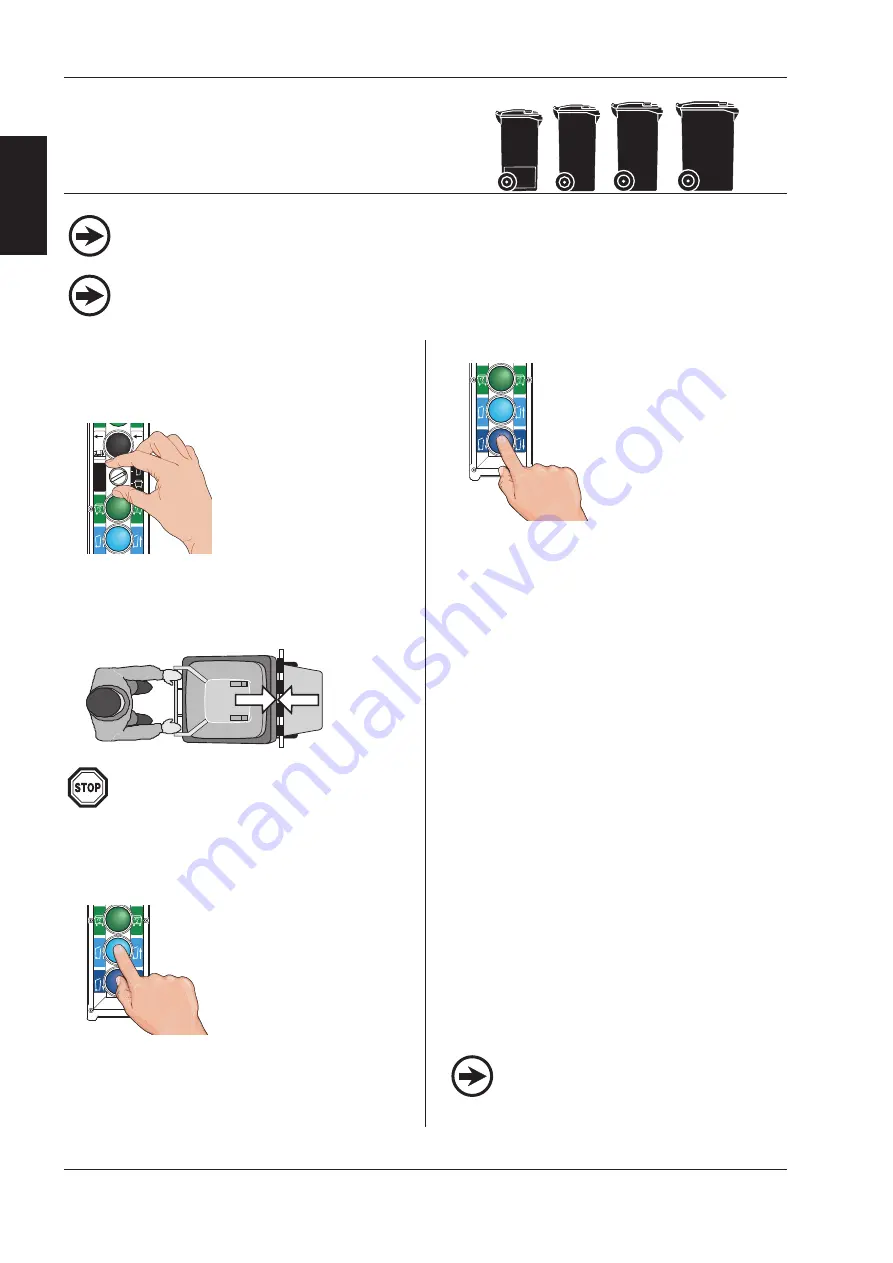
5) Remove the bin:
-
Press the dark blue
DOWN button (H).
The bin lowers to the
ground.
-
Pull the bin out of the bin
lift as soon as the wheels
touch the ground.
14
EN
E
N
3
.
B
in
l
if
t
o
p
e
ra
ti
o
n
37878
05-2017
ã
Terberg Machines B.V., IJsselstein, The Netherlands
All rights reserved. No part of this book may be reproduced, stored in database or retrieval system, or published, in any form or in any way,
electronically, mechanically, by print, photoprint, microfilm or any other means without prior written permission from the publisher.
1) Switch on the refuse collection vehicle's
compactor body.
2) Select 2-wheel bins:
Set the rotary switch (E) to
2-wheel bins.
[Or press the black button (K), this
can be done on both button
control stations.
The left-hand LED next to the
2-wheel bin should light up.]
*
3) Roll the bin against and over the pick-up comb
(06).
4) Empty the bin:
Press the light blue UP but-
ton (G), on the side of the
lifting chair selected.
The bin will be lifted to the tip-
ping position and emptied.
If any refuse remains stuck in the bin, you can give it
an extra shake by keeping the UP button pressed.
3.4.1 2-wheel bins;
capacity 80 to 360 litres
according to EN 840-1
Chamberlain
Chamberlain
For manual loading, the safety arms (04) do
not need to be folded down.
Because in manual operation the bin security
switch is deactivated, great care must be
taken that the bin is located correctly on the
pick-up comb.
The optional DIN pick-up arms (18) must be
folded in.
3.4
Manual loading with the pick-up comb
[ ] *
This text applies to the optional button control stations. See 'Important components' at the start of this chapter.
Only give an extra shake if there is a need for
this. Shaking takes time and causes extra
noise for the surrounding area.