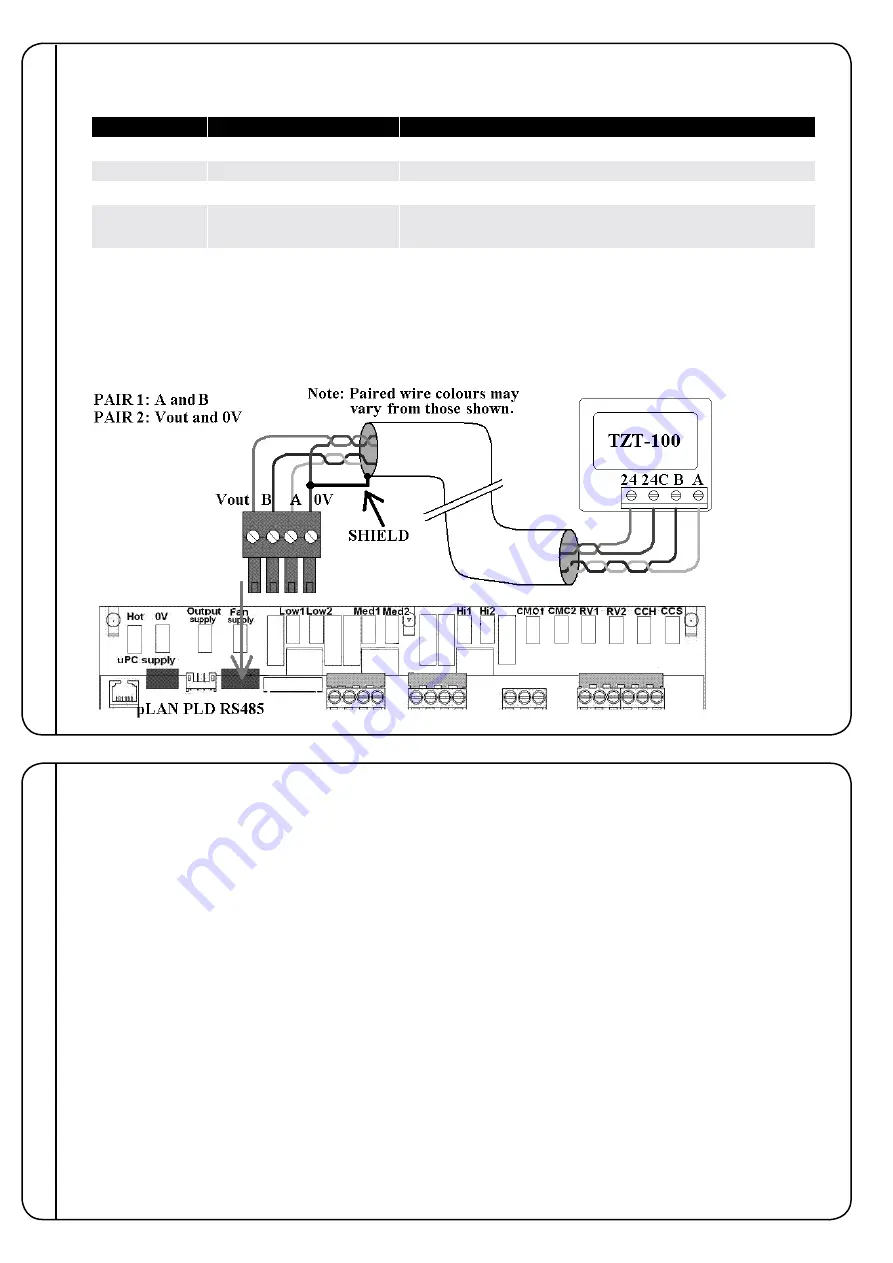
- 8 -
C
O
M
M
U
N
IC
A
TION
P
O
R
TS
M
A
IN
TE
NAN
C
E
11. COMMUNICATION PORTS
11.1 Several types of communication ports are available on the UC6.
Note 1: Connectors to the UC6 show R+/T+ for signal A, R-/T- for signal B.
11.2 Temperzone TZT-100 thermostat connection
The UC6 can connect directly to the temperzone TZT-100 thermostat using a shielded cable with two twisted pair wires
suitable for RS85 serial communications. The drawing below shows connection details.
COMM PORT
Signal
Notes
RS485
1
Modbus / CAREL RS485
Thermostat, Inverter
pLAN
UC6 service tool
Programmable graphic display
PLD
1
Fieldbus (RS485 or TLan)
Supervisory System
BMS
Modbus RS485, or
BACnet TCP/IP
Available only with additional plug-in module connected to the
“BMS” connector (adjacent to the Digital Input connector).
12. MAINTENANCE
WARNING HAZARDOUS VOLTAGE. ENSURE ALL POWER SUPPLIES
ARE ISOLATED BEFORE PERFORMING MAINTENANCE. FAILURE TO
ISOLATE POWER CAN LEAD TO SERIOUS INJURY.
12.1 Monthly
1. Check air filters, if fitted, and vacuum or wash clean
as necessary.
2. Check condensate drain for free drainage.
3. Check compressor compartment for oil stains
indicating refrigerant leaks.
4. Check system operating pressures and history using
PDG mini service interface tool fitted to all ECO
machines
12.2 Three Monthly (or every 1200 hrs of operation)
Check the indoor unit’s indoor EC motor and plug fan
operation and adjust if necessary, using PDG mini
service interface tool fitted to all ECO machines.
12.3 Six Monthly
1. Check the tightness of electrical connections.
2. Check the tightness of all fans, motor mountings
3. Check suction and discharge operating pressures
using PDG mini service interface tool fitted to all ECO
machines
4. Check and or Replace indoor air filters
5. Check condensate drain for free drainage.
12.4 Yearly
1. Check all refrigerant piping for chafing and vibration.
2. Check the operation of electric heaters, if fitted
3. Check air supply at all diffusers
4. Check for excessive noise and vibration and correct
as necessary.
5. Check for insulation and duct damage and repair
as necessary.
6. Check system operating pressures and history using
PDG mini service interface tool fitted to all ECO
machines
7. Remove lint and dust accumulation from outdoor
coil fins with soft brush or low pressure water spray.
8. Touch up any paintwork damage to prevent corrosion.
NOTE: The manufacturer reserves the right to make changes
in specifications at any time without notice or obligation.
Certified data is available on request.
Summary of Contents for OPA 465RKTG-P
Page 10: ... 10 OPA 465RKTG P ...
Page 11: ... 11 OPA 550RKTG P ...
Page 12: ... 12 OPA 705RKTG P ...
Page 13: ... 13 OPA 800RKTG P ...
Page 14: ... 14 OPA 855RKTG P ...
Page 15: ...OPA 960RKTG P ...