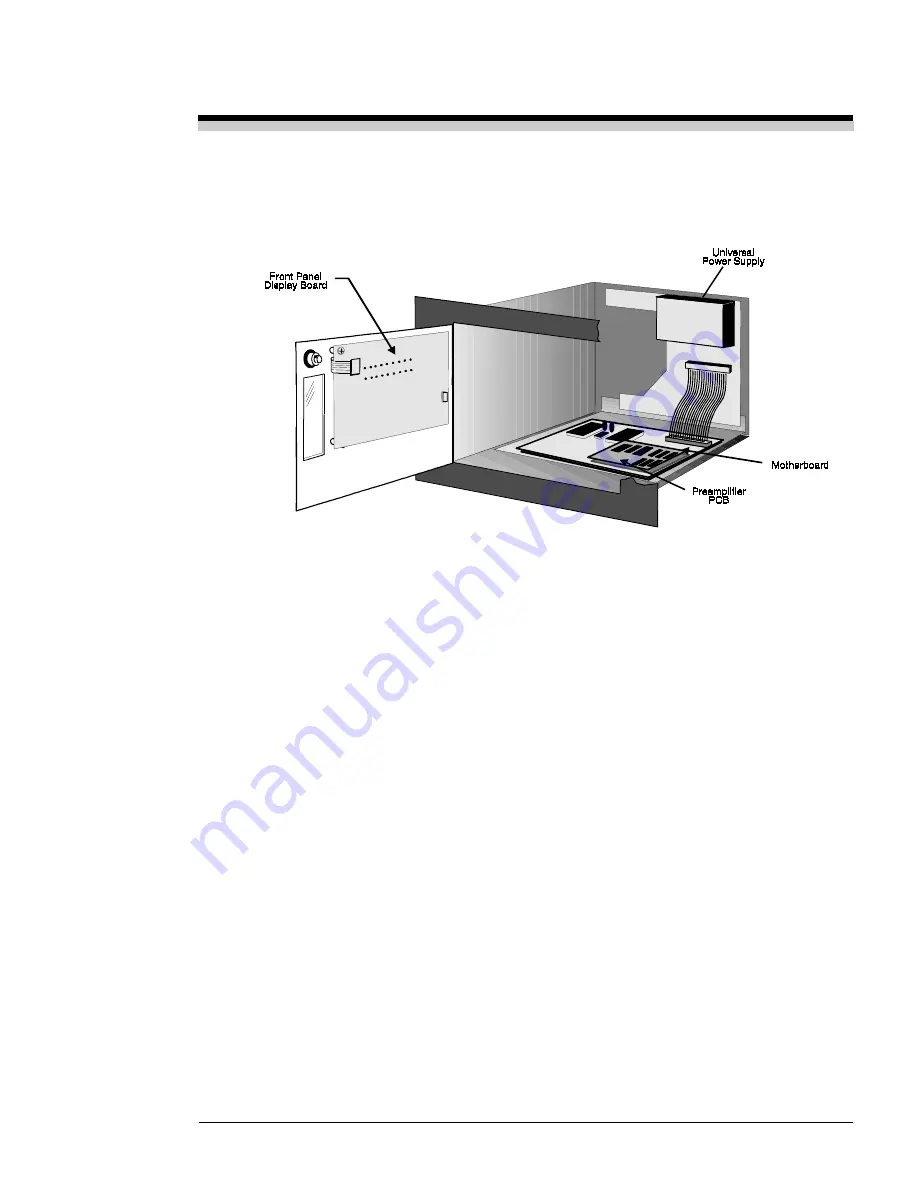
Part I: Control Unit
Maintenance 5
Part I: 5-3
5.3
Major Internal Components
The major components in the Control Unit are shown in Figure 5-3.
Figure 5-3: Control Unit Major Internal Components
WARNING: HAZARDOUS VOLTAGES EXIST ON CERTAIN COM-
PONENTS INTERNALLY WHICH MAY PERSIST FOR
A TIME EVEN AFTER THE POWER IS TURNED OFF
AND DISCONNECTED.
The 3010PA Control Units contain the following major components:
•
Power Supply
•
Motherboard (with Microprocessor, RS-232 chip, and
Preamplifier PCB)
•
Front Panel Display Board and Displays—
5 digit LED meter
2 line, 20 character, alphanumeric, VFD display
See the drawings in the Drawings section in back of this manual
for details.
The Front Panel Display Board is accessed by unlatching and swing-
ing open the front panel, as described earlier. Other electronic components
are accessed by removing four rear panel screws and sliding out the entire
chassis. See Figure 5-4, below.
Summary of Contents for 3010PA
Page 17: ...1 6 Part I 1 Introduction Model 3010PA ...
Page 21: ...2 4 Part I 2 Operational Theory Model 3010PA ...
Page 57: ...iv Part II Model 3010P Oxygen Analyzer ...
Page 69: ...2 8 Part II 2 Operational Theory Model 3010P ...
Page 77: ...3 Installation Model 3010P 3 8 Part II ...