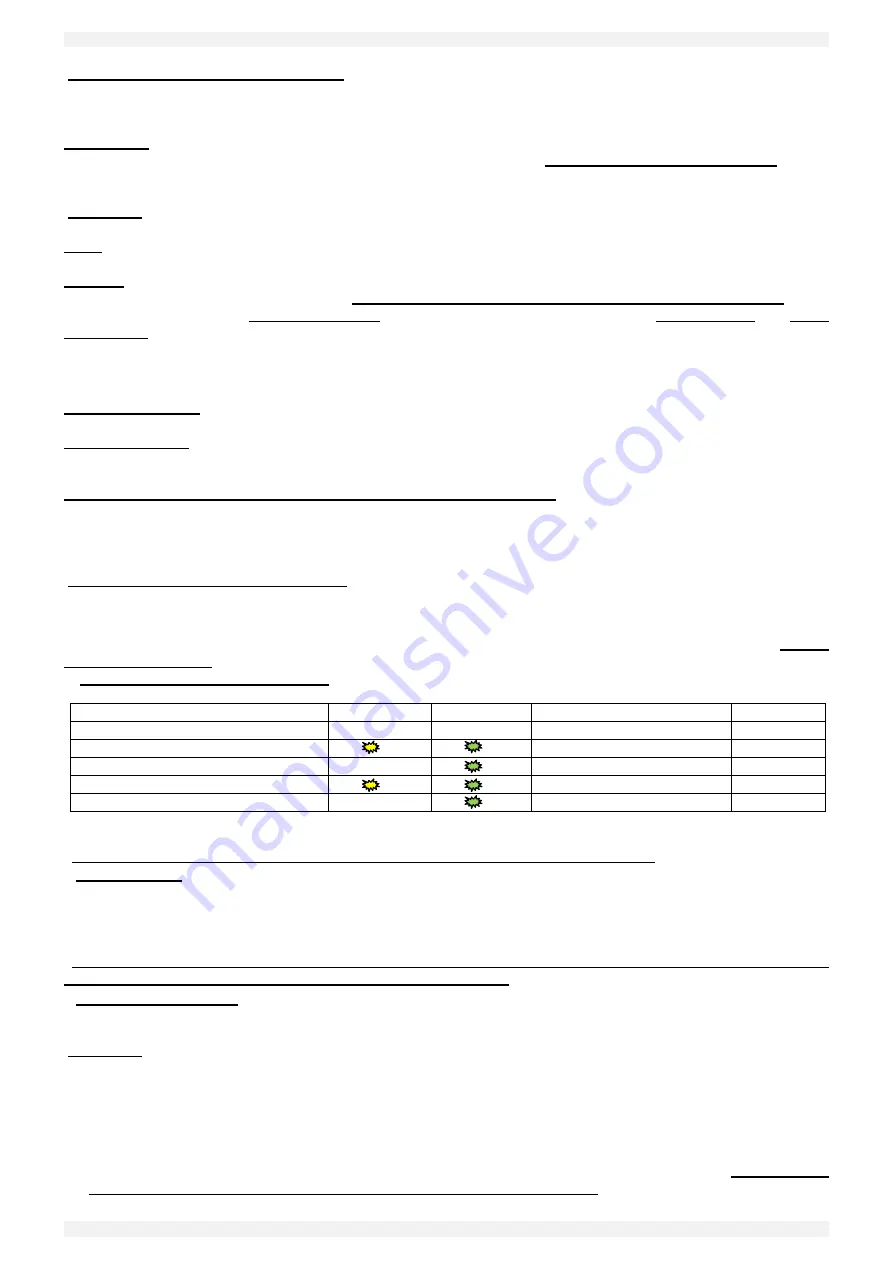
IST-2183.KM01.02/B
Istruzione / User’s Manual / Manuel d’utilisation
Pag. 6 / 11
TECNOCONTROL S.r.l. Via Miglioli 47 SEGRATE ( MI )
Tel: +39 02 26 92 28 90 Fax: +39 02 21 33 734
Compatibility with other Control Units:
In case of a control unit other than Tecnocontrol,
please use products
with 4÷20mA input referred to ground and with compatible operating characteristics (Full Scale, Minimum operating
voltage, Absorption, Maximum load resistance, etc.)
.
We accept no liability for any malfunction, failure or dam-
age caused by products that are not compatible or not of our production.
Average life
: In fresh air and in normal working condition the sensor's life is
about 5 years
from the date of instal-
lation. After this period the yellow LED “
FAULT
” flashes every 4 seconds, is necessary replacing the detector.
After an exposure to gas, above the limits of measurement (50% LFL), the operation of the detector must be
checked with the titled gas, as explained in paragraph "
CALIBRATION CHECK
".
Important:
The catalytic sensor operates only in presence of Oxygen. Do not use pure gases or a lighter
directly on the sensor since they could damage it irremediably.
Note:
the detector is not able to detect gas leaks occurring outside the room where it is installed, neither inside
walls or under the floor.
Warning
: Consider that in polluted environments, or with vapours of flammable substances (including solvents),
the lifetime of the sensor can be reduced. Some substances cause a
permanent reduction of sensitivity
; avoid
contacts of the sensor with
vapours of Silicon
(found in paints, sealants and greases), Tetraethyl lead and Phos-
phate esters. Other substances cause a temporary loss of sensitivity; these "inhibitors" include Halogens, Hydro-
gen sulphide, Chlorine, Chlorinated hydrocarbons (Trichloroethylene or Carbon tetrachloride). After a short time in
fresh air, the sensor resumes its normal operation.
CALIBRATION
IMPORTANT NOTE: the following operations must be performed only by expert and trained personnel, the
mA output changing value, causes the activation of alarm devices connected to the Control Unit.
Periodical testing
: The Calibration with Gas/Air mixture is the only safe method to check the effective operation of
the detector and the correct response of the detector to the gas. It is advisable to perform the verification of opera-
tion every 6-12 months and every 2 years, if necessary, also proceed to recalibration with Gas/Air mixture.
Operation Check, Zero Adjust, Calibration Check and Full Calibration
:
are different code protected functions.
To access these functions, it is necessary to open the housing (
only after setting the plant in safety
) and then insert
the relevant "
Code
" with the F1 and F2 keys. To have the key pressure recognized, hold pressing it for around a
second (
until the Green Led doesn't switch off for a moment
). Then the next key can be pressed. In case of error,
the Yellow LED flashes quickly, just wait about 10 seconds and the sequence is automatically cancelled.
Calibration Kit and Sample Gas Bottles
(
for Calibration Check and Full Calibration
) please, only using a mixture:
20%LFL (0.88%v/v)
Methane in Air (20.9% Oxygen).
Catalytic sensors cannot work in oxygen deficiency
. It is possible to use either the disposable cylinders with
adjust valve or the high pressure ones with reduction gear. It is also necessary to use
the calibration kit
Tecno-
control model TC011
(
for non-corrosive gases
).
“INSTRUMENT OPERATION CHECK” (
Check Code
: F2, F2, F1, F1)
:
this function allows to effect a functional test
of the equipment. After having put the system in safety and inserted the "
Code Test
":
STATUS of
OPERATION CHECK
YELLOW LED GREEN LED mA OUTPUT (S)
Control Unit
After entering the Check Code
OFF
OFF
0 mA
FAULT
Starting Operation Check
ON
ON
0 mA
for 2 seconds
FAULT
Within 2 sec. the mA output
OFF
ON
increases to 4 mA for 5 seconds
NORM
Within 2 sec. the output in mA
ON
ON
increases to
20 mA
for 5 seconds
ALARM
End Check and return to normal operation
OFF
ON
gas measurement
NORM
The check lasts a total time of about 16 seconds, then the detector will return to normal operating conditions.
It is advisable to perform this operation every 6-12 months according to the use.
Note:
The operation cannot be performed if the output is greater than 12mA (10% LFL).
“ZERO ADJUST” (
Zero Code
: F2, F1, F1, F2)
:
even if there is an automatic zero adjustment system (zero tracker)
this operation
must be performed only if the output is different from 4mA
(0% LFL on the control unit) after the
installation and every 6-12 months based on the environmental conditions. This function must be done in clean air
only (
environment without the presence of gas or other pollutants
). Immediately after having inserted the "
Zero Code
", as a con-
firmation of the operation carried out there will be
1
flash of the Green Led and the output will become 4,0mA.
Note:
The operation cannot be performed if the output is greater than 12mA (10% LFL).
In this case, it will be
necessary to recalibrate the unit and/or replacing the detector.
“CALIBRATION CHECK” (
Cal Check Code
: F2, F1, F2, F1)
:
this operation allow to effect a real functional test of
the equipment with gas
after the "
Calibration
" routine, or after the installation. This routine should be done during the
periodic maintenances because this is the only method to verify the instrument real functioning.
WARNING: the Cal Check Code allows using the same cylinder 0.88% v/v M Air for all types even
if they have different gas response,
e.g. the SE183KG. Instead, if a cylinder with 0.28% v/v Air mixture
is used for the verification, the code must not be used.
1)
With the keys perform the “
Cal Check Code
". Wait until the Yellow Led starts to flash (the green one remain fix)
2)
Insert the TC011 over the sensor holder. Adjust the sample gas bottle valve (
0.88%v/v methane in air
), as the flow
meter indicates around 0.3 l/mins (
see Fig.3
).
3)
Verify with a voltmeter connected to the Test-Point, the value reaches a value between
184 and 216mV
, [cor-
responding to
20mA
(±1.6) output and the control unit should be display about
20% LFL
(±2)]. If the value re-
sult is more different, it is necessary to recalibrate the sensor (
see “
Calibration”
).