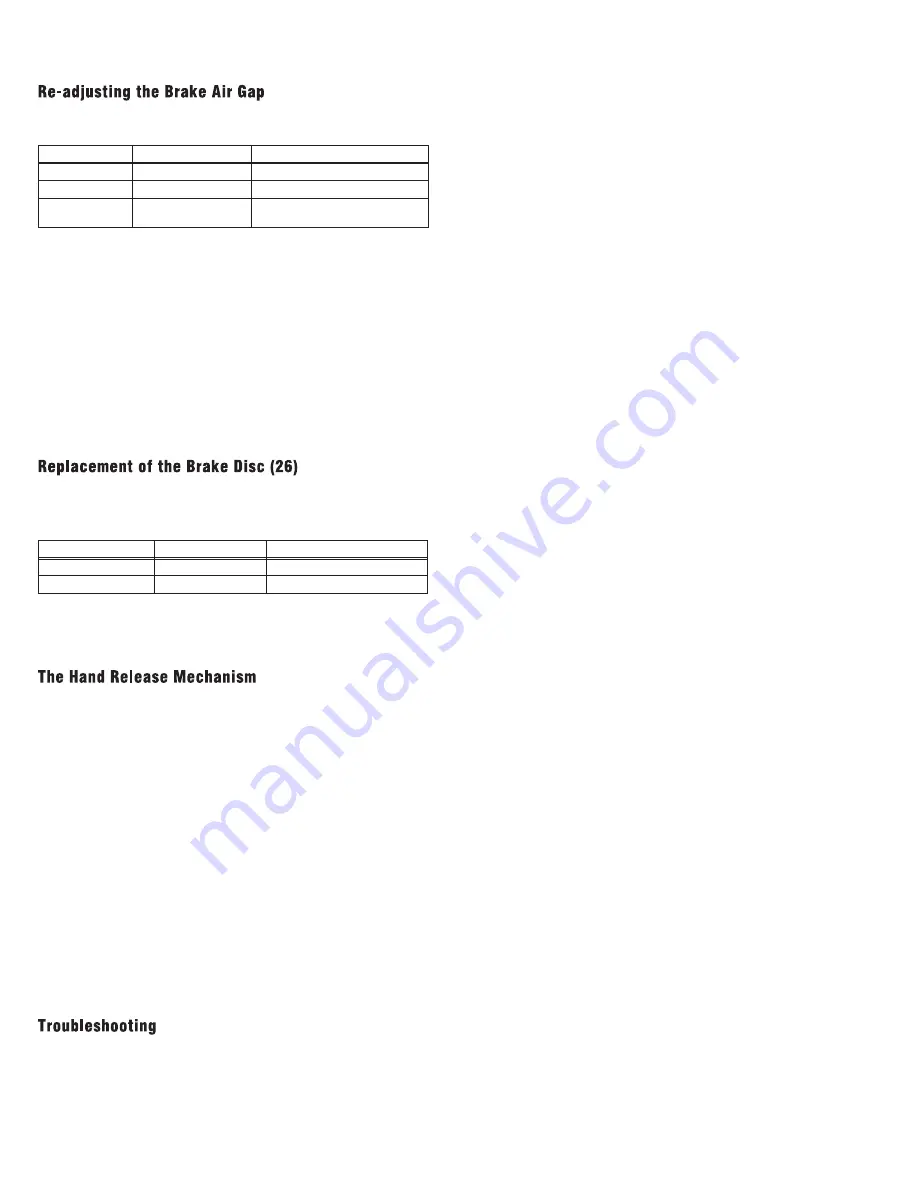
A properly adjusted brake air gap is critical for correct operation. The fol-
lowing table indicates the required air gap measurement.
Prolonged use of the brake will wear the brake disc lining. This wear in-
creases the air gap. When the air gap approaches its maximum value, the
brake must be re-adjusted. To re-adjust the brake, follow the procedure
below.
1.
Remove the fan cover (14), fan snapring, fan (17), rubber seal (2), and
any accessories at the fan end.
2.
Insert a feeler gauge between the brake coil body (21) and the station-
ary disc (22), tighten the adjusting nuts (19) until the minimum value
for the air gap is reached equally around the brake. With motor size
160L and up (brakes BM30 to BM62) first screw the threaded bush-
ings (24) into the endshield. After setting the air gap, lock the bush-
ings (24) against the coil body.
3.
Ensure a play of 0.06" to 0.08" (1.5 to 2 mm) in the releasing arm. See
“THE HAND RELEASE MECHANISM.”
Extended operation of the brake may wear the brake disc (26) beyond ac-
ceptable limits. The thickness of the brake disc can be measured to deter-
mine if this has occurred.
Motor Size
Brake Size
Min. Disc (26) Thickness
DT71 - DT100
BM05 - BM4
0.354" (9mm)
DV112 - DV225
BM8 - BM62
0.394" (10mm)
If the brake disc (26) is worn below the measurement given, it must be re-
placed. If the thickness is greater than the specification above, the brake
disc is still usable and the brake can be re-adjusted.
Most of our brakes are supplied with a hand-operated release lever. This
allows opening of the brake without applying power, allowing for adjust-
ments on the driven machinery.
There are two brake release mechanisms available:
The “BMHR” (4) type requires a lever to be inserted into the release arm.
To open the brake, pull the lever away from the motor. It will re-engage
automatically, once the lever is released. The lever, when not used, is at-
tached to the motor's cooling fins with clamps.
The screw-type “BMHF” (5) arrangement requires a hexagon key which,
when turned clockwise, opens the brake.
Since the stationary disc (22) will move away from the coil body during
the brake's operation, it is vital that there is free play (floating clearance)
on the release arm of 0.060"-0.080" (1.5-2.0 mm). The springs (11)
should be placed between the arm (7) and the nuts (12) to eliminate noise.
The brake release mechanism is not used to change the brake's
torque setting. There must always be clearance on the lever.
Fault: Motor does not run
1.
Check the motor and brake wiring for damage and proper connection.
2.
At the motor, measure the line voltage, line current and motor resis-
tance of all three phases.
3.
If all three phases read a similar current value the following condi-
tions may exist:
•
The motor may be blocked by either an excessive external load, or
problems in the reducer or the brake. In both cases, the motor
should draw locked rotor (in-rush) current. Consult
SEW-
Eurodrive catalogs for these values. Release the brake mechani-
cally, reset the air gap if needed, or disconnect the load from the
output shaft.
•
If the brake is at fault electrically see #4 below.
•
If the current differs significantly from the rated locked rotor cur-
rent, the motor is either an incorrect voltage, or it is jumpered for the
wrong voltage.
4.
If the brake can be released mechanically, but does not respond to
voltage, check the brake for electrical problems.
•
Make sure the wiring is according to the instructions. Pay special
attention to the brake voltage.
•
Energize the brake circuit and measure the AC voltage on the recti-
fier terminals 2 and 3 (BG/BGE rectifiers). The measured voltage
should correspond to the nameplate inscription: “Brake V.”
•
Measure the DC voltage across terminals 3 and 5 of the brake recti-
fier which should be about 35% to 45% of the previously measured
AC voltage.
•
If there is no fault found to this point, measure the resistance of the
brake coils. Disconnect the coil from the rectifier for this measure-
ment. See the table on Page 2 for the brake coil resistance values.
•
Measure the resistance of each brake coil lead to the brake coil
body. This test should show an open circuit. If a short is found, the
brake coil is damaged.
If the results of all these checks (electrical connection, mechanical checks
and adjustments, and electrical tests) indicate that the brake should work,
then the most likely cause of the brake's failure to release is a damaged
brake rectifier.
Fault: Brake stopping time is too slow
If the brake has been operating well for some time and a gradual increase
in stopping time has occurred, the release arm may have come in contact
with the coil body. Verify that the brake release arm end play is correct,
and check for excessive brake disc wear, (see previous instructions).
If the brake has been in operation for some time, and the stopping has be-
come erratic, dust accumulation around the stationary disc guides may be
the cause. Remove the brake's rubber sealing collar and clean with an air
hose.
If the application is new, check the brake's wiring and air gap. If the brake
is not wired for fast response, then changing the brake wiring to fast re-
sponse will decrease the stopping time. Vertical motion and indexing ap-
plications may also require the fast response connection. Increasing the
brake's torque may remedy the situation, but will also increase stress on
the transmission.
On applications requiring excessive brake work, the lining's surface may
become glazed due to extreme heat. The application of a BGE rectifier
will improve this situation dramatically. BGE rectifiers are standard
equipment on motors size DV 112 - DV225, but optional on the smaller
sizes DT71-DT100. Contact SEW-Eurodrive for more information.
Motor Size
Brake Size
Air Gap
DT71 - DT100
BM(G)05 - BM(G)4
0.010"-0.024" (0.25-0.6 mm)
DV112 - DV225
BM(G)8 - BM31
0.012"-0.047" (0.3-1.2 mm)
DV180-DV225
BM32-BM62
Double Disc
0.016"-0.047" (0.4-1.2 mm)
4
Summary of Contents for LM1010-2x
Page 5: ...4...
Page 8: ...7 LM Control Box Overlay...
Page 15: ...14 LM Machine PARTS View...
Page 17: ...16 LM 2x Back gauge Crank Assembly...
Page 21: ...20 LM 2x Back gauge Drive Assembly...
Page 26: ...25 LM1010 WIRING DIAGRAM...