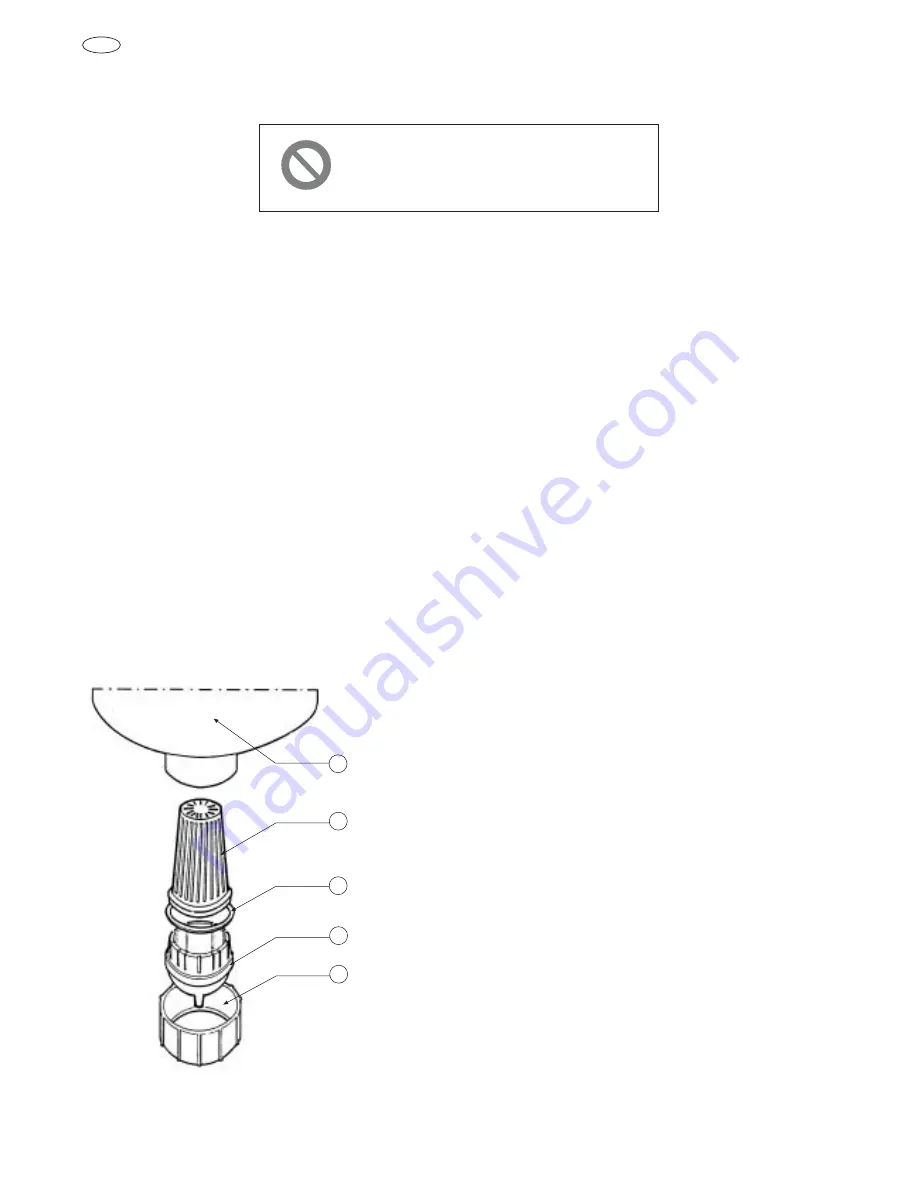
GB
16
6. MAINTENANCE
W
W
W
W
A
A
A
A
R
R
R
R
N
N
N
N
II
II
N
N
N
N
G
G
G
G
!!
!!
!!
!!
!!
!!
THIS PROCEDURE MAY ONLY BE DONE
BY AN AUTHORISED TECNOMAC
INSTALLATION TECHNICIAN
Regular maintenance is limited to descaling or
replacing the boiler, together with annual
cleaning (generally done before seasonal
close-down).
CYLINDER BOILER CLEANING
AND REPLACEMENT
This is necessary when scale on the active sur-
faces of the electrodes prevents the sufficient
passage of electrical current (alarms E08 and
E06).
To dismantle the cylinder boiler:
– drain water completely, by pressing MANUAL
DRAIN button 11) on the control panel;
– cut of power to the equipment by means of
switch or line fuses;
– remove steam pipe from the boiler;
– disconnect wiring to main electrodes and
unplug light level electrodes;
– unscrew fixing knob to free cylinder, lift boiler
to remove. The boiler may generally be used
again after descaling. Unscrew ring nut (see
figure) and extract bottom filter. Remove
scale and calcareous deposits under a jet of
water and clean grids mechanically or chem-
ically with a commercially available cleaner.
When electrode wear is such that regenera-
tion is insufficient, the boiler must be
replaced. Exchange only involves the body
of the boiler and the gasket. The ring nut,
connection piece and filer do not deteriorate
with use.
Reassemble the boiler in reserve sequence,
after, checking and if necessary the washer
between the threaded connection and the dis-
charge group.
CLEANING AND SEASONAL
CLOSE-DOWN
Annually, or before summer close-down,
inspect and clean the systems. Drain water
from the boiler by pressing the MANUAL
DRAIN pushbutton 11) on the control panel
and cutting off power.
The following is Recommended:
– dismantle and wash water intake valve, and
check that intake filter is clean;
– dismantle drain group, cleaning conduits and
nozzles and removing and solids from the
base of the syphon;
– inspect water intake, drain, steam and con-
densation pipes, and replace them it they are
worn out or fragile.
5
4
1
3
2
1. RING NUT
2. CONNECTION PIECE
3. GASKET
4. FILTER
5. CYLINDER BOILER