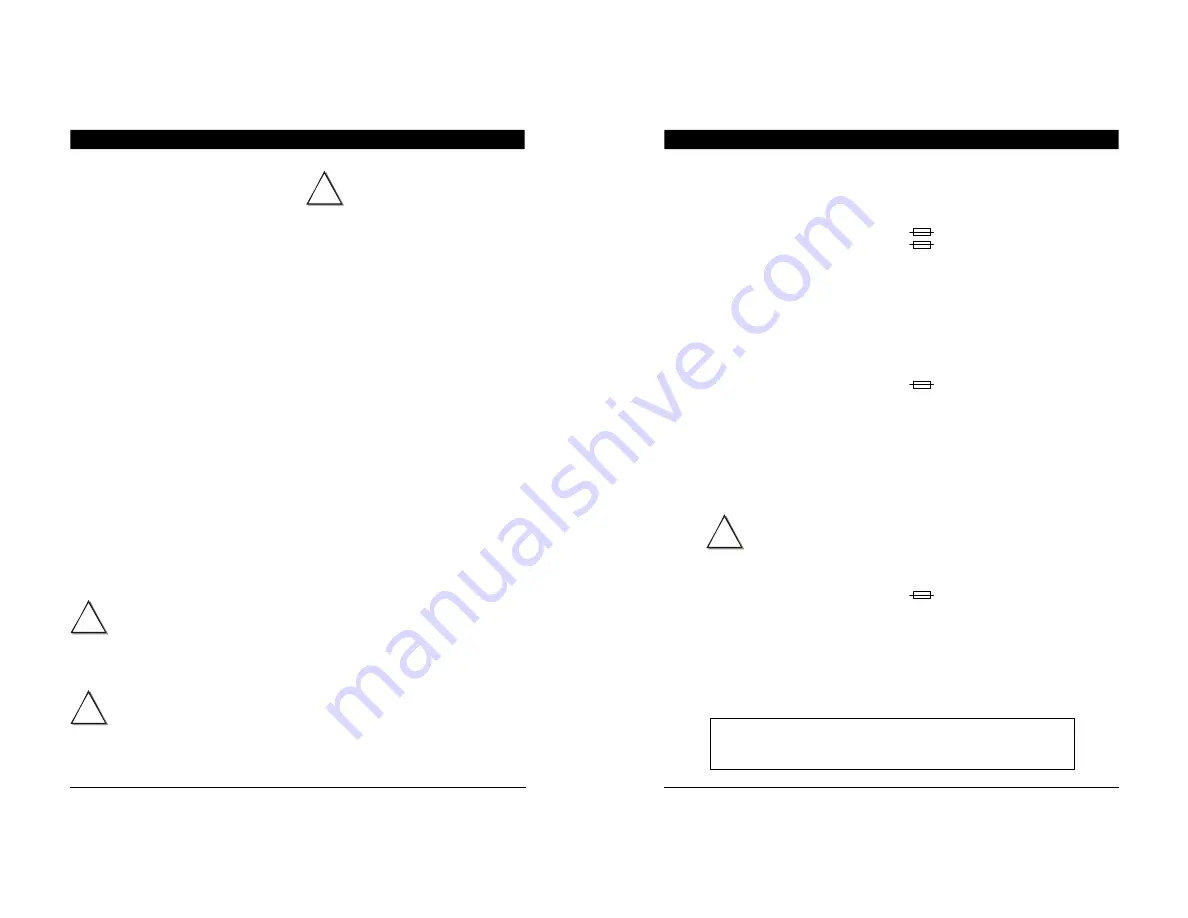
12
TARGET ECO I FEEDING, rev.09
TARGET ECO I FEEDING
3.
MOUNTING INSTRUCTIONS
3.1
Installing the Controller on
the Wall
Open the latch and lift the cover. Remove
the black caps located on each of the four
mounting holes. Mount the enclosure on
the wall using four screws. Be sure the
electrical knockouts are at the bottom of
the enclosure in order to prevent water
from entering the controller. Insert the
screws in the mounting holes and tighten.
Fasten the four black caps provided with
the controller onto the four mounting holes.
The enclosure must be mounted in a loca-
tion that will allow the cover to be com-
pletely opened right up against the wall.
3.2
Connections
3.2.1
Controller’s Main Wiring
Refer to the wiring diagram enclosed with
this user's manual to connect the control-
ler. Use the electrical knockouts provided
at the bottom of the enclosure. Do not
make additional holes in the enclosure, par-
ticularly on the side of the enclosure when
using a computer communication module.
!
All wiring must be done by an autho-
rized electrician and must comply with
applicable codes, laws and regulations.
Be sure power is off before doing any
wiring to avoid electrical shocks and
equipment damage.
!
Do not install rigid conduit into electrical
knockouts. Only nylon cable glands are
permitted for cable or wire fastening.
!
The controller has no power-on switch.
An external switch or circuit breaker
shall be included in the building installa-
tion to interrupt power to L and N
electric power lines. It shall be in close
proximity to the equipment and within
easy reach of the operator. It shall be
marked as the disconnecting device for
the equipment.
3.2.2
Alarm Connection
There are two types of alarms on the mar-
ket. One type activates when current is
cut off at its input, whereas the other ac-
tivates when current is supplied at its in-
put. For an alarm of the first type, use the
NC terminal as shown on the wiring dia-
gram. For an alarm of the second type,
use the NO terminal.
33
TARGET ECO I FEEDING, rev.09
TARGET ECO I FEEDING
9.
TECHNICAL SPECIFICATIONS
Type .................................................
ECO I FEEDING
Main supply fuse F1 ..............................
1A, fast-blow
Module power fuse F2 ............................
1A, fast-blow
Main supply/frequency ........................... 115/230V+10% -20%, 20VA, 50/60Hz
Housing ............................................. IP54, plastic casing
Operating temperature ........................... 0 to 40°C
Storage temperature ............................. -15 to 50°C
Ambient relative humidity ....................... max. 95%
Pollution degree ................................... 2
Altitude ............................................. Up to 2000m
Installation Category: ............................. Class II
Type .................................................
CDM-1
Main supply fuse F1 ..............................
1A, fast-blow
Main supply/frequency ........................... 230V+10% -20%, 2HP, 50/60Hz
Housing ............................................. IP54, plastic casing
Operating temperature ........................... 0 to 40°C
Storage temperature ............................. -15 to 50°C
Ambient relative humidity ....................... max. 95%
Chain disk motor .................................. 230Vac / 2HP max
Nema Code Letter: ............................. A to L
Full-load amps (FLA): ........................... 13A max
Locked rotor amps (LRA): ..................... 170A max
!
Running a motor with higher ratings could result in potential controller
damages and/or fire. If the Nema Code Letter is not available,
exclusively use the LRA ratings!
Type .................................................
PSM-8
Main supply fuse F1 ..............................
1A, fast-blow
Main supply/frequency ........................... 115/230V+10% -20%, 12VA, 50/60Hz
Housing ............................................. IP54, plastic casing
Operating temperature ........................... 0 to 40°C
Storage temperature ............................. -15 to 50°C
Ambient relative humidity ....................... max. 95%
Sensor supply ...................................... 12VDC, 200mA total max.
The room temperature where the controller is located must always remain
between 32° and 104°F (0° and 40°C).
For indoor use only.