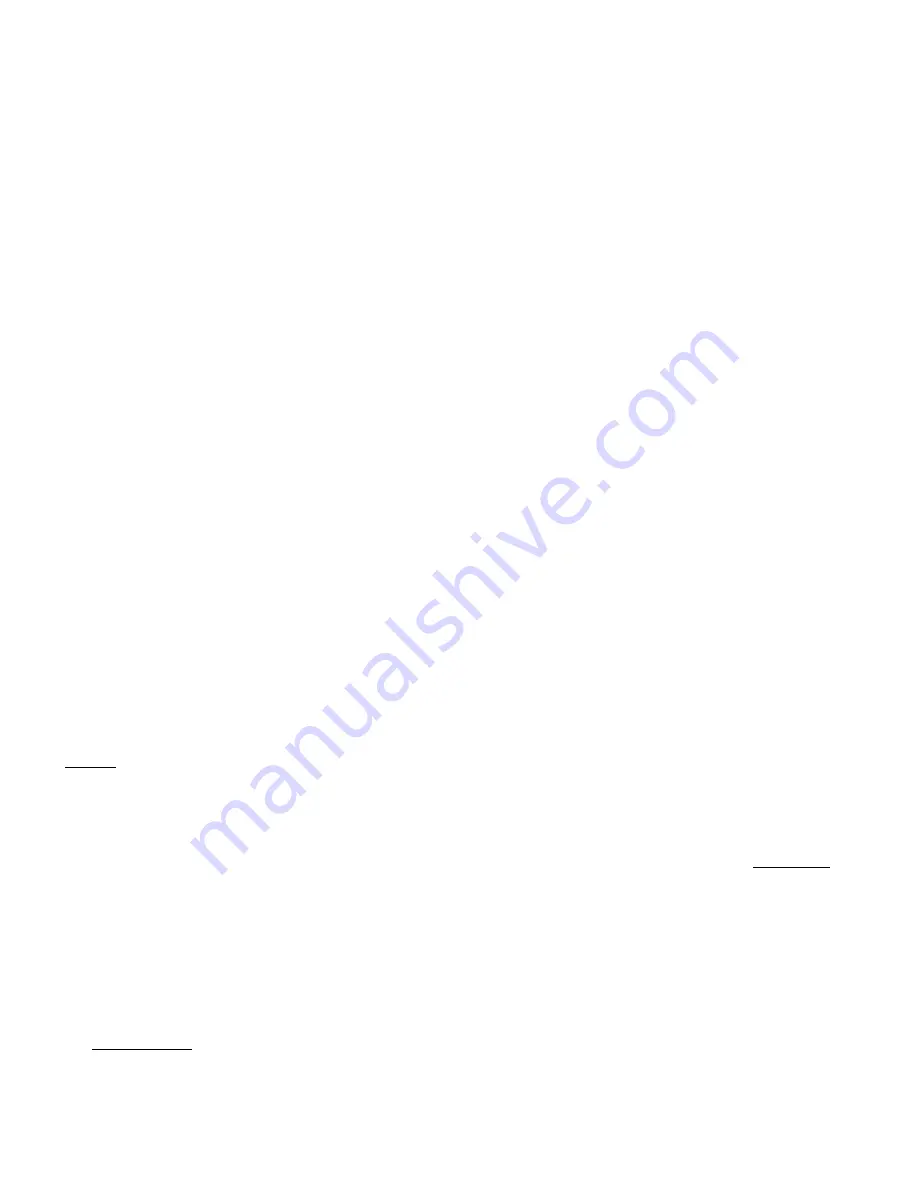
Page 8
the Working Thermostat dial setting
. The setting should be reduced to 150°C the same for Alcohol, and
you must adjust the Fractional Thermostat temperature down to 85° C when recovering Alcohol.
9.
The first container under the solvent outlet nozzle will collect the purest alcohol. Your second
container, under solvent outlet nozzle will collect the recovered alcohol.
10. After a recovery cycle has been completed, let the unit cool to at least 50°C prior to opening the secured
top. Premature opening will allow a release of solvent fumes into the surrounding atmosphere and can
also cause burn injury to the operator.
11. Open the cover, remove expandable ring and disposable bag. Dispose of the waste in the bag according
to appropriate state and local guidelines. NOTE: Take special care not to spill any remaining waste
material (especially wax) into the vapor collecting duct.
12. Be sure that the distilling chamber remains free of liquid and debris, after each cycle.
Approximately 45-90 minutes are necessary before the distillate begins to flow. Be certain that there is
sufficient ventilation to prevent dangerous gases and vapors from forming. During the first few distillation
cycles there may be a small amount of thermal oil leakage. This is quite normal and is to be expected. Do
not tilt or shake the unit once loaded or when operating. This could create a dangerous situation.
Xylene:
1.
Place clean and dry collection containers under each of the lower distillate solvent outlet nozzles left and
right.
2.
Verify that the Thermal oil level is at the correct level.
3.
Place the disposable plastic bag into the vessel using the expandable metal ring to hold the bag in place.
Note: For the 3-gal unit, small hole should be cut near the top edge of the bag to fit over the vapor
collection duct.
4.
Place the contaminated solvent in the distilling chamber, up to 3 gallons.
NOTE
:
Take special care NOT to allow any contaminated solvent to enter the Vapor Collector Duct
Manifold when you are filling the distilling chamber. This may create a build up of wax inside of the
condensing coils that can cause blockage and unwanted pressure within the distilling chamber during
recovery.
5.
Close the cover of the chamber by securing the locking knob by tighten clockwise until the knob stops.
The spring will act as a release valve if an unlikely blockage of the vapor collector duct occurs.
6.
Set the distillation temperature with the Working Thermostat 15°C above the boiling point of the
contaminated solvent to be recovered.
7.
Setting of the fractional temperature depends on the solvent you are recycling. You should then set the
fractional temperature at approximately 20-30°C higher than your highest boiling point of the
contaminates.
Alcohol has a boiling point of 78°.
Your fractional temperature switch will be set at a
minimum of 85°C for the recovery of alcohol.
Summary of Contents for SR12
Page 3: ...Page 3 GLOSSARY 15...