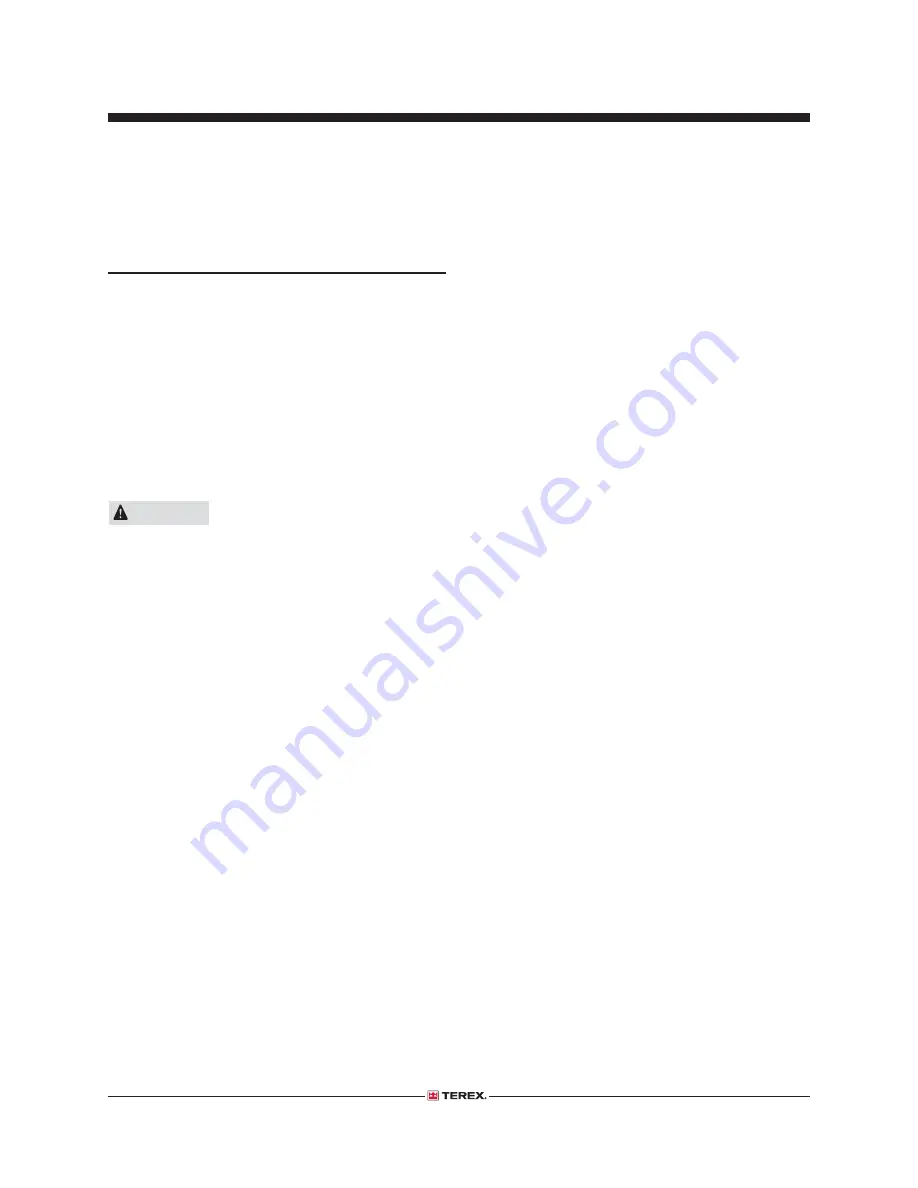
REV B
Section 4 • Repair Procedures
August 2016
Part No. 229171
AL4L • AL5L
4 - 5
How to Disassemble the Winch
Note: For ease of disassembly, refer to the
illustration on the next page.
1 Remove the winch. See 2-1,
How to Remove
the Winch
.
2 On a workbench, remove the cable drum and
lock arm.
3 Remove the lock gear and two jam nuts from
the pinion shaft.
4 Remove the retaining ring from the small
groove at the non-threaded end of the pinion
shaft. Rotate the pinion shaft until the shaft is
removed. Hold the winch components in place
while removing the pinion shaft.
5 Remove the ratchet pawl assemblies.
6 Remove the pinion shaft bushings. Use a soft
metal drift equal to the outside diameter of the
bushing and tap with a rubber mallet.
Note: Carefully observe the quantity and location
of the shims between the winch drum and the
bushing before disassembling.
2-1
Winch
How to Remove the Winch
1 Turn the handle of the mast pivot winch and
fully loosen the mast pivot cable. Remove the
handle from the winch.
2 Open the cabinet doors and locate the winch.
Remove the fasteners securing the handle to
the winch, and remove the handle.
3 Remove the cable retaining fastener securing
the cable to the winch drum. Unwind the cable
from the winch drum.
CAUTION
Bodily injury hazard. Cables can
fray. Always wear adequate hand
protection when handling the
cable.
4 Remove the winch from the machine.
Winch
Summary of Contents for AL4L
Page 1: ......
Page 3: ...August 2016 Part No 229171 AL4L AL5L Serial Number Legend INTRODUCTION iii...
Page 4: ...August 2016 AL4L AL5L Part No 229171 This page intentionally left blank iv...
Page 14: ...REV B August 2016 2 4 AL4L AL5L Part No 229171 Section 2 Specifications SPECIFICATIONS...
Page 67: ......