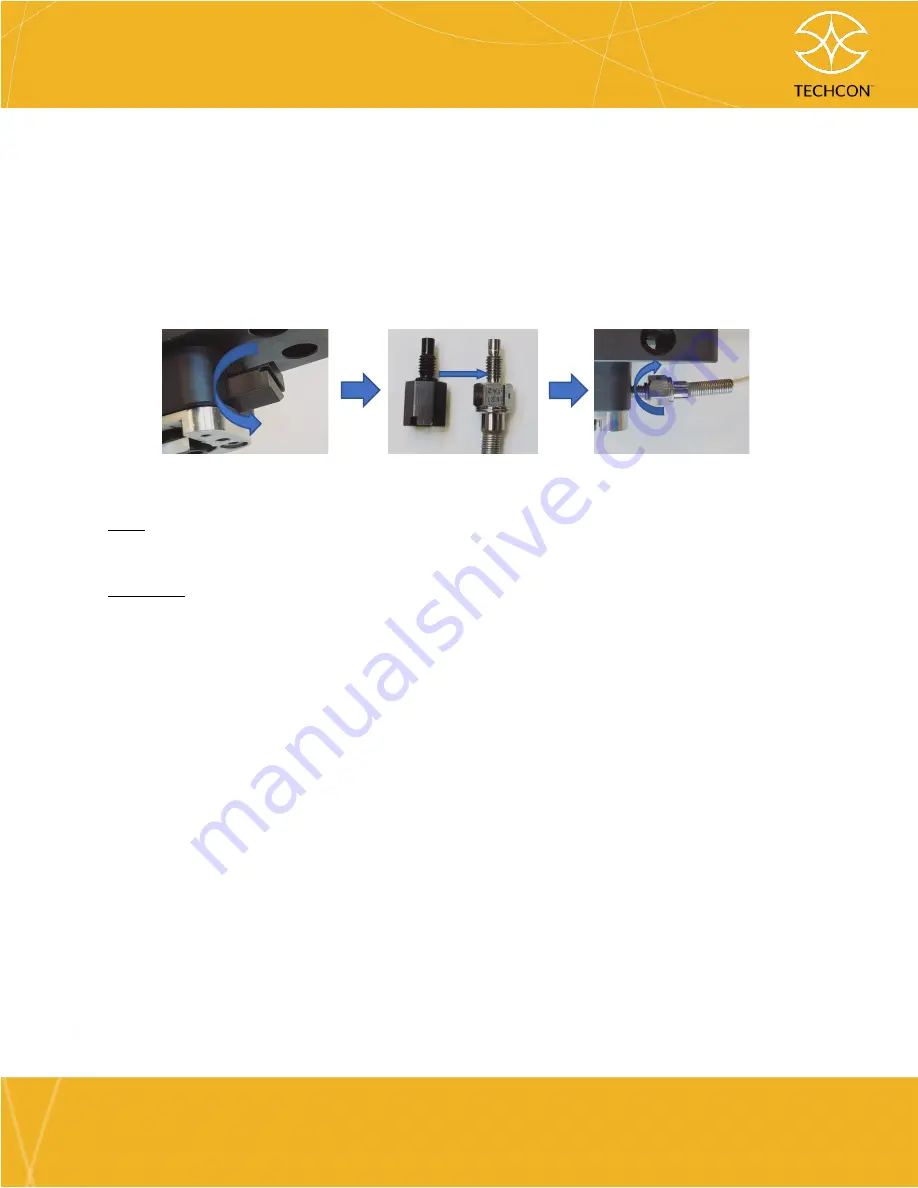
15
TS8200D Series
Micro-Meter Mix User Guide
a.
Remove both fluid manifold plug screws and O-rings.
b.
Mount sensors. Note: If the sensors are missing O-rings, use the O-rings
from the plugs.
c.
Screw the sensors by hand and use 8.0 mm wrench, crescent wrench, or
flat head screwdriver for the final tightening.
Tip:
To avoid cable “curling
,
”
do not install sensors to the controller before fastening
the sensors to the pump.
Warning!
The surface of the sensors is extremely sensitive. Therefore, take extra
caution when handling these sensors and avoid hitting them against other surfaces.
10.
Install Calibration Adaptor
The calibration adaptor is required whenever calibration is performed, when a
new fluid is introduced, when the valve is disassembled & reassembled, or when
the stators or rotors are changed. Connecting calibration adaptor can protect
the TS8200D from having direct contact with the material as it exits the pump.
a.
Mount the 1:1/2:1 K-type Nozzle Locking Plate and use a 2.0mm hex
wrench to fasten screws into place.
b.
Mount the calibration adaptor and use a 2.5mm hex wrench to fasten
screws into place.
c.
Make sure that the calibration adaptor rest evenly against the nozzle
locking plate.