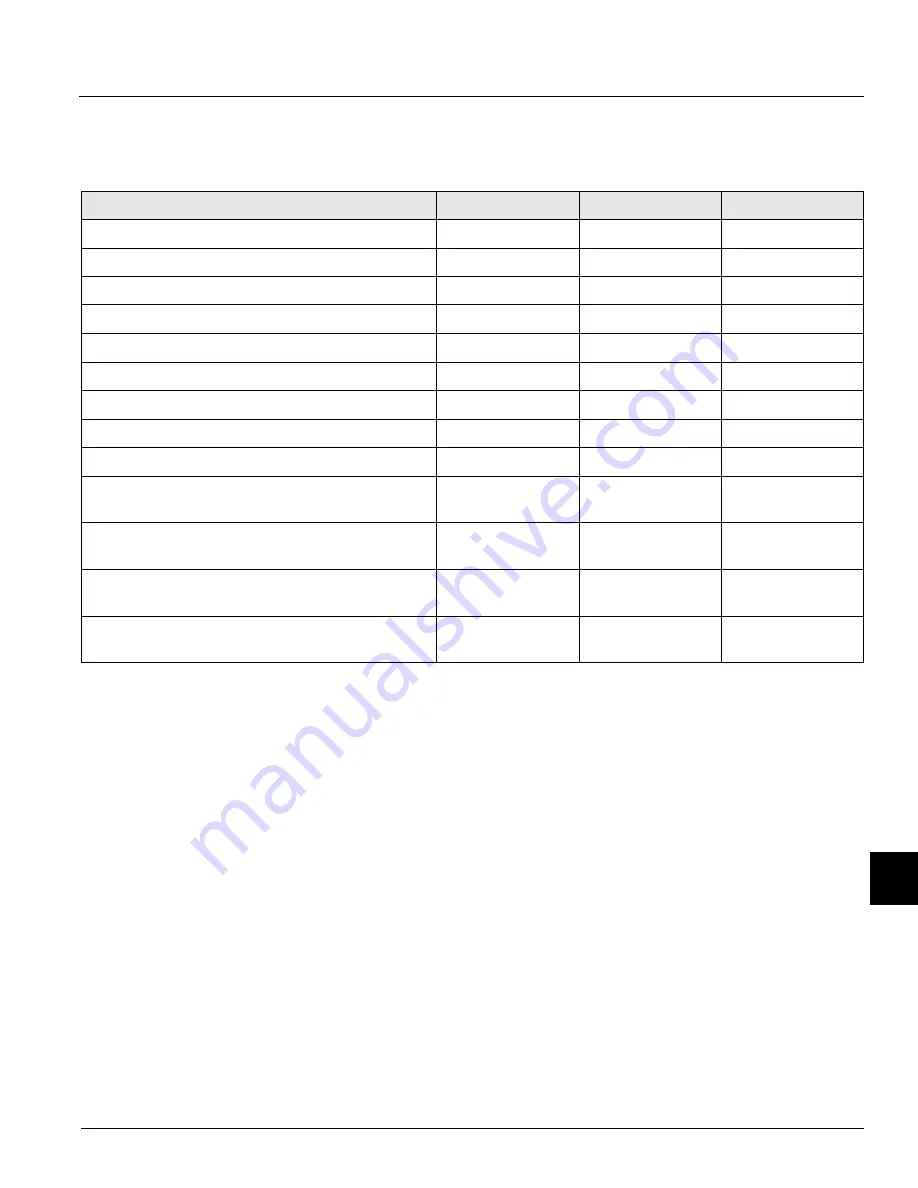
Section 9
9-1
Model 336, 338, 339
Parts Replacement Schedule
9
Parts Replacement Schedule
Maintenance Intervals
Table 9-1
Part Description
Every 3 Months
Every 6 Months
Annually
Drive Shaft Seal
X
Scraper Blade
X
Freezer Door Gasket
X
Front Bearing
X
Draw Valve O-ring
X
Pivot Pin O-ring
X
Prime Plug O-ring
X
Air Tube O-ring
X
Air Orifice O-ring
X
White Bristle Brush, 3” x 7”
Inspect and replace if
necessary.
Minimum
White Bristle Brush, 1” x 2”
Inspect and replace if
necessary.
Minimum
Black Bristle Brush, 1” x 2”
Inspect and replace if
necessary.
Minimum
Double-Ended Brush
Inspect and replace if
necessary.
Minimum
Summary of Contents for Freezemaster 336
Page 8: ...1 4 TO THE INSTALLER Model 336 338 339 To the Installer 1 Notes...
Page 18: ...4 6 OPERATOR PARTS IDENTIFICATION Model 336 338 339 Operator Parts Identification 4 Notes...
Page 22: ...5 4 USER INTERFACE Model 336 338 339 User Interface 5 Notes...
Page 38: ...9 2 PARTS REPLACEMENT SCHEDULE Model 336 338 339 Parts Replacement Schedule 9 Notes...
Page 42: ...10 4 LIMITED WARRANTY ON EQUIPMENT Model 336 338 339 Limited Warranty on Equipment 10 Notes...
Page 46: ...11 4 LIMITED WARRANTY ON PARTS Model 336 338 339 Limited Warranty on Parts 11 Notes...