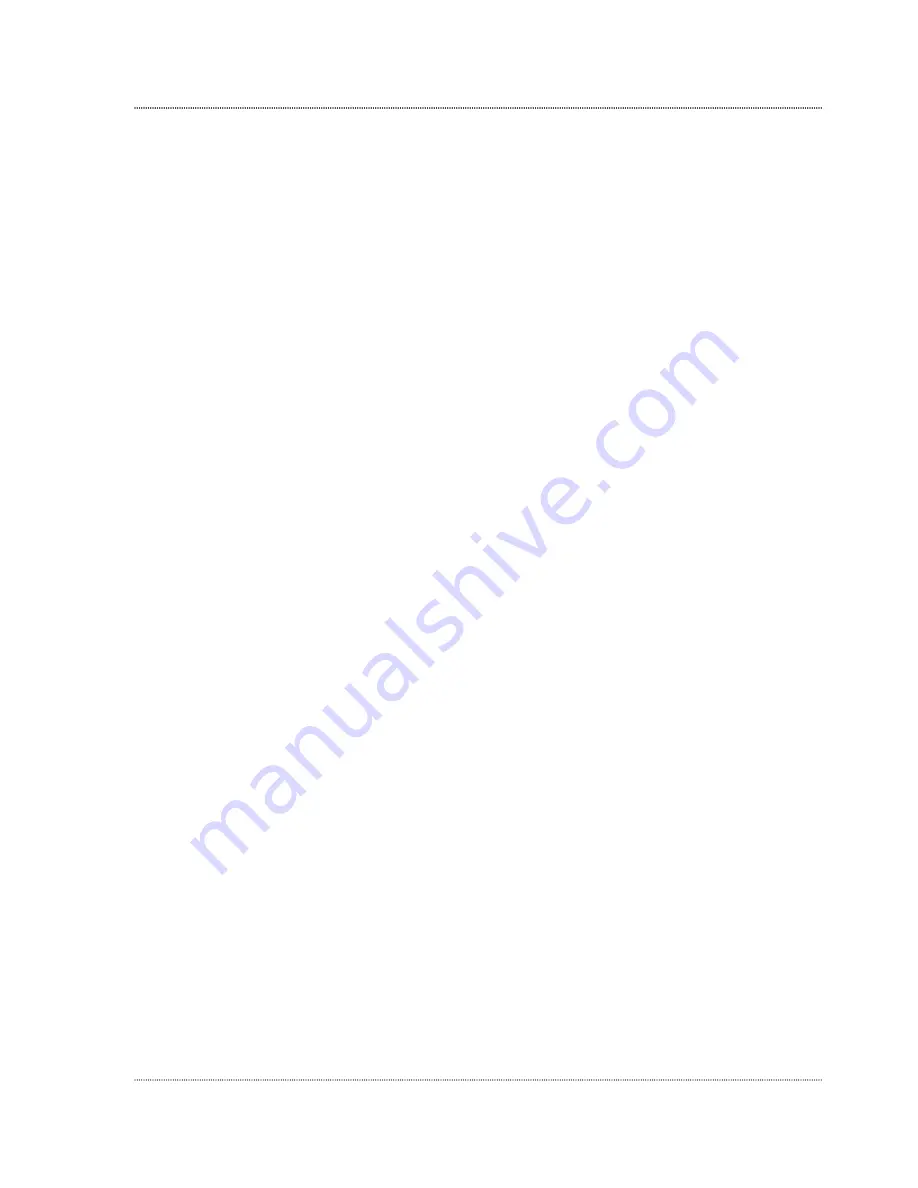
Solo Innova Instructions 1-800-782-9927 Version 01-18
Tarm Biomass · 4 Britton Lane · Lyme, NH 03768
The induced
draft fan
(9) pulls combustion air into the boiler via the primary and secondary air con-
trols and pulls gases from combustion through the heat exchanger and exhausts them out of the boiler.
The
boiler serial number plate
(10)
indicates factory no. and type and other information required to
order spare parts. Factory no, and type can be noted in Section 8 On the last page of this user guide.
The
flue gas turbulators
(11) provide for turbulent flow of the flue gas in the heat exchanger, increas-
ing heat transfer.
The heat
exchanger pipes
(12) transfers the heat from the combustion gasses to the boiler water.
The
firebox
(13) is the primary combustion chamber where the wood is loaded and the fire is started.
Secondary combustion air is injected in the nozzle just above the
gasification tunnel
(14) that serves
to hold combustion gasses in a high temperature, turbulent environment to achieve high efficiency
combustion.
The highly efficient wood combustion in the Solo Innova boiler is achieved by the draft fan continu-
ously operating once wood in the boiler is ignited to achieve an efficient and clean burn of all the
wood loaded in the firebox. Due to the continuous heat output once the Solo Innova is ignited the
boiler must be connected to a thermal storage system.
2.2.2 Description of Burn Process
A key component of the Solo Innova boiler operation is the induced
draft combustion fan
. Both pri-
mary and secondary combustion air are both drawn into the boiler by the induction blower mounted on
the breach of the boiler. Primary and secondary combustion air are metered through air ducts into the
boiler with the precise volume necessary for proper combustion. The combustion air is drawn through
self
closing flaps
into individually adjustable
primary and secondary air valves
. Primary air then is
drawn into the firebox where it is dispersed behind the
firebox aprons
into
the
primary combustion
chamber
just above the top of the
ceramic refractory combustion stones
. Secondary air is drawn
downward and then back into the center combustion stone where it enters the
combustion throat
.
Here secondary air is turbulently mixed at high velocity with hot combustion gasses, which ignite and
are burned very completely before being exposed to the heat exchange surfaces between the combus-
tion chamber and the breach. The correct proportions of air for combustion from the fan and gases
from the wood are a
prerequisite for optimal and environmentally friendly burning of the wood with
the
highest possible efficiency.
A noteworthy construction feature is the special
ceramic fuel tunnel
(15) in the heart of the boiler
which ensures that the combustion temperature reaches more than 1800 °F (1000 °C). Combustion is
efficient, soot-free, and ensures optimal fuel use. The secondary combustion stones are essential to
achieving complete combustion with log wood. The stones allow the combination of exhaust gasses
and secondary air to reach very high temperatures while isolated from the quenching affect of the wa-
ter jacket.
Product Description and Requirements for Safe Operation > Boiler Function
Page 5