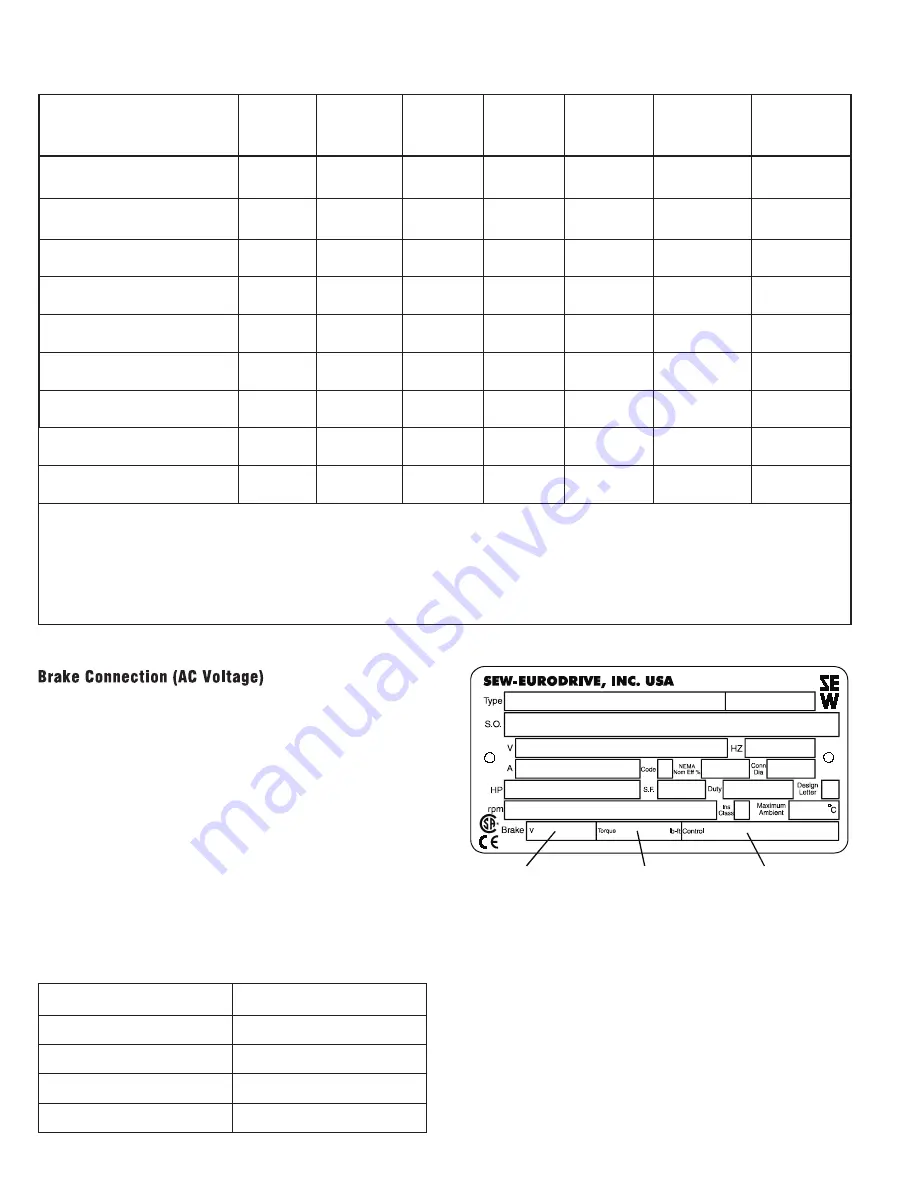
SEW-Eurodrive motor brakes can be connected in a number of different
ways. In order to connect the brake for each application, it is important to
refer to the data on the motor nameplate that describes the brake system.
The brake fields are: brake voltage, brake torque and brake control.
This operating instruction covers AC brake voltages with the following
brake control components. If the brake voltage is DC, or if the brake con-
trol components differ from those listed below, an additional operating
instruction must be consulted for connection information.
SEW-Eurodrive fail-safe mechanical brakes are DC controlled. Stan-
dardly, a brake rectifier (halfwave) is provided to convert the AC line
voltage to the DC voltage required to drive the brake. 24VDC brakes do
not include a rectifier. When voltage (V
B
) is applied to the brake, it will
release. When voltage (V
B
) is removed from the brake, it will set. The
brake rectifier can be wired either for normal brake reaction time (set-
ting, stopping) or fast brake reaction time. The fast brake reaction will set
the brake more quickly which will provide a shorter and more repeatable
stopping distance. There are two basic types of brake rectifiers, BG and
BGE. The BG brake rectifier is standard on motor sizes DT71 - DT100.
The BGE rectifier is standard on motor sizes DV112 - DV225. The BGE
rectifier can be ordered with motor sizes DT71 - DT100 and will provide
faster brake release times allowing the motor to cycle more frequently.
The wiring diagrams for brake connections are located on the inside of
the motor conduit box lid. The brake will release and allow the motor to
rotate when the nameplate AC brake voltage V
B
is supplied to the brake
rectifier terminals. There are certain cases where the brake rectifier can
receive its voltage from the motor's terminal block, meaning that when
power is applied to the motor it will simultaneously release the brake and
start the motor. See page 3 for this description.
Brake Coil Resistance
Motor Frame
DT71-80
DT80
DT90-100
DT100
DV112-132S
DV132M-160M
DV160L-225
Brake Size
BM(G)05
BM(G)1
BM(G)2
BM(G)4
BM(G)8
BM15
BM30/31/32/62
Brake Torque (lb-ft)
0.89 - 3.7
4.4 - 7.4
3.7 - 14.8
17.7 - 29.5
7.00 - 55.3
18.4 - 110.6
36.9 - 442.5
BRAKE VOLTAGE
R
B
(
Ω
)
R
B
(
Ω
)
R
B
(
Ω
)
R
B
(Ω
)
R
B
(
Ω
)
R
B
(
Ω
)
R
B
(
Ω
)
AC (to rectifier V
B
)
DC
R
T
(
Ω
)
R
T
(
Ω
)
R
T
(
Ω
)
R
T
(
Ω
)
R
T
(
Ω
)
R
T
(
Ω
)
R
T
(
Ω
)
24
4.3
3.8
3.3
7
1.6
0.8
0.7
13.2
11.8
10.3
8.2
8.2
5.0
5.3
105-116
48
17.1
52.5
15.2
47.0
13.3
40.9
10.7
32.7
6.2
32.7
3.1
20.1
2.8
21.1
186-207
80
54.0
166
48.1
149
42.1
129
33.8
103
19.6
103
9.8
63.5
8.9
66.7
208-233
96
68.0
209
60.5
187
53.0
163
42.5
130
24.7
130
12.4
80.8
11.2
84.0
330-369
147
171
525
152
470
133
409
107
327
62
327
31.1
201
28.1
211
370-414
167
215
661
191
591
168
515
134
411
78.1
411
39.2
253
35.4
266
415-464
185
271
832
241
744
211
649
169
518
98.3
518
49.3
318
44.6
334
465-522
208
341
1047
303
937
266
817
213
652
110
577
62.1
401
56.1
421
Voltage AC - The voltage shown is the nameplate AC brake voltage supplied to the brake rectifier.
DC - The voltage shown is the effective DC voltage required by the brake coil. The measured voltage from
the rectifier will be 10-20% lower than that shown.
Brake Coil Resistance - values must be measured with the brake coil disconnected from the rectifier.
R
B
-
Accelerator coil resistance in
Ω
, measured from the red to the white brake coil wire.
R
T
-
Fractional coil resistance in
Ω
, measured from the white to the blue brake coil wire.
Brake Control (Rectifier)
Part Number
BG1.5
825 384 6
BG3.0
825 386 2
BGE1.5
825 385 4
BGE3.0
825 387 0
Brake Voltage
Brake Torque
Brake Control
2
Summary of Contents for LM1014
Page 5: ...5...
Page 6: ...6...
Page 7: ...7...
Page 11: ...11 LM Control Box Overlay...
Page 20: ...20...
Page 21: ...21 LM Machine PARTS View...
Page 24: ...24 LM 2x Back gauge Crank Assembly...
Page 26: ...26 LM 2x Back gauge Pointer Assembly...
Page 28: ...28 LM 2x Back gauge Drive Assembly...
Page 29: ...29 LM 2x Back gauge Arm Assembly...
Page 31: ...31 LM Four Foot Squaring Arm...