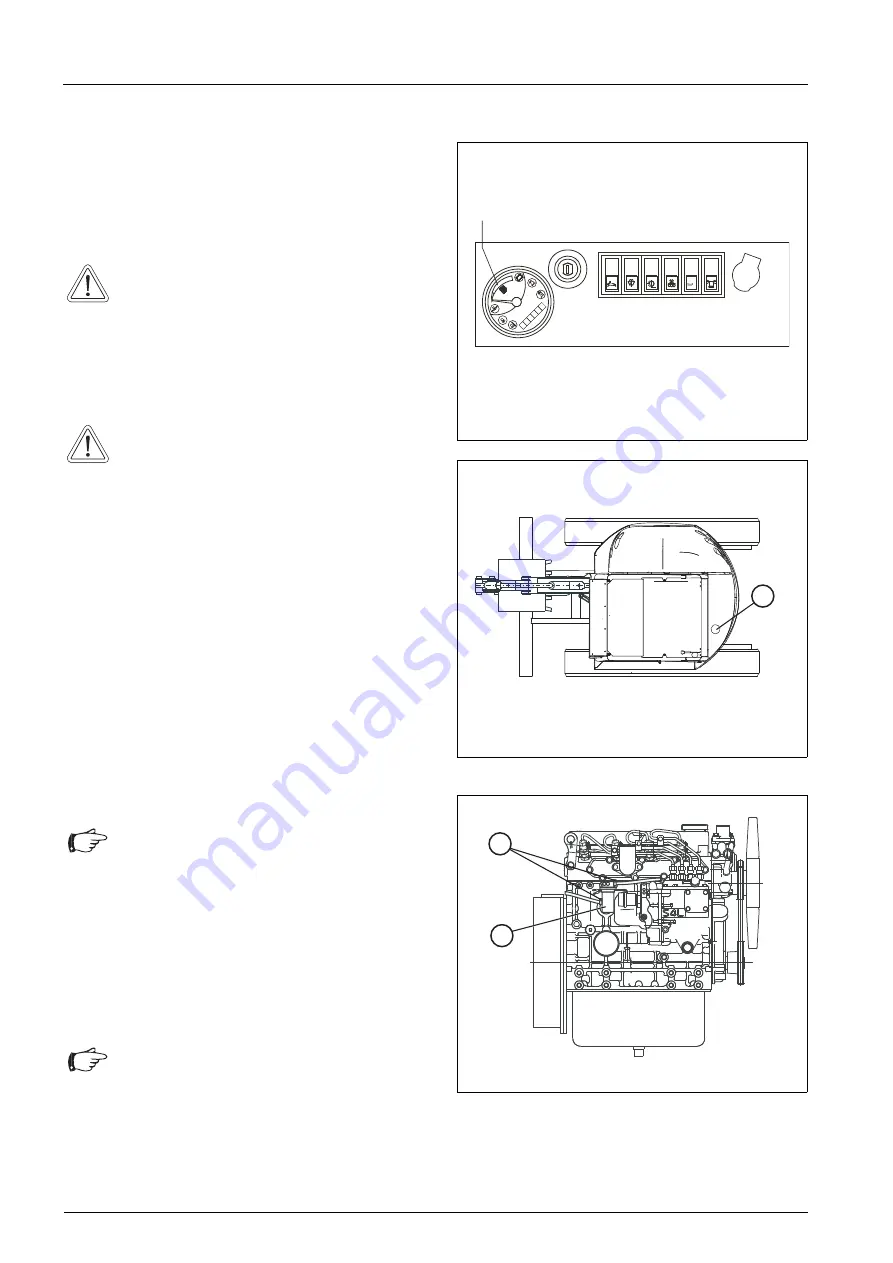
77
Operating Manual Crawler Excavator TC37
Care and Maintenance
7
7.8.4
Fuel system
Checking the fuel level
• Check the fuel level using the fuel gauge (45/23).
• In order to prevent condensation from forming
before the machine is next put into operation, top
up fuel every day after use (46/1).
•
Maintain visual contact with the fuel gauge (46/1)
and the filler neck (46/1).
Replacing the fuel filter
• Loosen the hose clamps (47/2) and remove the
filter (47/1).
• Collect any escaping fuel.
• Install a new fuel filter and re-tighten the hose
clamps.
• Check for leakages.
Fig. 45
Checking the fuel level
Fig. 46
Fuel tank
0
4/4
h.
R
HR3.7-03-49
23
HR3.7-04-50
1
Caution
When topping up fuel with the electrical
refueling pump the fuel cover must be opened
to avoid excessive pressure in the fuel tank.
Caution
The pump switch is "on".
Fig. 47
Replacing the fuel filter
HR14-03-51
1
2
Attention
• Collect the fuel in a suitable container.
Attention
The fuel system does not have to be vented.