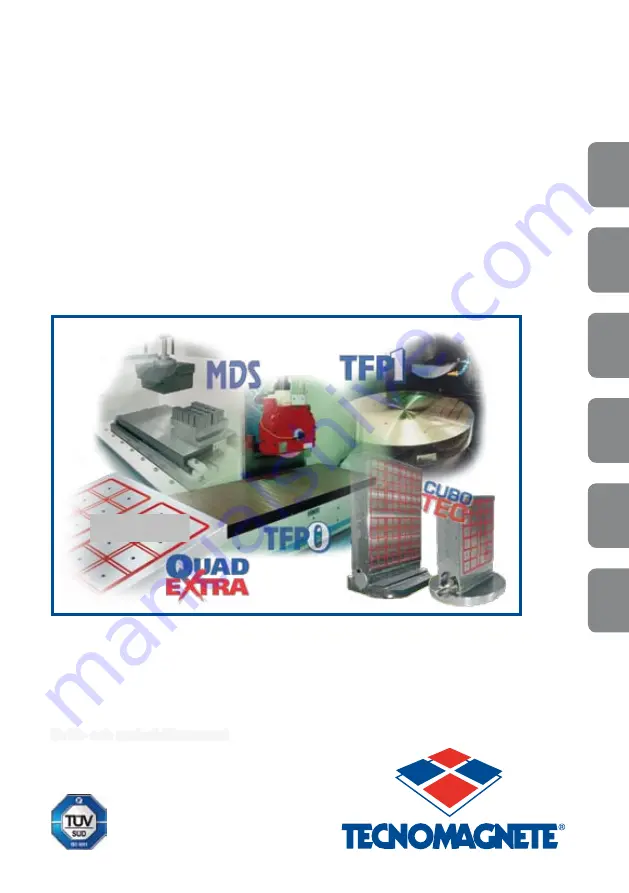
IT
ALIANO
ENGLISH
FRANÇAIS
DEUTSCH
ESP
AÑOL
IT
ALIANO
ENGLISH
FRANÇAIS
DEUTSCH
ESP
AÑOL
SVENSKA
SISTEMI MAGNETICI ELETTROPERMANENTI
Divisione ancoraggio macchine utensili - serie rettifica e fresatura
PERMANENT-ELECTRO MAGNETIC SYSTEMS
Clamping Tool Machines Division - Systems for grinding and milling operations
SYSTÈMES MAGNÉTIQUES ÉLECTROPERMANENTS
Section serrage machines-outils - série rectification et fraisage
ELEKTROPERMANENTE MAGNETSYSTEME
Abteilung Verankerung von Werkzeugmaschinen - Serie Schleifen und Fräsen
SISTEMAS MAGNÉTICOS ELECTROPERMANENTES
División anclaje sobre máquinas herramienta - serie rectificado y fresado
ELEKTROPERMANENTA MAGNETSYSTEM
Avdelning för fästanordningar till verktygsmaskiner - serie för finslipning och fräsning
Manuale uso e manutenzione
Instruction and maintenance manual
Manuel d’utilisation et d’entretien
Betriebs- und Wartungsanleitung
Manual de uso y mantenimiento
Drift- och underhållsmanual
Nr. 50 100 7816
MILL TEC