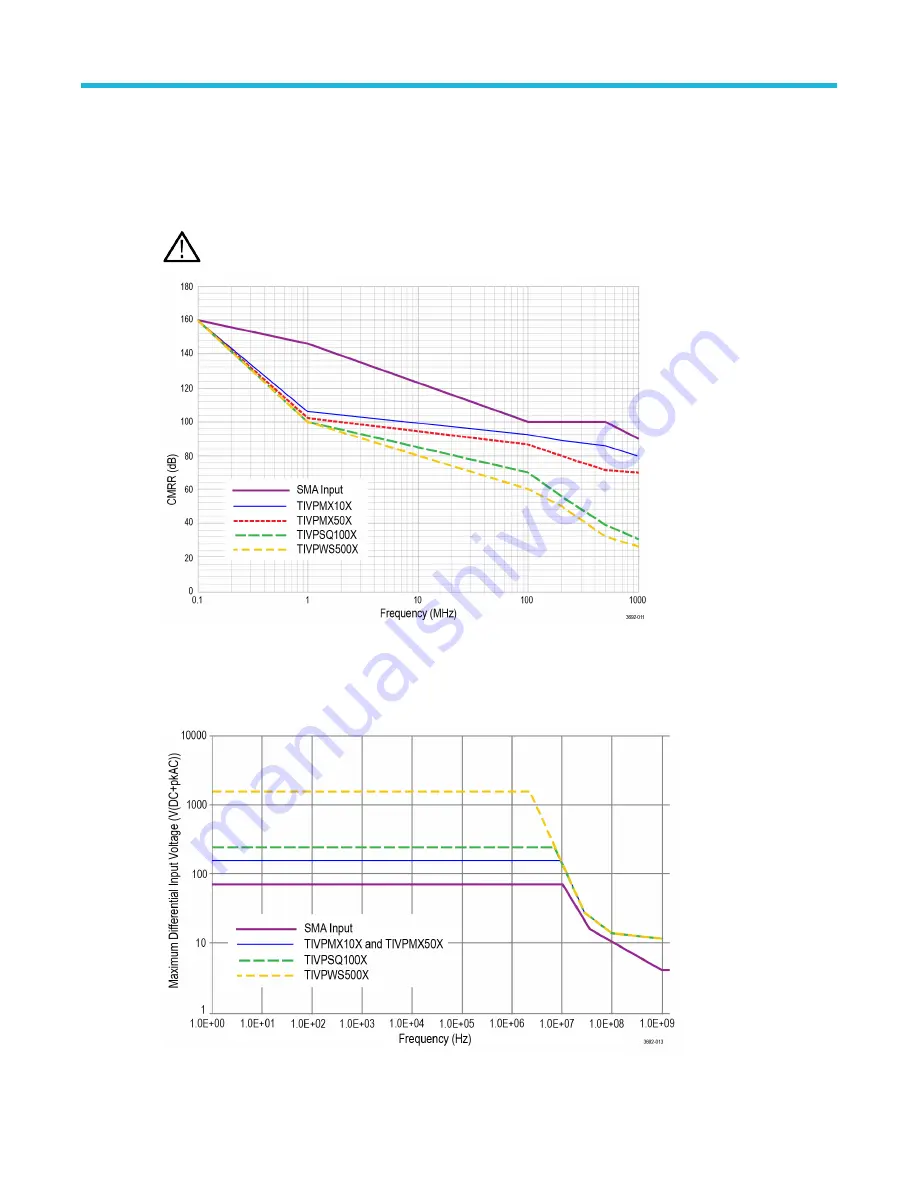
Common mode rejection ratio graphs
The ability to measure common mode rejection ratios (CMRR) of the IsoVu system below 100 kHz is limited by the dynamic
range of test systems. Due to the optical isolation of the IsoVu sensor head, the DC CMRR performance of all tip cables is
expected to be greater than 160 dB.
The following figure shows the typical CMRR values for the supported sensor tip cables.
Note: The values for the TIVPMX50X, TIVPSQ100X, and TIVPWS500X sensor tip cables are preliminary.
Figure 7: Typical CMRR values for the sensor tip cables
Maximum differential input voltage vs frequency derating graphs
The following figure shows the derating values for the supported sensor tip cables.
Figure 8: Maximum differential input voltage vs. frequency for the sensor tip cables
Reference information
TIVP Series IsoVuTM Measurement System User Manual
37