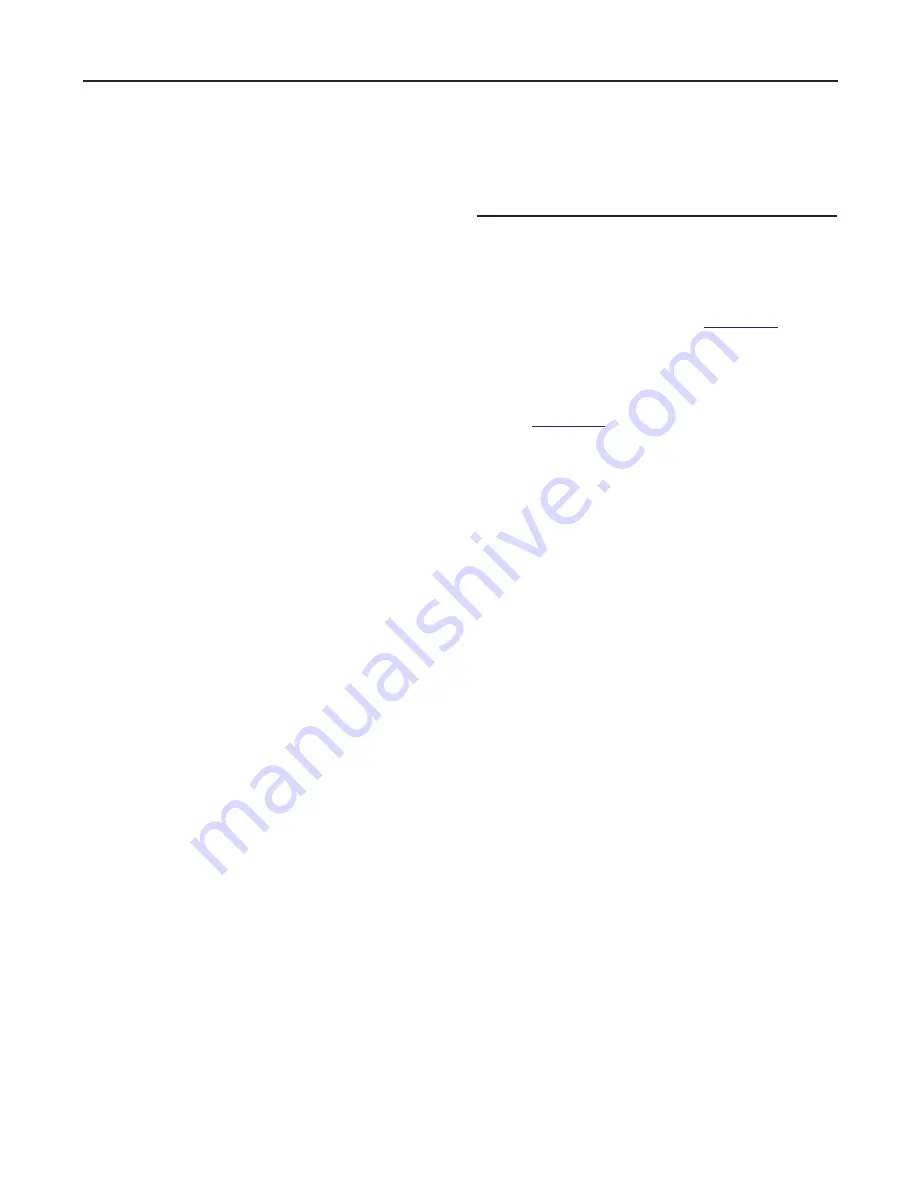
Issue/Rev. 0.7 (9/18) ║ MN06150 • Page 11
Section III – Installation
Table 4. Wiring Checklist
Install Pulse Input Wiring (from Meters and Metered
Injectors)
Install Pulse Outputs Wiring
Install Analog Input Wiring (RTD and 4-20ma)
Install Communications Wiring
Install Digital Input Wiring (DC)
Install Digital Output Wiring (DC)
Install Digital Output Wiring (AC)
Install Earth Ground
Install Instrument Power Wiring
Calculated Accuracy: The gross at standard temperature
Cable entries must be in accordance to EN/IEC 60079-1
section 13 .
For wiring systems utilizing cable glands the gland
and/or thread adaptor must be Ex certified.
The cable end must be securely installed and depending
on the cable type be properly protected from mechanical
damage.
For wiring systems utilizing conduit, an Ex certified seal
-
ing device must be used immediately at the entrance
of the enclosure. Any unused entry must be suitably
blocked with an Ex d IIB IP65 certified plug for ATEX
and IECEx applications. For North American Zone
applications, the plug must be listed 'metal close-up
type.
The maximum ambient temperature for the enclosure
is 60˚ degrees celsuis.
Equipment bonding shall be provided at the external
grounding facility terminal, external connection is not
required when using metallic conduit or armoured
cable. External grounding facility terminal wire range:
10-12 AWG (5.26 sq mm to 3.31 sq mm) wire.
Cover to body fasteners must be either DIN 912 grade
12.9 (alloy steel), DIN 912-A4-70 (316 stainless steel),
or DIN 912-A2-70 (18-8 stainless steel).
Keypad is protected by an intrinsic safe barrier, the
enclosure must be grounded as per national electrical
code regulations, for example NEC/CEC etc.
Battery back-up option (if equipped) use only approved
AAA NiMH (1.2V/Cell Nominal) rechargeable batteries
meeting IEC 61951-2 requirements, IEC IEC Designa-
tion (IEC-HR03) with a maximum capacity of 1.5 Ah at
a 1 h discharge rate.
Warning:
Contains internal battery-powered circuit.
To prevent ignition of hazardous atmospheres, do not open
enclosure unless area is known to be non-hazardous.
To reduce the risk of ignition of hazardous atmospheres,
conduit runs must have a sealing fitting connected
within 18 inches of the enclosure. Substitution of com-
ponents may impair intrinsic safety. To prevent ignition of
hazardous atmospheres and to prevent electrical shock,
disconnect from supply circuits before opening, keep
tightly closed when circuits are in operation.
Start-Up
When the wiring is completed and verified, apply only
instrument power to the unit. The displays should light,
indicating that the microLoad.net is ready for Start-Up.
Next, the microLoad.net must be configured internally
to match the inputs and outputs to which it has been
connected. The Reference Manual
the procedures for the complete configuration of the
microLoad.net. Once configured, check the operation
of the inputs to the microLoad.net. Next, apply external
device power and check the operation of output devices.
The microLoad.net is now ready for use. The Operations
Manual
describes the procedures used in
the day to day use of the instrument.
Summary of Contents for Smith Meter microLoad.net
Page 13: ...Issue Rev 0 7 9 18 MN06150 Page 13 Section IV Diagrams Figure 3 Opening microLoad net ...
Page 29: ...Issue Rev 0 7 9 18 MN06150 Page 29 Section IV Diagrams Figure 16 RS 232 Shared Printing ...
Page 30: ...Page 30 MN06150 Issue Rev 0 7 9 18 Section IV Diagrams Figure 17 RS 485 Shared Printing ...
Page 37: ...Issue Rev 0 7 9 18 MN06150 Page 37 Section IV Diagrams Figure 24 AC Digital Outputs ...
Page 40: ...Page 40 MN06150 Issue Rev 0 7 9 18 Section IV Diagrams Figure 26 Sample Application Worksheet ...
Page 41: ...Issue Rev 0 7 9 18 MN06150 Page 41 Section IV Diagrams Figure 27 Sample Application AC Wiring ...