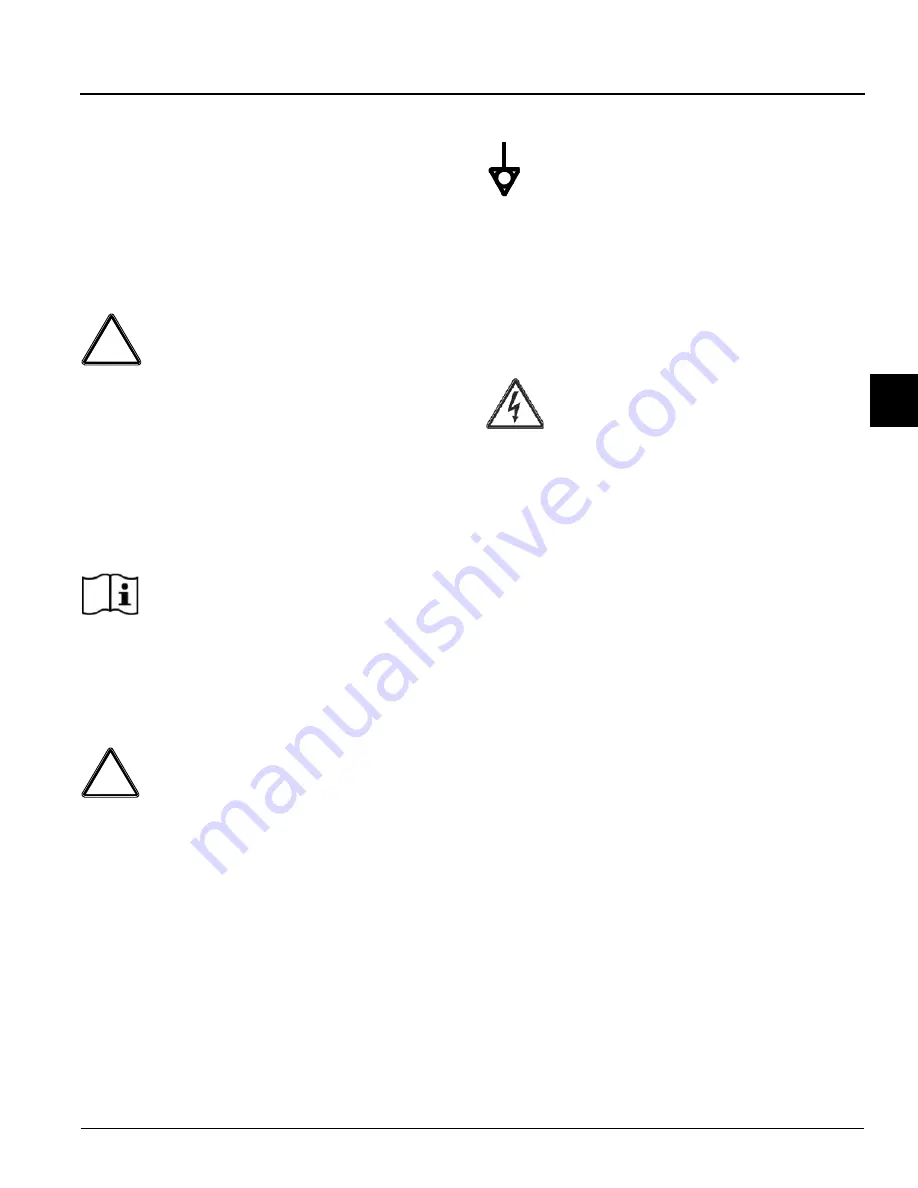
Section 3
3-1
Model 390
Safety
3
Safety
We, at the Taylor Company are concerned about the
safety of the operator when he or she comes into contact
with the freezer and its parts. Taylor has gone to extreme
efforts to design and manufacture built-in safety features
to protect both you and the service technician. As an
example, warning labels have been attached to the
freezer to further point out safety precautions to the
operator.
!
DANGER!
Failure to adhere to the following
safety precautions may result in severe personal injury or
death. Failure to comply with these warnings may also
damage the machine and/or its components. Such
damage may require component replacement and
service repair expenses
.
To Operate Safely
NOTICE! DO NOT
operate the machine
without reading this entire manual first. Failure to follow
all of these operating instructions may result in damage
to the machine, poor performance, health hazards, or
personal injury.
!
IMPORTANT! This machine is to be used only
by trained personnel. It is not intended for use by children
or people with reduced physical, sensory, or mental
capabilities, or lack of experience and knowledge. Where
limited machine operation is allowed for public use, such
as a self-serve application, supervision or instruction
concerning the use of the machine by a person
responsible for their safety is required. Children should
be supervised to ensure that they do not play with the
machine.
IMPORTANT! An equipotential grounding lug is
provided with this machine. Some countries require the
grounding lug be properly attached to the rear of the
frame by the authorized installer. The installation location
is marked by the equipotential bonding symbol (5021 of
IEC 60417-1) on both the removable panel and the
machine's frame.
WARNING!
Avoid injury.
•
DO NOT
operate the machine unless it is
properly grounded.
•
DO NOT
operate the machine with larger fuses
than specified on the machine's data label.
•
All repairs should be performed by an
authorized Taylor service technician.
•
The main power supplies to the machine must
be disconnected prior to performing installation,
repairs, or maintenance.
•
Machines that are permanently connected to
fixed wiring and for which leakage currents may
exceed 10 mA, particularly when disconnected
or not used for long periods, or during initial
installation, shall have protective devices to
protect against the leakage of current, such as a
GFI, installed by the authorized personnel to the
local codes.
•
Stationary machines which are not equipped
with a power cord and a plug or another device
to disconnect the appliance from the power
source must have an all-pole disconnecting
device with a contact gap of at least 0.125 in. (3
mm) installed in the external installation.
•
Supply cords used with this machine shall be
oil-resistant, sheathed flexible cable not lighter
than ordinary polychloroprene or other
equivalent synthetic elastomer-sheathed cord
(code designation 60245 IEC 57) installed with
the proper cord anchorage to relieve conductors
Summary of Contents for 390
Page 8: ...1 4 TO THE INSTALLER Model 390 To the Installer 1 Notes...
Page 10: ...2 2 TO THE OPERATOR Model 390 To the Operator 2 Notes...
Page 14: ...3 4 SAFETY Model 390 Safety 3 Notes...
Page 18: ...5 2 USER INTERFACE Model 390 User Interface 5 Notes...
Page 30: ...9 2 PARTS REPLACEMENT SCHEDULE Model 390 Parts Replacement Schedule 9 Notes...
Page 36: ...11 4 LIMITED WARRANTY ON PARTS Models 390 Limited Warranty on Parts 11...