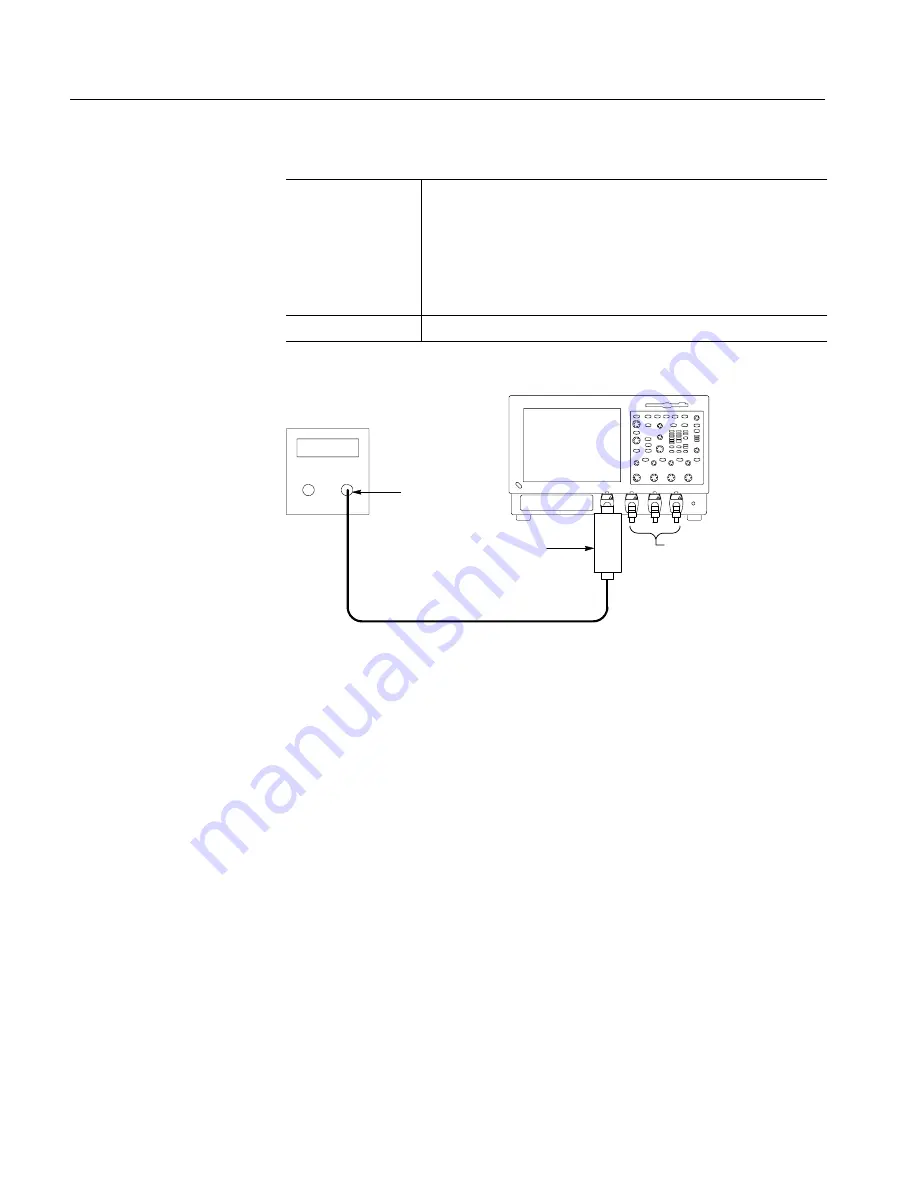
Performance Tests
4- 86
CSA7404B, TDS7704B, TDS7404B, TDS7254B & TDS7154B Service Manual
Equipment
required
One leveled sine-wave generator (Item 12)
One 2X attenuator (Item 26)
Four TCA-BNC adapters (Item 19)
Three 50
Ω
terminations (Item 3)
One 50
Ω
, precision coaxial cable (Item 4)
Prerequisites
See page 4--17
Instrument under test
50
Ω
Coaxial cable
Output
Leveled
sine wave
generator
2X Attenuator
50
Ω
Terminations
Figure 4- 19: Initial test hookup
1.
Install the test hookup and preset the instrument controls:
a.
Initialize the instrument:
Press the
DEFAULT SETUP
button.
b.
Modify the initialized control settings:
H
Turn on all vertical channels (press the Vertical button of any off
channels: CH 1, CH 2, CH 3, and CH 4).
H
Set the Horizontal SCALE to
1 ns
.
H
Set the Vertical SCALE of CH 1, CH 2, CH 3, and CH 4 to
100 mV
.
H
From the tool bar, touch
Horiz
and select the
Acquisition
tab. Set
the acquisition mode as follows:
TDS7704B: Touch
Sample
.
All other CSA/TDS7000B: Touch
Average
, set the number of
averages to
16
.
Check Channel Isolation
(Crosstalk)
Summary of Contents for CSA7404B
Page 4: ......
Page 14: ...Table of Contents x CSA7404B TDS7704B TDS7404B TDS7254B TDS7154B Service Manual ...
Page 18: ...Service Safety Summary xiv CSA7404B TDS7704B TDS7404B TDS7254B TDS7154B Service Manual ...
Page 20: ...Environmental Considerations xvi CSA7404B TDS7704B TDS7404B TDS7254B TDS7154B Service Manual ...
Page 23: ...Specifications ...
Page 24: ......
Page 55: ...Operating Information ...
Page 56: ......
Page 69: ...Theory of Operation ...
Page 70: ......
Page 74: ...Theory of Operation 3 4 CSA7404B TDS7704B TDS7404B TDS7254B TDS7154B Service Manual ...
Page 75: ...Performance Verification ...
Page 76: ......
Page 80: ...Performance Verification 4 4 CSA7404B TDS7704B TDS7404B TDS7254B TDS7154B Service Manual ...
Page 92: ...Brief Procedures 4 16 CSA7404B TDS7704B TDS7404B TDS7254B TDS7154B Service Manual ...
Page 120: ...Performance Tests 4 44 CSA7404B TDS7704B TDS7404B TDS7254B TDS7154B Service Manual ...
Page 215: ...Adjustment Procedures ...
Page 216: ......
Page 218: ...Adjustment Procedures 5 2 CSA7404B TDS7704B TDS7404B TDS7254B TDS7154B Service Manual ...
Page 219: ...Maintenance ...
Page 220: ......
Page 228: ...Maintenance 6 8 CSA7404B TDS7704B TDS7404B TDS7254B TDS7154B Service Manual ...
Page 308: ...Troubleshooting 6 88 CSA7404B TDS7704B TDS7404B TDS7254B TDS7154B Service Manual ...
Page 310: ...Repackaging Instructions 6 90 CSA7404B TDS7704B TDS7404B TDS7254B TDS7154B Service Manual ...
Page 311: ...Options ...
Page 312: ......
Page 319: ...Replaceable Electrical Parts ...
Page 320: ......
Page 322: ...Electrical Parts List 8 2 CSA7404B TDS7704B TDS7404B TDS7254B TDS7154B Service Manual ...
Page 323: ...Diagrams ...
Page 324: ......
Page 327: ...Replaceable Mechanical Parts ...
Page 328: ......
Page 348: ...Mechanical Parts List 10 20 CSA7404B TDS7704B TDS7404B TDS7254B TDS7154B Service Manual ...