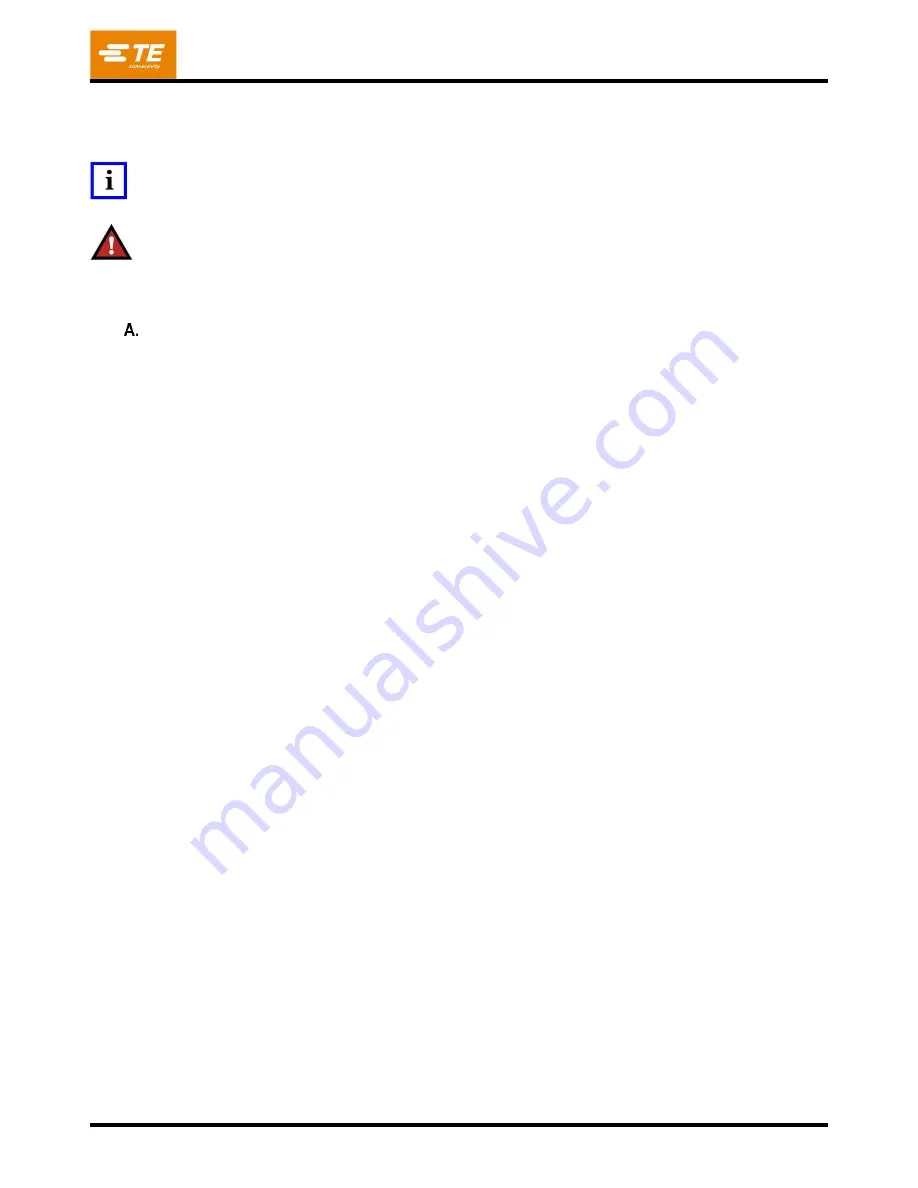
409-32048
Rev A
36
of 64
Changing to Reverse Shuttle mode requires a software configuration change. After software configuration
settings are modified (contact TE Service for specifics) and the AEP application is restarted, the machine
may require a power cycle to complete the conveyor mode change.
NOTE
If desired, the CAPI-6T with Autoload option configured for In-line operation may also be operated as a stand alone press if
Conveyor Extensions are attached on both sides.
DANGER
The press used in Autoload mode must NEVER be operated without required safety guarding in place. The conveyor openings
on each end of the press MUST be covered by an adjacent machine, a block-off plate or a Conveyor Extension.
8.2.
Operation
Loading the PCB
First, initiate production operation by selecting the desired board from Main menu and then double-
clicking on the <Run> button. After responding to all user prompts, press the green Start/Pause button on
the front of the machine, or double-click on the screen <Run> button.
In-line Mode:
If the CAPI-6T is the first machine in a PCB line, place the desired PCB on the upstream
Conveyor Extension, which must be previously installed and aligned to the upstream side of the CAPI-6T.
The Autoload system checks the optic sensor mounted on the Conveyor Extension and stages the PCB
into the machine. If the CAPI-6T is not the first machine in the line, the previous machine is first prompted
to transfer a PCB. In Production mode (left-to-right), the Autoload system will attempt to keep a PCB
staged in the infeed conveyor at all times to maximize throughput. When a PCB is transferred to the main
conveyor, it is moved against the hard stops. The main conveyor then lowers the PCB onto the fixture,
clamps are actuated to secure the PCB in position and the CAPI-6T initiates the press fit operation. When
the PCB processing is completed the main conveyor unclamps the PCB, rises to the transfer height and
moves the PCB downstream in preparation to unload it to the next machine in line. In Reverse Production
mode (right-to-left), the Autoload system will buffer the completed PCB staged on the downstream
(referred to as the infeed) conveyor so that the next PCB may be processed on the main conveyor, thus
maximizing throughput. If the CAPI-6T is the last machine in the line, manually remove the PCB from the
exit Conveyor Extension when prompted.
Reverse Shuttle Mode:
Place the desired PCB on the Conveyor Extension when prompted. The
Conveyor Extension must be previously installed and aligned to the exit side of the CAPI-6T. The cover
for the infeed conveyor opening must also be previously installed. The infeed conveyor is not used in this
mode and must be closed off for safety.
Once the PCB is placed on the Conveyor Extension, acknowledge the prompt by clicking the screen
message or pressing the green Start/Pause button. The conveyor then transfers the PCB into the CAPI-
6T past the hard stops; the hard stops are engaged and the PCB is moved back against the hard stops.
The conveyor then lowers the PCB onto the fixture; the clamps are actuated to hold the PCB down and
the CAPI-6T initiates the press fit operation. When the PCB processing is completed the conveyor
unclamps the PCB, rises to transfer height and moves the PCB back out to the end of the Conveyor
Extension to be manually removed. Remove the PCB from the exit Conveyor Extension when prompted.
8.3.
Testing the Autoload Function
Enter the Input/Output screen and select the 'Autoload' tab. The
Load Board
button, when pressed, performs a
PCB load operation. When configured for In-line Production mode, the upstream machine is prompted to
transfer a PCB to the infeed conveyor unless a PCB is already present on the infeed conveyor. The PCB is
then transferred to the main conveyor where it is moved against the hard stops. The main conveyor retracts the
hard stops, lowers and then clamps the PCB against the fixture. When configured for Reverse Shuttle or Inline
Reverse Production mode the main conveyor transfers the PCB backwards (into the machine) from the output
Conveyor Extension past the hard stops, extends the hard stops, moves the PCB forward against the hard
stops, lowers and then clamps the PCB against the fixture. The unload function can be initiated by pressing the
Unload Board
button to release the PCB, raise the main conveyor and deliver the PCB to the end of the main
conveyor / Conveyor Extension or in In-line Reverse Production mode, to the downstream (referred to as the
“infeed”) conveyor.
The Autoload system then waits for a prompt from the downstream machine to send a PCB
before transferring the PCB, or for the operator to remove the PCB from the Conveyor Extension.