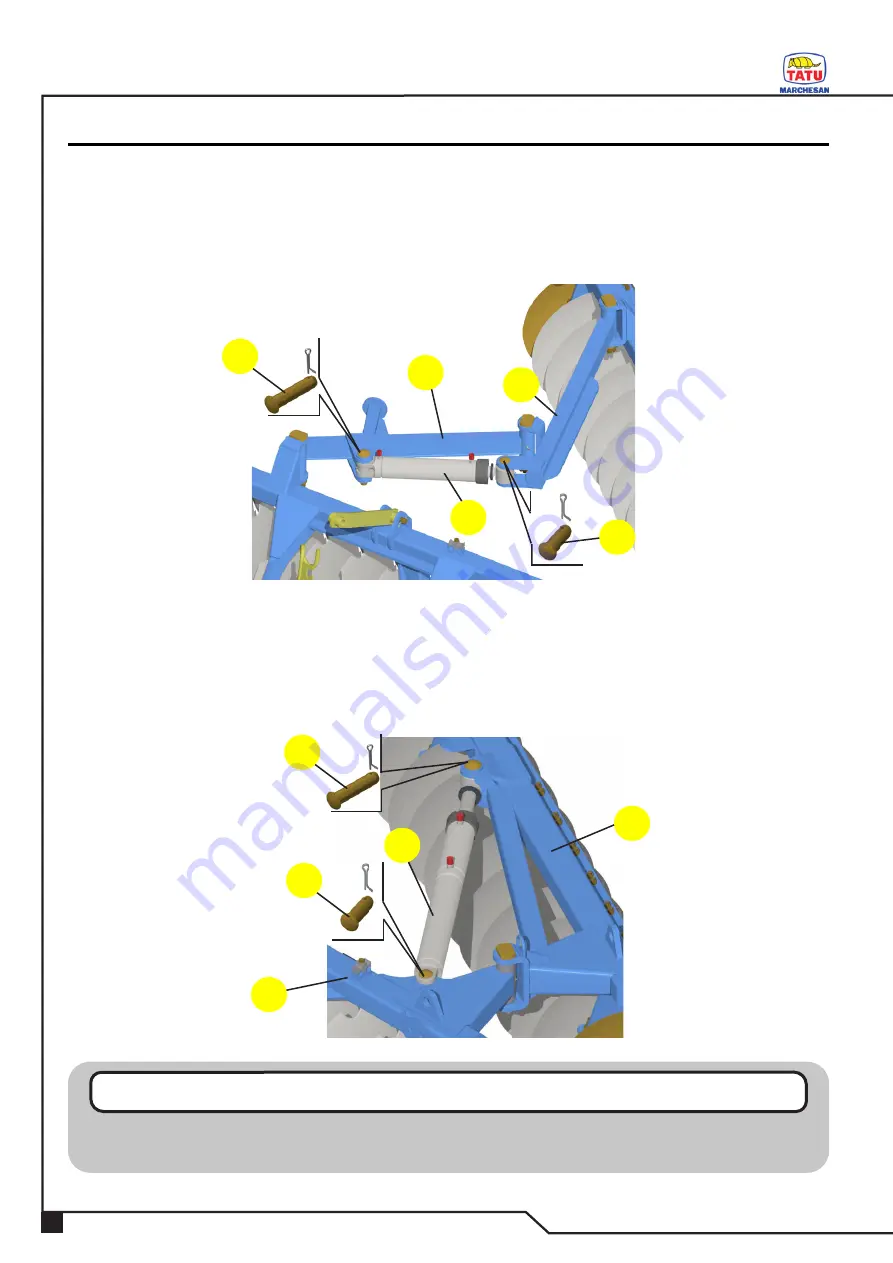
32
GNL - Rev. 07 - Mar/22
5. Assembly
Hydraulic cylinder assembly
For the GNL model with 32 disc blades and hydraulic cylinder:
1. Fasten the cylinder barrel (A) to the front stabilizer bar (B) using an articulation pin
(H) and cotter pin.
2. Fasten the cylinder rod to the rear stabilizer bar (C) using a junction axle (G) and
cotter pin.
For the GNL model with 36 - 42 disc blades and hydraulic cylinder:
1. Fasten the cylinder barrel (D) to the front frame (E) using a junction axle (G) and
cotter pin.
2. Fasten the cylinder barrel to the rear frame (F) using an articulation pin (H) and
cotter pin.
NOTE
- When assembling the cylinder, the rod must be facing the rear part of the equipment
to be on its correct position and the cylinder ports must be facing up.
A
A
C
C
B
B
G
G
H
H
D
D
F
F
E
E
G
G
H
H