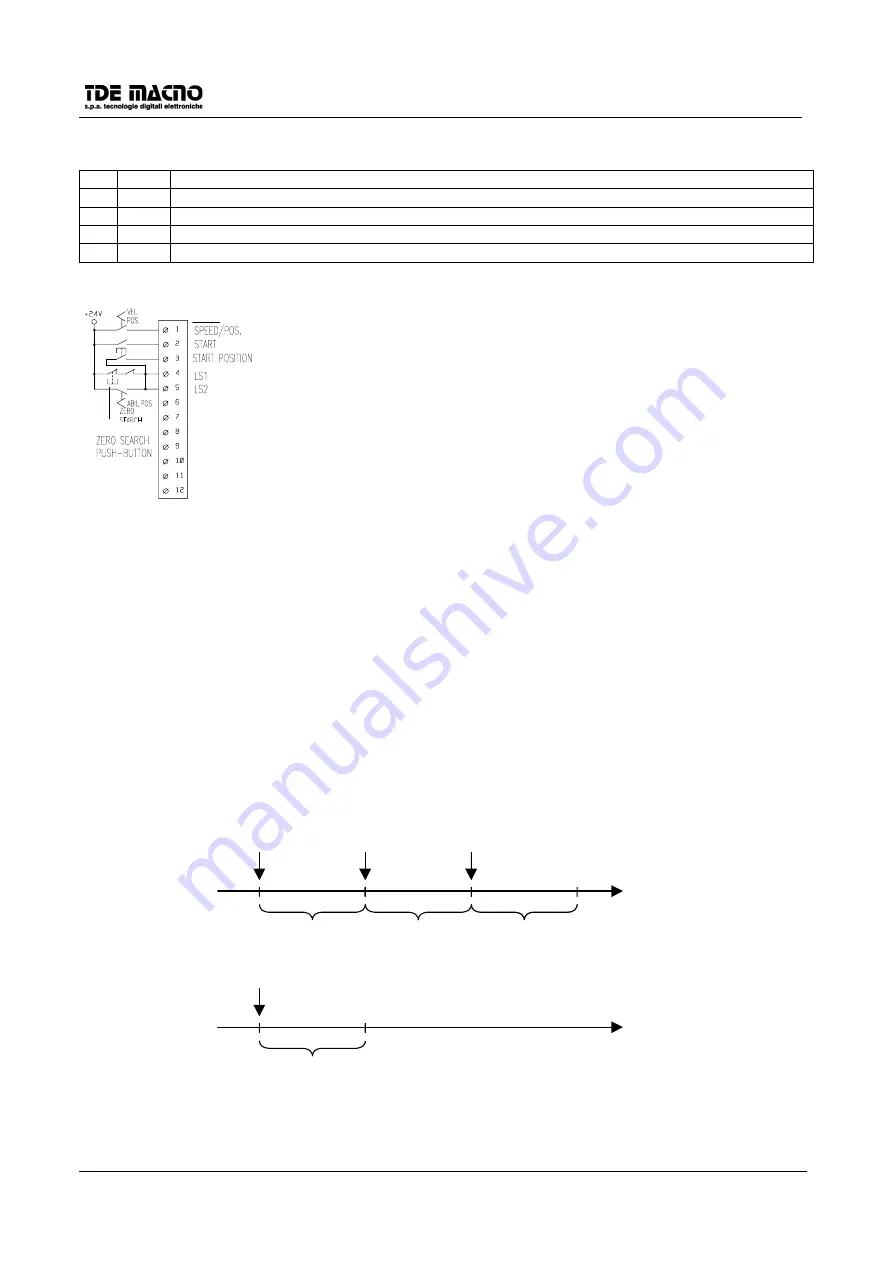
User manual
13-6
DSC/DSCT Series
13.3.3. SPEED, POSITION WITH INITIAL ABSOLUTE NUMBER
c1
= 11
position/speed
c2
= 0
on line
c3
= 9
start pos. 1
c4
= 5
limit switch LS1 (absolute microswitch)
c5
= 6
limit switch LS2 (absolute microswitch)
As the limit switch needed to initialise the system blocks the motor movement in the search direction, if the
movement must be free the “
search zero/enable positioning
” selector switch is needed, which excludes the
limit switch when it is in the second condition while it enables the start position push-button.
13.4. POSITIONER
IMPROVEMENTS
The positioning speed can be taken from the external analog reference (SREF, /SREF) by setting P01=0 or
P02=0 (depends on the used movements). This speed reference is read at the start of the movement, and
variations during the movement do not cause any effect.
In the old versions the positioner could make only cumulative movements: each movement is referred to the
previous. Now the positions of the movements can be also expressed in reference to a zero position: by
setting
c39=0
the "cumulative rate" positioning mode is chosen, by setting
c39=1
the "absolute position"
positioning mode is chosen.
rate P07
rate P07
Start
Start
position P07
Start
0
Start
Etc..
absolute position:
Cumulative rate:
J1