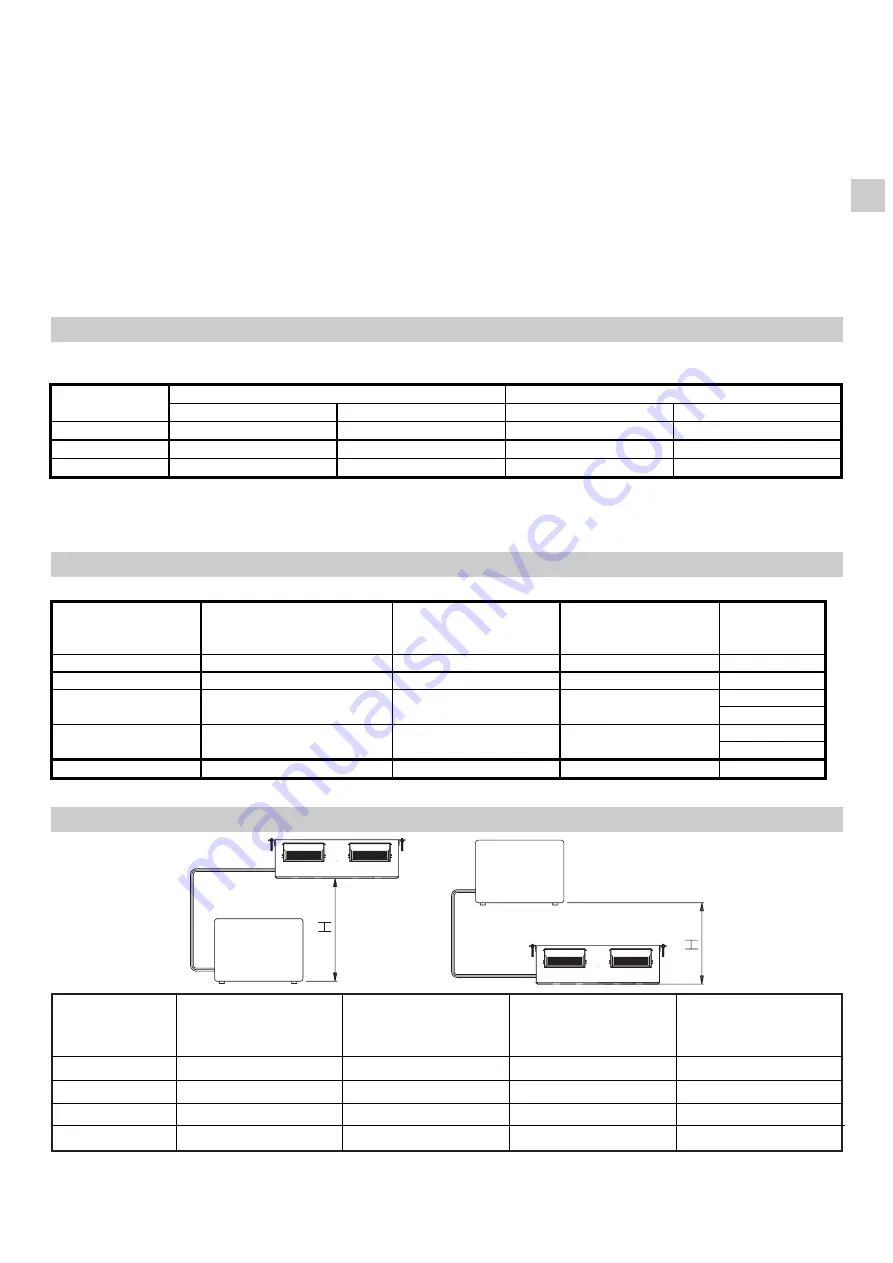
DSAF94
7,5
15
7
10
DSAF124
7,5
15
7
12
DSAF185
10
25
15
20
DSAF225
12,5
20
15
120
3
Installation site selection - Indoor unit
AVOID
• Direct sunlight.
• Nearby heat sources that may affect unit performance.
• Areas where leakage of flammable gas may be expected.
• Locations where large amounts of oil mist may occur (such as in
kitchen or near factory equipment) because oil contamination can
cause operation problems and may deform plastic surfaces and
parts of the unit.
• Unsteady locations that will cause noise or possible water leakage.
• Locations where the remote control unit will be splashed with water
or affected by dampness or humidity.
• To make holes in areas where electrical wiring or conduits are
located.
• To place appliances under tension (household appliances,
computers), because in case of emergency operation the unit could
drip condensate water.
DO
• Select an appropriate position from which every corner of the room
can be uniformily cooled.
• Select a sufficiently strong ceiling to support the weight of the unit.
• Select a location where tubing and drain hose have the shortest run
to the outside.
• Allow access for operation and maintenance as well as unrestricted
air flow around the unit.
Installation site selection - Outdoor unit
AVOID
• Heat sources, exhaust fans.
• Direct sunlight.
• Damp, humid or uneven locations.
• To make holes in areas where electrical wiring or conduits are
located.
DO
• Choose places as cool as possible and well ventilated.
• use lug bolts or equal to bolt down the unit, reducing vibration and
noise.
ADDITIONAL MATERIAL REQUIRED FOR INSTALLATION (NOT SUPPLIED)
●
Deoxidized annealed copper tube for refrigerant tubing connecting the units of the system; it has to be insulated with foamed polyethylene
(min. thickness 8mm).
●
PVC pipe for condensate drain pipe (ø int.18mm) in lenght suitable to let the condensate flow into the outside drainage.
●
Anti-freeze oil for flare connections (about 30g.).
●
Electric wire: use insulated copper wires of size and length as shown in the table “ELECTRICAL DATA” and at paragraph “SYSTEM WIRING
DIAGRAMS”.
ELECTRICAL DATA
LENGTH, SIZE WIRES AND DELAYED FUSE
TUBING LENGTH AND ELEVATION DIFFERENCE LIMITS
(go on page 4)
EG
* For every meter of tube more than standard lenght at shipment, add refrigerant as shown in the table. No additional charge
of compressor oil is necessary.
OUTER DIAMETER
MIN. THICKNESS
OUTER DIAMETER
MIN. THICKNESS
DSAF94-124
6,35 mm
0,8 mm
9,52 mm
0,8 mm
DSAF185
6,35 mm
0,8 mm
12,7 mm
0,8 mm
DSAF225
9,52 mm
0,8 mm
15,88 mm
0,8 mm
LARGE TUBE
MODEL
NARROW TUBE
Power supply wiring length
Power line length
Control line length
Delayed fuse
MODEL
(A-B) m
(C) m
(D) m
GRF94-95
50
15
15
10 A
GRF124-125
35
15
15
10 A
30
20 A
150*
10 A
25
20 A
100*
10 A
Cross section area (mm
2
)
2,5
2,5
1
-
25
20
GRF185
GRF225
25
20
MODEL
MAX. ALLOWABLE
LIMIT OF TUBING
LIMIT OF ELEVATION
REQUIRED AMOUNT OF
TUBING LENGTH AT
LENGTH
DIFFERENCE
ADDITIOONAL
SHIPMENT
H
REFRIGERANT
(m)
(m)
(m)
(g / m)*
* 3-phase version