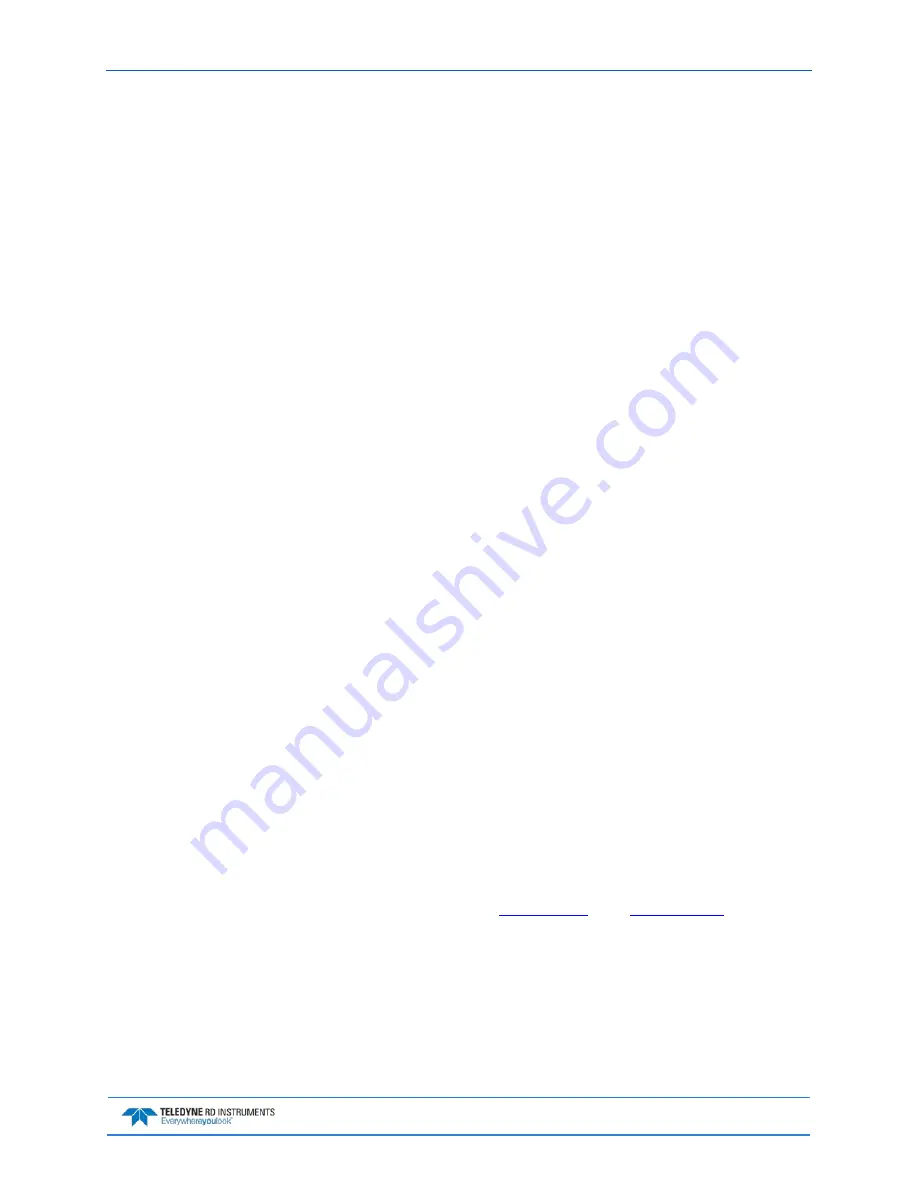
Pathfinder DVL Guide
April
2018
EAR-Controlled Technology Subject to Restrictions Contained on the Cover Page.
Page 43
Acoustic Integration Considerations
Flow Noise
Water flowing over the transducer faces increases the acoustic noise level, which in turn decreases the op-
erational range of the DVL. Flow noise can be reduced across the transducer faces by mounting the DVL
behind a sea chest, fairing, or acoustic window. Flow noise can also be reduced by optimizing the trans-
ducer head type and design to conform to the platform hull form being used. Optimized transformer
heads are can be custom made by Teledyne RD Instruments for specialized applications and may exist as
commercial off the shelf product for more standard applications.
Cavitation
Cavitation is the formation of air bubbles due to the reduction of ambient pressure because of hydrody-
namic flow conditions. Cavitation at the edges of the transducer or surrounding area near the trans-
ducer often results in increased acoustic noise, and a corresponding reduction in operating range. As with
flow noise, cavitation can also be reduced by optimizing the transducer head type and design to the plat-
form hull form being used.
Ringing
Definition
: Ringing occurs in DVLs when the energy from the side lobes of the transmitted signal excites
the metal portion of the DVL transducer such that a resonant condition occurs. This causes the transducer
and anything attached to it to resonate at the system’s transmit frequency. While some ringing is nor-
mal in DVLs its magnitude must be minimized.
It is helpful to review the transmitted acoustic signal associated with DVLs in order to fully characterize
the phenomenon of ringing. The DVL transmits an acoustic pulse into the water. The main lobe of this
pulse bounces off of the sea bottom (bottom track) or particles in the water column (water track) and the sig-
nals returned from these particles are used to calculate the velocity of the water.
Along with the main lobe of the transmitted pulse are many associated side lobes. It is these side lobes
that come in contact with metal the housing of the DVL transducer and as noted above are the source of
the ringing.
If the DVL is in the receive mode while the transducer is ringing, then it will receive both the return sig-
nals from the water and the “ringing.” Both of these signals are then processed by the DVL. The ringing
causes bias to the velocity data.
All DVLs “ring” for some amount of time. Therefore, each DVL requires a blanking period (time of no data
processing) to keep from processing the ringing energy. During this time the transmitted pulse is traveling
away from the DVL at the speed of sound, so this “blanking period” corresponds to a range near the DVL
that cannot be profiled. Each DVL frequency has a different typical ringing duration.
These typical ringing values are recommended as the minimum setting for all DVLs using default set-
ups (minimum value for the blanking period as set by the #
and #
).
It should be noted, on some installations the effects of ringing will last longer than the recommended set-
tings above.