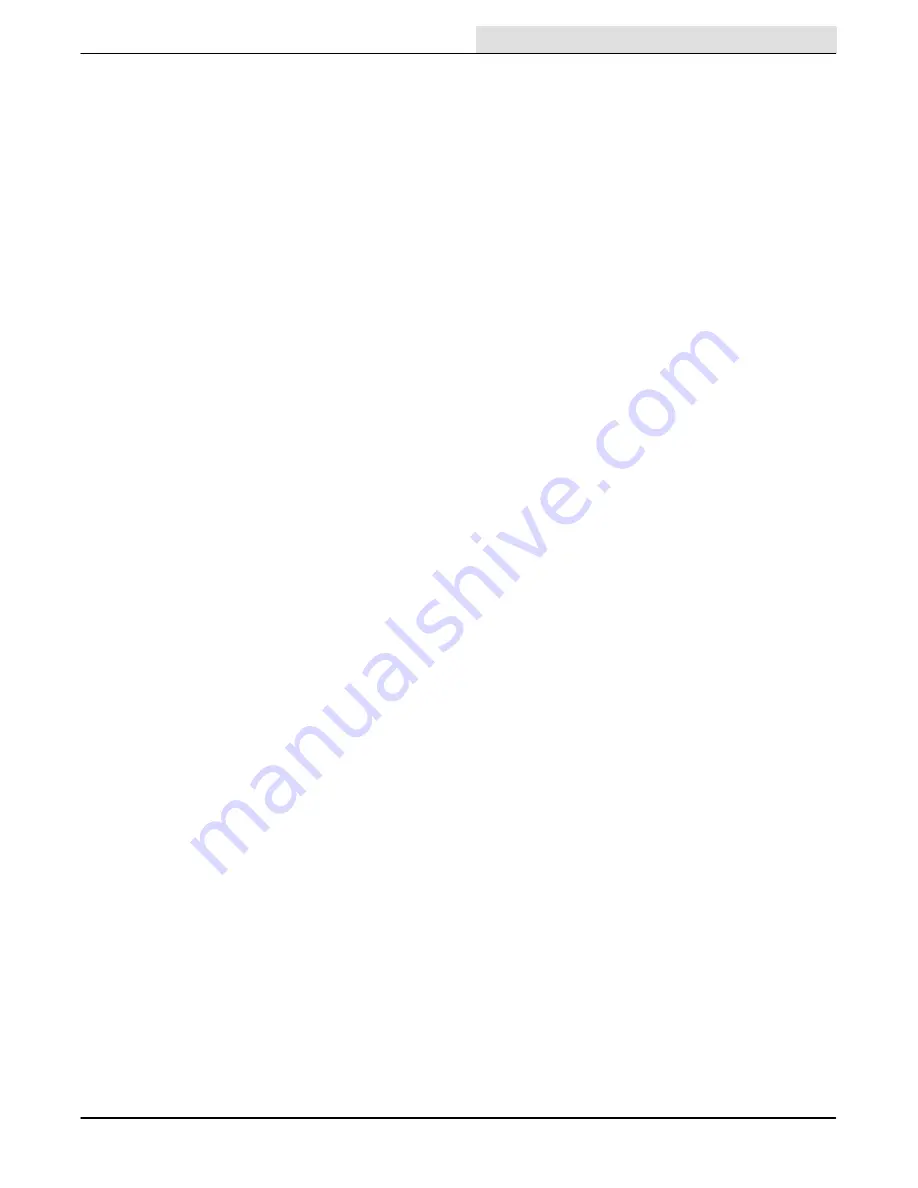
APPENDIX
4-1
255 SERIES II MM189 (12---89)
SECTION 4
CONTENTS
Page
HARDWARE INFORMATION
4-3
. . . . . . . . . . . . . . . .
STANDARD BOLT TORQUE CHART
4-3
. . . . . .
METRIC BOLT TORQUE CHART
4-3
. . . . . . . . .
BOLT IDENTIFICATION
4-3
. . . . . . . . . . . . . . . . .
THREAD SEALANT AND LOCKING
COMPOUNDS
4-3
. . . . . . . . . . . . . . . . . . . . . .
HYDRAULIC FITTING INFORMATION
4-4
. . . . . . . .
HYDRAULIC TAPERED PIPE FITTING (NPT)
TORQUE CHART
4-4
. . . . . . . . . . . . . . . . . . . .
HYDRAULIC TAPERED SEAT FITTING (JIC)
TORQUE CHART
4-4
. . . . . . . . . . . . . . . . . . . .
HYDRAULIC O---RING FITTING
TORQUE CHART
4-4
. . . . . . . . . . . . . . . . . . . .
Summary of Contents for 255 Series II
Page 1: ...r 255 Series II Sweeper Scrubber...
Page 6: ...ABOUT THIS MANUAL 255 SERIES II MM189 12 89 d...
Page 16: ...GENERAL INFORMATION 255 SERIES II MM189 6 90 x...
Page 18: ...SPECIFICATIONS 255 SERIES II MM189 12 89 1 2...
Page 22: ...SPECIFICATIONS 255 SERIES II MM189 NIL 1 6...
Page 24: ...OPERATION 255 SERIES II MM189 12 89 2 2...
Page 60: ...OPERATION 255 SERIES II MM189 12 89 2 38...
Page 74: ...MAINTENANCE 255 SERIES II MM189 12 89 3 14 04624 HYDRAULIC SCHEMATIC LOW DUMP MODEL...
Page 75: ...MAINTENANCE 3 15 255 SERIES II MM189 12 89 04625 HYDRAULIC SCHEMATIC MULTI LEVEL DUMP MODEL...
Page 94: ...MAINTENANCE 255 SERIES II MM189 12 89 3 34 04642 ELECTRICAL SCHEMATIC ACCESSORIES...
Page 95: ...MAINTENANCE 3 35 255 SERIES II MM189 6 90 06187 ELECTRICAL SCHEMATIC AUTO SHAKER RFS...
Page 96: ...MAINTENANCE 255 SERIES II MM189 6 90 3 36 06187 ELECTRICAL SCHEMATIC AUTO SHAKER RFS...
Page 124: ...MAINTENANCE 255 SERIES II MM189 6 90 3 64...