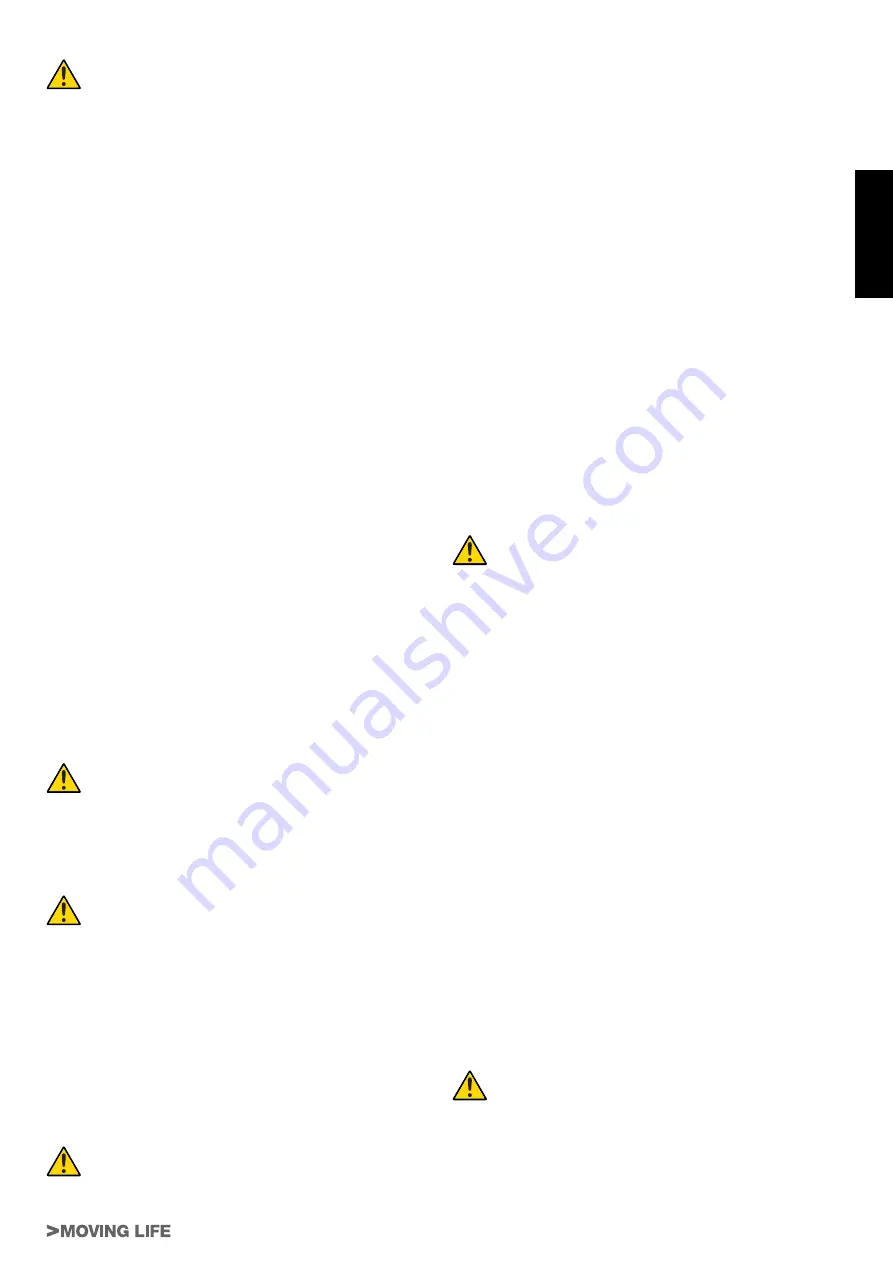
13
T-ONE Series
ENGLISH
4_
ELECTRICAL CONNECTIONS
Before proceeding, ensure that the gearmotor is not
connected to the electrical mains.
• To make the connections, remove the cover from the gearmo
-
tor, route the power cables through the holes on the founda
-
tion plate assembly (if used) and through the lower body of the
gearmotor, then prepare them for connection to the terminal
board of the control card housed in the electrical components
support.
• Use cables with a minimum section of 2.5 mm² for the power
circuits (T-ONE3B and T-ONE5B) and 1.5 mm² (T-ONE5, T-
ONE8 and T-ONEXL), 0.5 mm² for the control circuits.
For connections to the control cards consult the relative instruction
booklets:
-
K120M for T-ONE3B;
-
K125M for T-ONE5B;
-
K580M for T-ONE5, T-ONE8 and T-ONEXL.
5_
12V BATTERY INSTALLATION (T-ONE5B)
If a battery is to be fitted on the gearmotor to guarantee operation
in the event of a power failure, remove the cover and insert it in the
relative seat (fig. 13); then connect the power cables to the tabs.
6_
MANUAL RELEASE
In the event of a power failure, raise the cover from the lock, insert
the relative key and turn as shown in fig. 14.
Then, as shown in fig. 15, pull the lever outwards to enable manual
movement of the gate.
7_
LIMIT SWITCH (T-ONE5 / T-ONE8 / T-ONEXL)
The series T-ONE (230 Vac) has been designed to operate with an
electro-mechanical micro-switch type limiter.
The cables are connected as shown in fig. 16:
1= grey (common);
2= orange (F.C. close - NC contact);
3= red (F.C. Open - NC contact);
4= grey (common).
As shown in fig. 16, when the gear rotates clockwise and the spring
moves as shown, if gate travel does not stop, invert the position of
the red and orange wires on the terminal board of the control card.
8_
FINAL CHECKS AND START-UP
T-ONE must be connected to the power mains by
skilled and qualified personnel, in possession of all
requirements for full compliance with all legal provi-
sions, standards and regulations.
Immediately after powering up T-ONE, perform a number of simple
checks:
1. Ensure that the leds on the control card are lit.
2. Ensure that the motor does not activate any gate movement
and that the flashing light is off.
If this is not so, disconnect the control unit from the
power supply immediately and check the electrical
connections carefully.
Other useful information for troubleshooting can be found in chap
-
ter 7.6 “Troubleshooting”.
For other parameter settings, such as gate travel learning, clutch
adjustment, deceleration, automatic closure time, obstacle detec-
tion sensitivity etc., refer to the instructions of the electronic cards.
9_ TESTING AND COMMISSIONING
This is the most important phase of automation set-up to ensure
maximum system safety. The test can also be performed as a pe
-
riodic check of automation devices.
Testing of the entire system must be performed by
skilled and qualified personnel, who are responsible
for the tests required to verify the solutions adopted
according to the risks present, and for ensuring ob-
servance of all legal provisions, standards and regula-
tions, with particular reference to all requirements of
the standard EN12445 which establishes the test meth-
ods for testing automations for power-operated gates.
9.1_ Testing
Each automation component, such as sensitive edges, photocells,
emergency stop, etc., requires a specific testing phase; for these
devices take care to follow the procedures specified in the respec
-
tive instruction manual.
To test T-ONE, perform the following sequence of operations:
Ensure that all specifications in this manual, and in particular chap
-
ter “1 WARNINGS” have been strictly observed;
2. Using the control or stop devices envisaged (key-operated
selector switch, control pushbuttons, radio transmitters, etc.)
perform gate opening and closing tests, ensuring that the leaf
movement corresponds to specifications.
3. Check operation of all system safety devices one at a time
(photocells, sensitive edges, emergency stop etc.);
4. To test photocells and in particular that there is no interference
with other devices, pass a cylinder (diameter 5 cm, length 30
cm) through the optic axis joining the pair of photocells, first
close to the TX and then the RX and then mid-way between
the two. Ensure that in all cases the device engages, chang
-
ing from the active status to alarm status and vice versa. Also
check that the envisaged action is generated in the control unit,
for example: that during the Closing manoeuvre, the door in
-
verts the current movement.
5. If hazardous situations generated by the moving leafs are pro
-
tected by means of impact force limitation, measure the force
as specified in the standard EN 12445. If the settings “speed”
and “gearmotor force” control are used as an auxiliary function
with the system for reduction of impact force, test and identify
the setting that obtains the best results.
9.2_ Commissioning
Commissioning can only be performed after positive
results of all test phases on T-ONE and other devices
present. Partial or “makeshift” commissioning is strict-
ly prohibited.
• Prepare the automation technical documentation (to be con
-
served for at least 10 years), which must contain the follow
-
ing documents: an overall layout diagram of the automation,
electrical wiring diagram, risk assessment and relative solu
-
tions adopted, manufacturer’s declaration of conformity for all
devices used (for T-ONE use the CE declaration of conformity
enclosed) copy of instruction manual for operation and the au
-
tomation maintenance schedule.
• Affix a dataplate on the gate, specifying at least the following
data: type of automation, name and address of manufacturer
(responsible for commissioning), serial number, year of con
-
struction and CE mark.
• Permanently fix a label or plate in the vicinity of the gate, stat
-
ing the procedures for release and manual manoeuvres.
• Compile the automation declaration of conformity and deliver
to the owner.
• Compile the manual “Instructions and warnings for automation
operation” and deliver to the owner.
• Prepare the automation maintenance schedule (including all
instructions for the maintenance of individual devices) and de
-
liver to the owner.
• Before commissioning the automation, ensure that the owner is
adequately informed in writing of all associated risks and haz
-
ards (for example of the manual of instructions and warnings
for automation operation).
10_ OPERATION
The gearmotors in the series T-ONE have been designed to move
horizontal sliding gates with leafs of a maximum weight of 300 kg
(
T-ONE3B
), 500 kg (
T-ONE5B
and
T-ONE5
), 800 kg (
T-ONE8
)
and 1200 Kg (
T-ONEXL
).
Use of the device for other purposes or in other circum-
stances than as specified is strictly prohibited.
The electronic control unit installed enables selection of the operat
-
ing mode:
automatic
: a control pulse activates gate opening and closing;
semiautomatic
: a control pulse activates gate opening or closing;
In the event of a power failure, the gate can still operate thanks
to the option of manual control, possible by means of the
manual
release device
.
Summary of Contents for T-ONE
Page 28: ...24 T ONE Series fig 4 1 fig 5A fig 5B fig 5 ...
Page 29: ...25 T ONE Series fig 6 1 1 1 fig 7A fig 7 fig 7B ...
Page 30: ...26 T ONE Series fig 9 1 1 1 1 fig 8 2 1 1 2 ...
Page 31: ...27 T ONE Series fig 10 fig 11 fig 13 fig 12 ...
Page 32: ...28 T ONE Series fig 16 fig 15 fig 14 1 2 3 4 ...