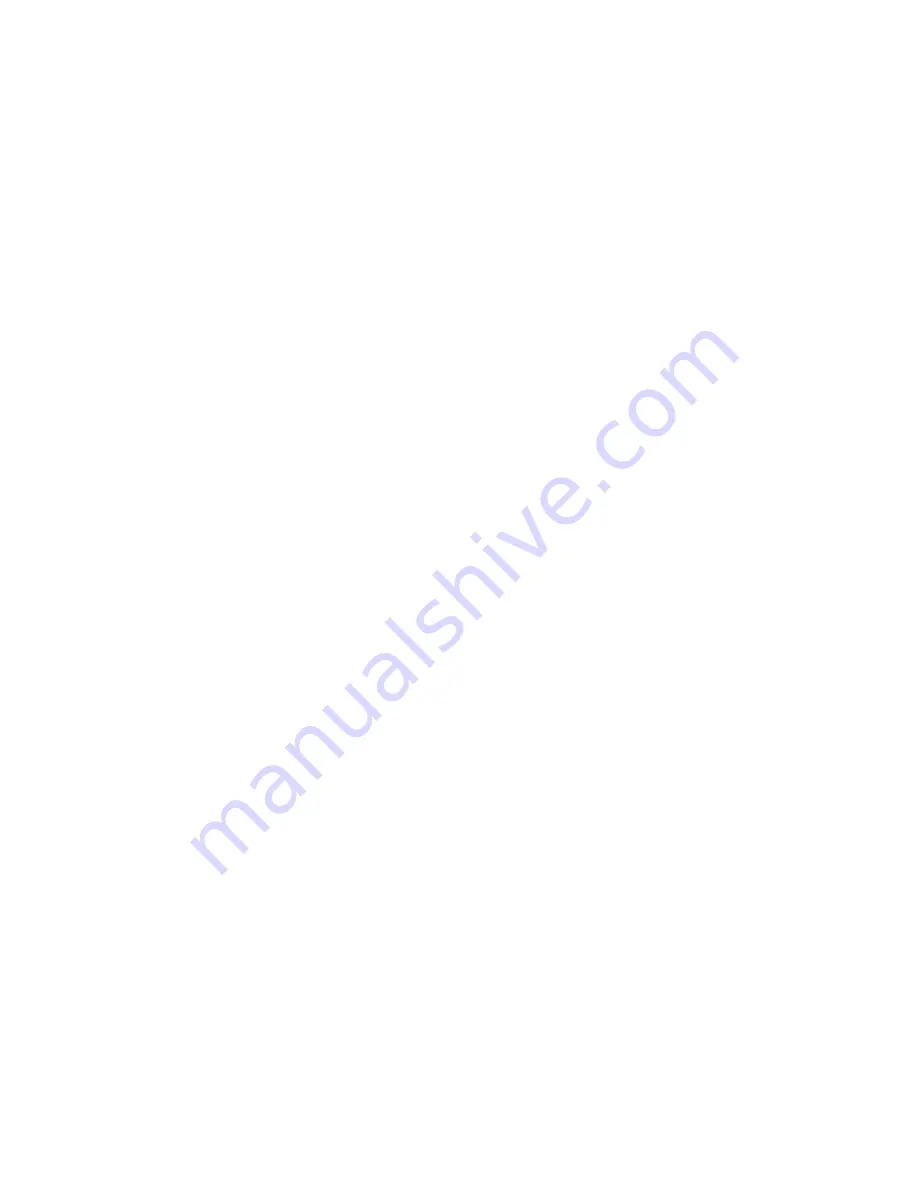
©Copyright Task Force Tips, LLC 2002 - 2018
LIA-200 March 20, 2018 Rev19
22
9.2 CRANKSHAFT OVERRIDE AND REPLACEMENT
The crankshaft includes an intentional shear joint to protect the gear train from overload, costly repairs and loss of service. The
magnitude of torque required to shear the crankshaft is several times greater than the torque typically needed to operate the valve at
maximum operating pressure. If the crankshaft breaks during use, this is an indication that either there is something obstructing the
half ball internally or the crank shaft has been abused (e.g. used as a step for climbing).
9.2.1 CRANKSHAFT OVERRIDE
In an emergency, the opposite side of the crankshaft can be turned using a 1/2” wrench or hex socket. This allows the valve to be
open or closed until the crankshaft is replaced. To prevent loss of the 1/8” square key on the crankshaft, do not allow the crankshaft
to slideout of gearbox until a replacement crankshaft is acquired. It is important not to rely on this as a long-term method of operation.
9.2.2 DIAGNOSIS
To diagnose the problem that caused the crankshaft to fail, complete the following steps:
1. Close upstream water supply. If possible, relieve pressure leading up to valve.
2. Locate 1/2” hex where crankshaft protrudes from opposite side of gearbox.
3. Gently turn crank shaft away from travel stop using a ½” hex wrench. Do not attempt to shock crankshaft free and do not exceed
50 ft-lb (68 Nm) of torque.
4. If crankshaft will not rotate, then half ball is likely obstructed. Only after relieving pressure on flanged joint, unbolt valve. Clear any
obstructions and evaluate whether repair is needed before returning to service.
5. If crankshaft is able to rotate, cycle the valve several times from open to closed to determine whether the crankshaft binds at any
place between the travel stops. If crankshaft binds, consult Task Force Tips Service Department to determine the appropriate
repairs.
6. If crankshaft rotates freely after clearing any obstructions, then a replacement crank shaft may be ordered from Task Force Tips
and replaced as described below.
9.2.3 CRANKSHAFT REPLACEMENT
A broken crankshaft can be replaced at any time by completing the following steps, regardless of whether or not the upstream water
supply is pressurized. Referring to item numbers shown in section 6.6, follow the steps below:
1. Remove external retaining ring (item 1) adjacent to ½” hex on crankshaft. Do not over-expand the retaining ring.
2. Using a punch or Phillips head screwdriver at least 6” in length, gently push on dimple in ½” hex end of crankshaft (item 18).
Continue to push crankshaft through until it protrudes from opposite side of gearbox.
3. Grab broken end of crankshaft and pull out of gearbox. As crankshaft is withdrawn, grasp small key (item 19) on shaft so it does
not get lost.
4. If 1/8” square x 1” long key is not visible in shaft, it has likely fallen into gearbox bore and must be removed before installing new
crankshaft. If square key is visible in gearbox bore, slide it out of bore. Needle-nose pliers may be helpful depending on position
of key in bore.
5. Verify polymer bushings (item 2 and 20) are still seated in bores on each side of gearbox. If not, locate and replace bushings.
6. Look through gearbox bore and note approximate orientation of square keyway in worm (item 10). Verify round notch in thrust
washer (item 3) is aligned with square keyway in worm.
7. Prepare new crankshaft by applying small dab of grease to keyway and seating 1/8” square x 1” long key into keyway. Grease ill
keep key in place during assembly.
8. Slide shaft into gearbox with key orientation the same as keyway in worm. Rotate shaft slightly in alternating directions until key
finds keyway, then push shaft in until it stops. Retaining ring groove and ½” hex should be protruding through opposite side of
gearbox. If hex is not visible, it may be necessary to slide polymer bushing back into gearbox bore.
9. Install retaining ring (item 1) onto shaft. Do not over-expand the retaining ring.
10.0 REPAIR
Factory service is available with repair time seldom exceeding one day in our facility. Factory serviced appliances are repaired by
experienced technicians to original specifications, fully tested and promptly returned. Repair charges for non-warranty items are
minimal. Any returns should include a note as to the nature of the problem and whom to reach in case of questions.
Repair parts and service procedures are available for those wishing to perform their own repairs. Task Force Tips assumes no liability
for damage to equipment or injury to personnel that is a result of user service. Contact the factory or visit the web site at tft.com for
parts lists, exploded views, test procedures and troubleshooting guides.
11.0 ANSWERS TO YOUR QUESTIONS
We appreciate the opportunity of serving you and making your job easier. If you have any problems or questions, our toll-free
“Hydraulics Hotline”, 800-348-2686, is normally available to you 24 hours a day, 7 days a week.