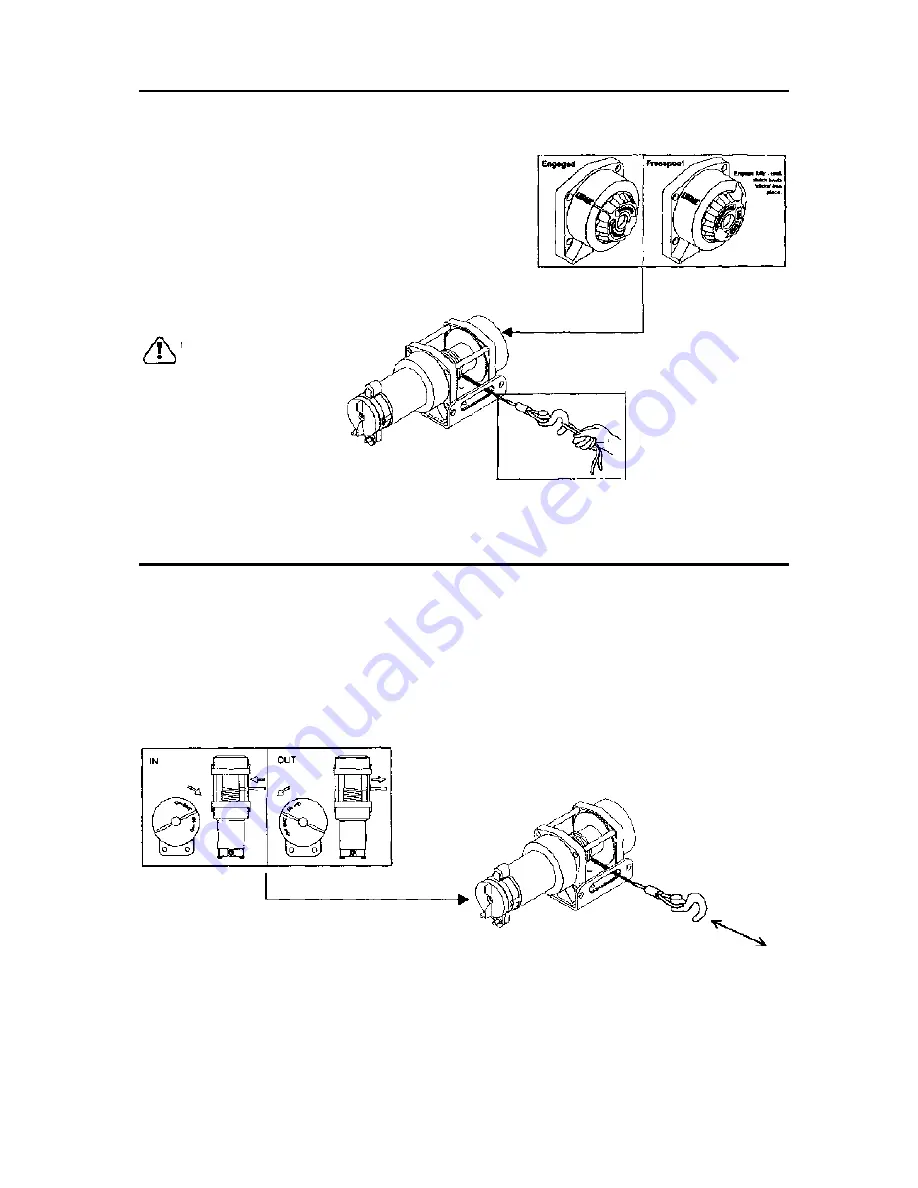
14.1
Pulling out wire rope – manual
The clutch knob, located on the winch housing
Clutch for free spool
opposite the motor, controls the clutch position.
When the clutch is in free spool, the gear train and
wire rope drum are uncoupled, allowing the drum
to rotate freely for pulling out the wire.
To prevent damage, always fully engage or fully
disengage the clutch knob.
WARNING
Do not disengage clutch if
winch is under load or
wire rope is in tension.
14.2
In and out spooling – automatic
The spooling switch is located on the winch motor.
When clutch above is engaged, the gear train is coupled to the wire rope drum, and power may
be transferred from the winch motor.
When turning the spooling switch to the right or left the motor activates for automatic in- as well
as out spooling.
Operating problems:
Remember that the winch is operated by the 12-v battery system. Long
and heavy usage can empty the battery faster than the charger is loading
the battery.
More information on battery and battery charger see page 9 and 20.
Summary of Contents for FS 1218 EX
Page 2: ...DRAFT 2 ...