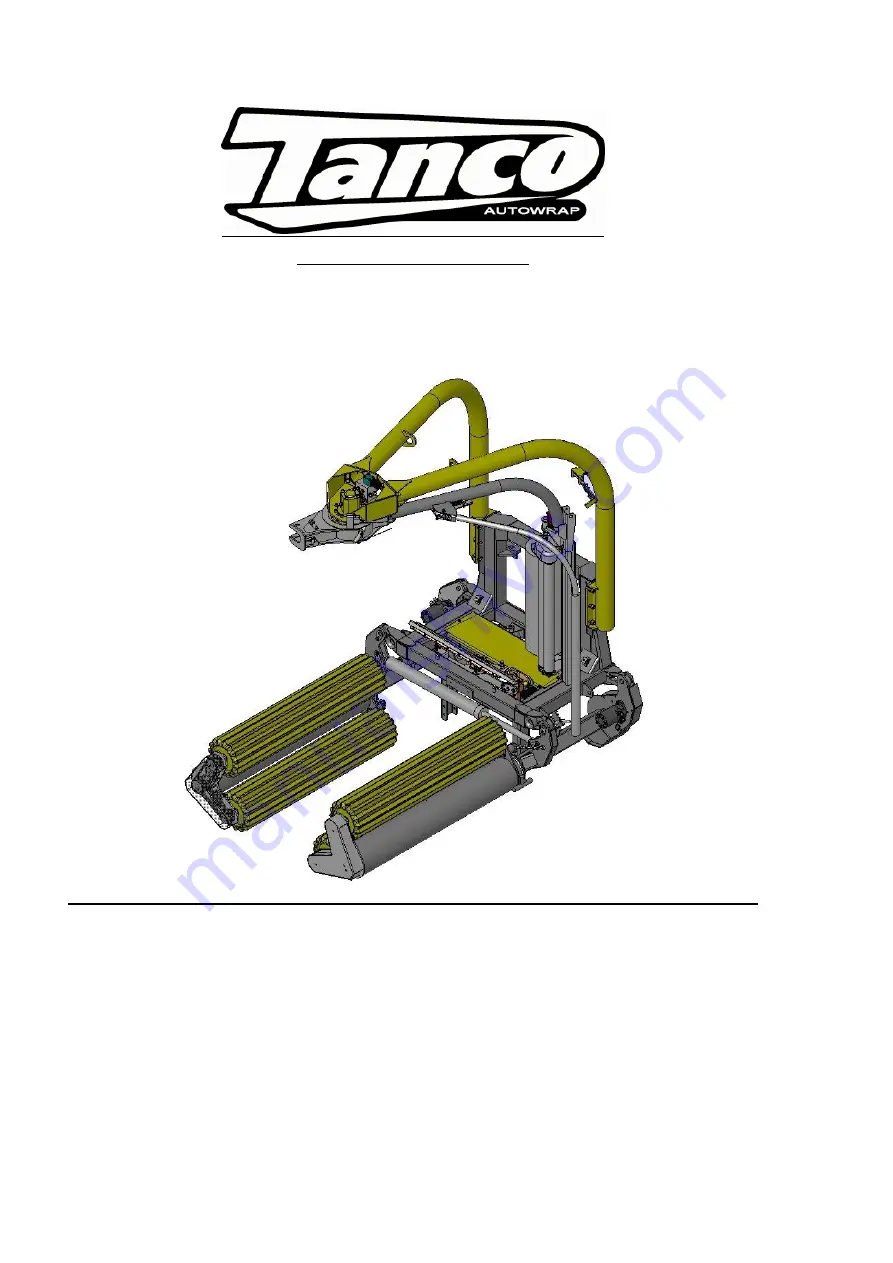
TANCO AUTOWRAP
1510 / 1514
OPERATORS HANDBOOK
WD66-1510 / 1514-M0407
Tanco Autowrap Ltd.
Royal Oak Road
Bagenalstown
Co. Carlow
Ireland
Tel.: +353 (0)5997 21336
Fax: +353 (0)5997 21560
E-Mail: [email protected]
Internet: www.tanco.ie
TANCO AUTOWRAP
1510 / 1514
OPERATORS HANDBOOK
WD66-1510 / 1514-M0407
Tanco Autowrap Ltd.
Royal Oak Road
Bagenalstown
Co. Carlow
Ireland
Tel.: +353 (0)5997 21336
Fax: +353 (0)5997 21560
E-Mail: [email protected]
Internet: www.tanco.ie