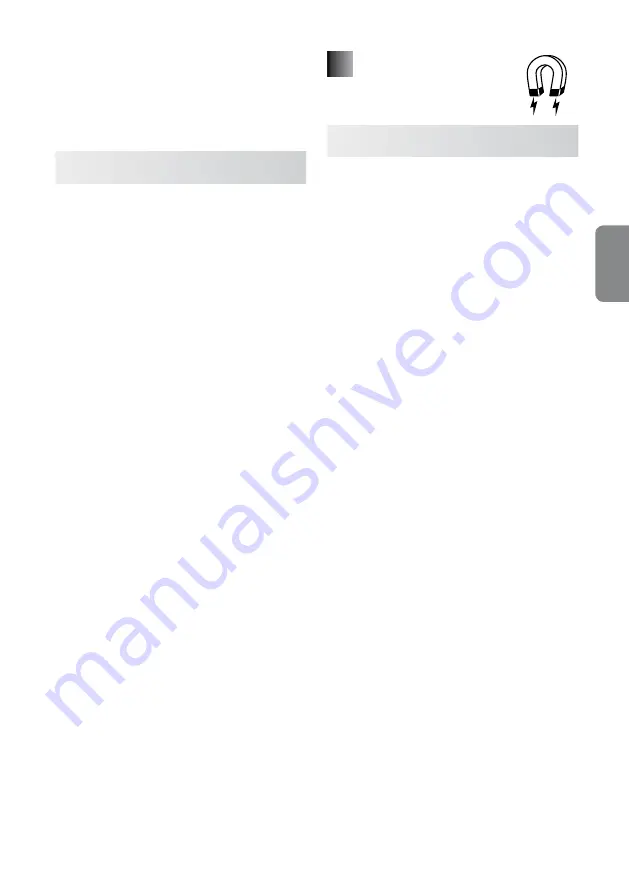
47
Instruction and maintenance manual
ENGLISH
have to be adopted in order to protect it from dam-
ages caused by potential impacts. In order to protect
the system from atmospheric agents, lubricate it
with anti-corrosion oils and place hygroscopic salts
in the box. All parts that cannot be permanently fixed
in place must be removed.
2.4 Storage
Before removing the system from service or storing it
for long periods of time, always thoroughly clean it in
order to remove machining scraps and protect all
visible metal parts with protective oils or greases to
prevent the surfaces from oxidizing.
Disconnect the controller from the magnetic chuck
and from the power supply.
It is generally advisable to cover the system with a
waterproof sheet and store it in dry and safe place.
The temperature of the storage area should range
between 0°C (32°F) and 55°C (131°F).
Relative humidity should be between 30% and 90%,
non condensing.
The atmosphere should be clean, free from acids,
corrosive gases, salts, etc.
Always restart the system in accordance with the in-
structions provided in Chapter 6.
3
DESCRIPTION OF
THE SYSTEM
3.1 Advantages
The best possible clamping conditions that a tooling
machine can offer are as follows:
1) Firmly fix the part that has to be machined
2) Verify that the tool is able to access the surfaces
that have to be machined.
Magnetic clamping systems offer the advantage of
combining the best of these two operating condi-
tions:
1) The clamping forces generated by magnetic sys-
tems are evenly distributed along all contact sur-
faces, in addition to having an intrinsic strength.
2) The part that has to be machined is clamped only
along the contact surface, so that the remaining
surfaces can be accessed by the tool.
The substantial difference in distribution of the
clamping forces account for the greater perform-
ances offered by magnetic systems as compared to
traditional mechanical systems. Some of the main
advantages include:
a) The high clamping force of magnetic systems is
consistently distributed on all surface of the part
to clamp. This can be particularly useful when
clamping sensitive pars like those with a small
thickness or that tend to easily deform.
b) The working principle of magnetic systems offers
the unparalleled advantage of significantly reduc-
ing vibrations created by machining. This means
that it is possible to remove materials at greater
speed and perform more accurate machining op-
erations.
European standards concerning the safety of work plac-
es and electromagnetic compatibility clearly emphasize
the superiority of permanent-electro magnetic systems
as compared to electromagnetic ones, because they
do not require a continuous source of external energy,
except for the clamping and release phases, and do not
affect the operation of other equipment as they do not
return any form of energy to the network.
Magnetic clamping systems ensure a continuous air
flow. The system is not dependant on external energy
sources while the tool machining is in progress, which
means that if a power failure occurs, the clamping forc-
es are not affected and are therefore able to continue
clamping the part.