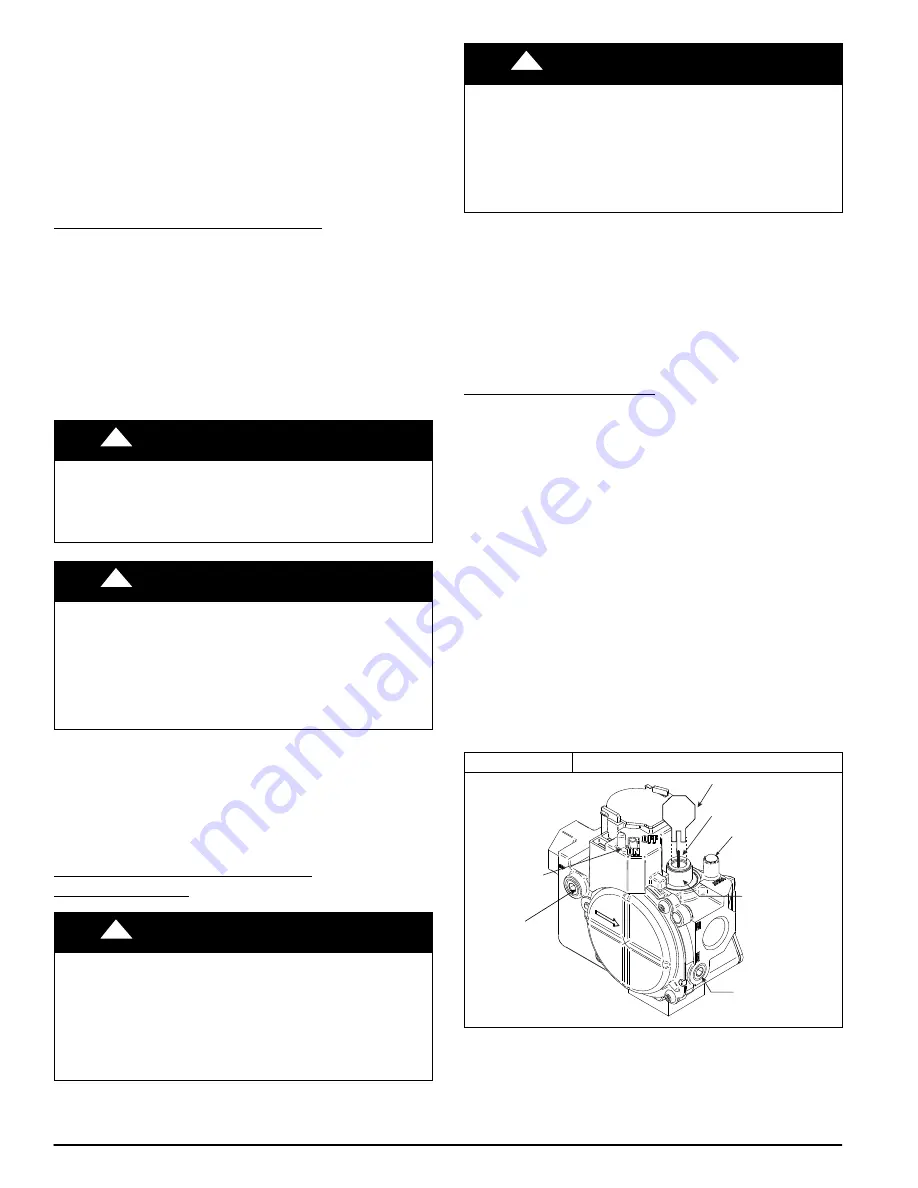
14
443 06 4001 01
Specifications subject to change without notice.
NOTE
: Use only propane
−
resistant pipe dope. Do not use
Teflon tape.
9. Insert the gas pipe through the grommet in the casing.
Apply a thin layer of pipe dope to the threads of the pipe
and thread the pipe into the gas valve.
NOTE
: Use a back
−
up wrench on the gas valve to prevent the
valve from rotating on the manifold or damaging the mounting
to the burner box.
10. With a back
−
up wrench on the inlet boss of the gas
valve, finish tightening the gas pipe to the gas valve.
CHECK INLET GAS PRESSURE
NOTE
: This kit is to be used only when inlet gas pressure is
between 4.5-in. w.c. and 13.6-in. w.c.
.
Natural gas service
pressure must not exceed 0.5 psig (14
−
in. w.c.) but be no less
than 0.16 psig (4.5
−
in. w.c.).
NOTE
: Verify NAT arrow on LP/NAT cap is pointed toward gas
valve.
1. Verify manometer is connected to inlet pressure tap on
gas valve. (See
Figure 23
)
2. Turn on furnace power supply.
3. Turn gas supply manual shutoff valve to ON position.
!
WARNING
FIRE, EXPLOSION, ELECTRICAL SHOCK HAZARD
Failure to follow this warning could result in personal injury,
death or property damage.
Gas supply MUST be shut off before disconnecting electrical
power before proceeding with conversion.
!
WARNING
ELECTRICAL SHOCK, FIRE OR EXPLOSION HAZARD
Failure to follow this warning could result in personal injury,
death or property damage.
Before installing, modifying, or servicing system, main
electrical disconnect switch must be in the OFF position and
install a lockout tag. There may be more than one disconnect
switch. Lock out and tag switch with a suitable warning label.
Verify proper operation after servicing.
4. Turn furnace gas valve switch to ON position.
5. Jumper R
−
W thermostat connections on control.
6. When main burners ignite, confirm inlet gas pressure is
between 4.5
−
in. w.c. and 13.6
−
in. w.c.
7. Remove jumper across R
−
W thermostat connections to
terminate call for heat.
8. Turn furnace gas valve switch to OFF position.
CHECK FURNACE AND MAKE
ADJUSTMENTS
!
WARNING
FIRE AND EXPLOSION HAZARD
Failure to follow this warning could result in personal injury
and/or death.
NEVER test for gas leaks with an open flame. Use a
commercially available soap solution made specifically for
the detection of leaks to check all connections. A fire or
explosion may result causing property damage, personal
injury or loss of life.
!
AVERTISSEMENT
RISQUE D’EXPLOSION ET D’INCENDIE
Le fait de ne pas suivre cet avertissement pourrait entraîner
des dommages corporels et / ou la mort.
Ne jamais examiner pour les fuites de gaz avec une flamme
vive. Utilisez plutôt un savon fait specifiquement pour la
détection des fuites de gaz pour verifier tous les connections.
Un incendie ou une explosion peut entrainer des dommages
matériels, des blessures ou la mort.
1. Be sure main gas and electric supplies to furnace are off.
2. Remove 1/8
−
in. (3 mm) pipe plug from manifold pressure
tap on downstream side of gas valve.
3. Attach manometer to manifold pressure tap on gas
valve. (See
Figure 13
)
4. Turn gas supply manual shutoff valve to ON position.
5. Turn furnace gas valve switch to ON position.
6. Check all threaded pipe connections for gas leaks.
7. Turn on furnace power supply.
SET GAS INPUT RATE
1. Jumper R and W thermostat connections to call for heat.
(See
Figure 20
)
2. Check manifold orifices for gas leaks when main burners
ignite.
3. Adjust manifold pressure to obtain input rate. (See
Table 3
)
4. When main burners have ignited, confirm proper
manifold pressure is between 3.2
−
in. w.c. and 3.8
−
in.
w.c. (See
Table 3
)
5. If manifold pressure needs to be adjusted, use gas valve
adjustment key, factory
−
supplied in this kit or adhesive
pouch. (See
Figure 25
)
6. Remove cap that conceals adjustment screw for gas
valve regulator. (See
Figure 25
)
7. Turn adjusting screw using supplied ADJUSTING KEY
either counterclockwise (out) to decrease input rate or
clockwise (in) to increase rate. (See
Figure 25
)
8. Replace cap and check rate. Cap MUST be in place to
actuate regulator.
9. Repeat Steps 5 through 8 until correct input rate is
obtained.
Figure 25
Manifold Pressure Adjustment Key
ON/OFF SWITCH
INLET
PRESSURE TAP
REGULATOR PLUNGER
ADJUSTING KEY
GAS PRESSURE
REGULATOR
MANIFOLD
PRESSURE TAP
BURNER REFERENCE
PRESSURE TAP
A11509
NOTE
: Gas valve LP/NAT cap MUST be in place with NAT
arrow pointing toward gas valve when checking input rate.
When correct input is obtained, main burner flame should be
clear blue, almost transparent (See
Figure 22
). Be sure cap is
in place when finished.