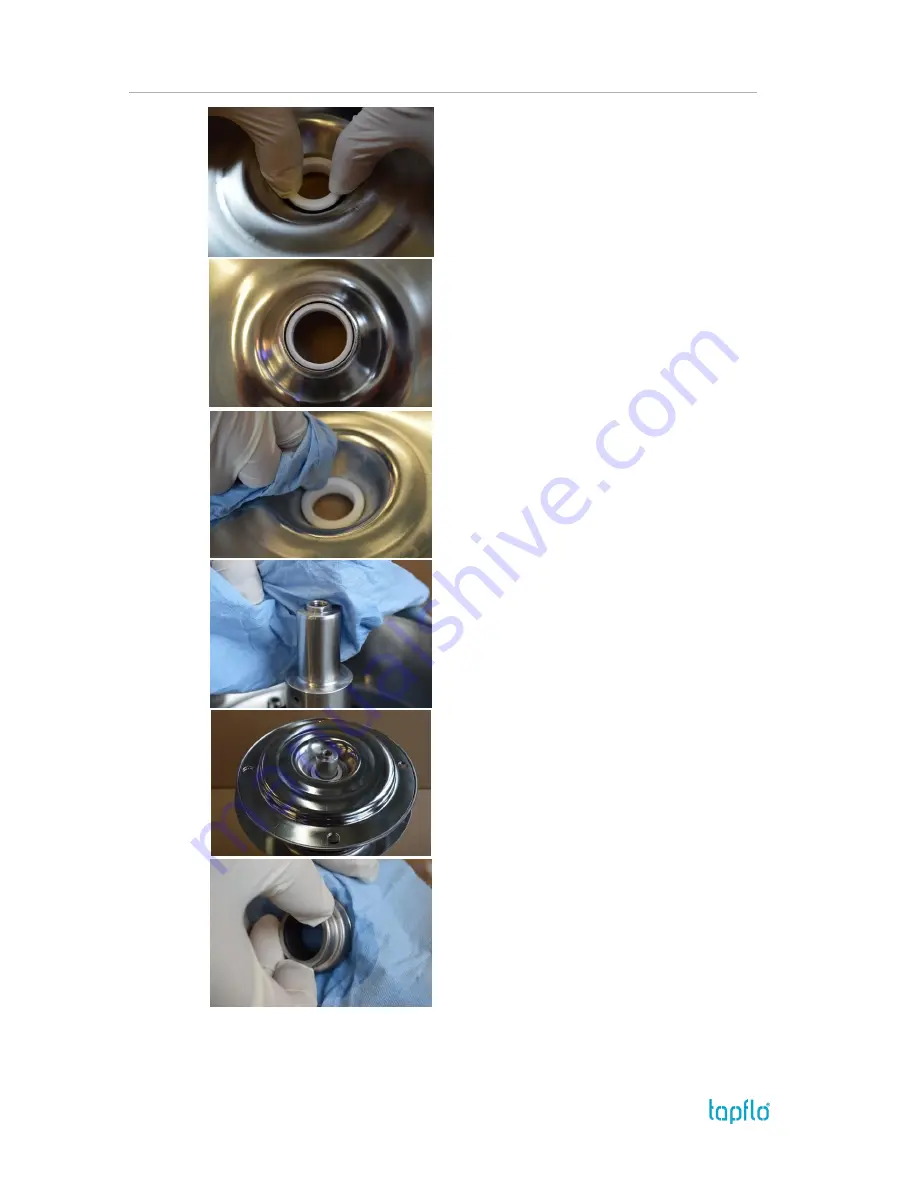
3.
MAINTENANCE
IOM manual CTI & CTH centrifugal pumps
21
Fig. 3.4.7
Simultaneously with both hands push the static part
[15B] of mechanical seal until the end.
Fig. 3.4.8
Ensure that the static par of mechanical seal is evenly
spaced around the circumference.
NOTE! Check if O-ring does not springs back. It may
springs back when O-ring does not reach the surface
of the internal rim.
Fig. 3.4.9
Once again degrease surface of the recess and the
sliding face
of the static part of mechanical seal.
Fig. 3.4.10
Clean and degrease the shaft extension [16].
Fig. 3.4.11
Fit the back casing [12] onto the back cover [11].
Fig. 3.4.12
Precisely clean and degrease the sealing face of the
dynamic part of the mechanical seal [15A].