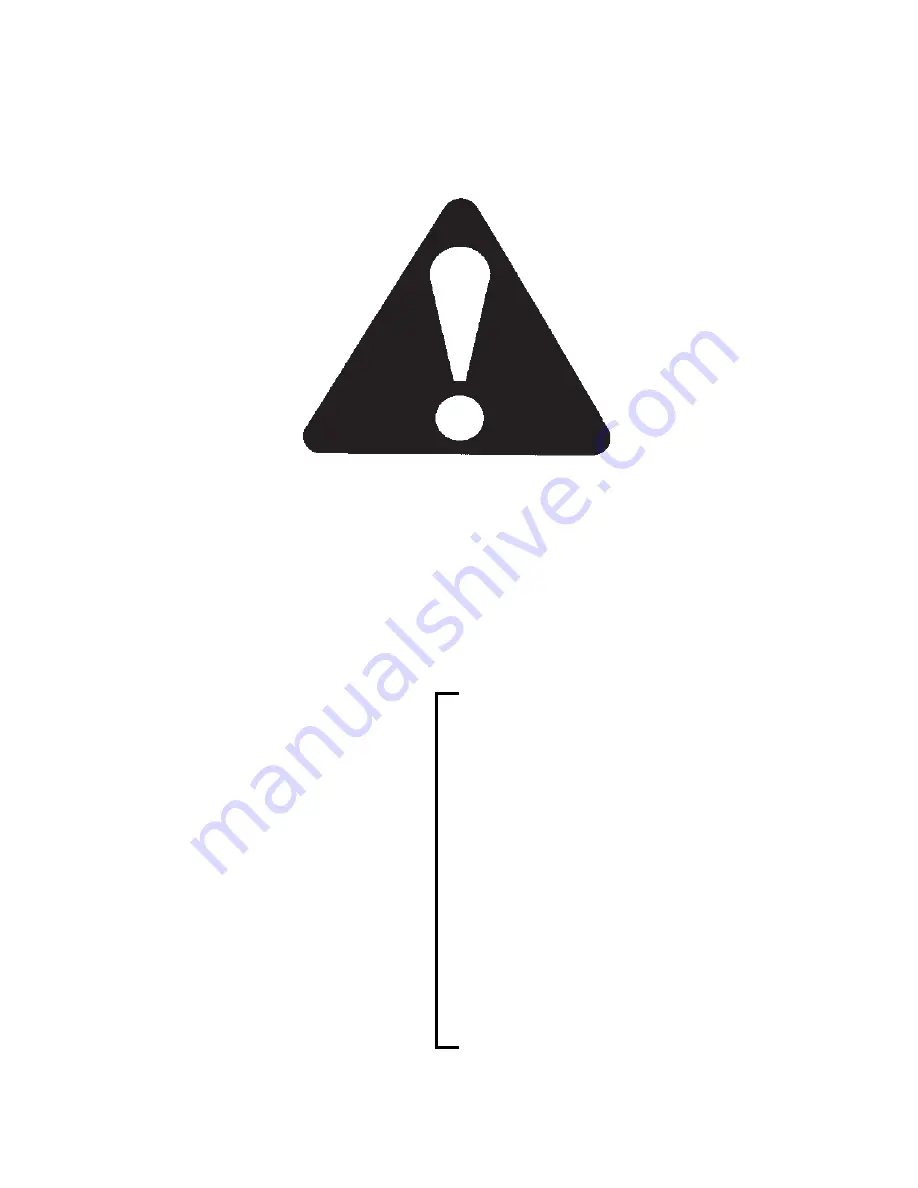
6
Accidents Disable and Kill
Accidents Cost
Accidents Can Be Avoided
Why is SAFETY important to you?
3 Big Reasons
ous situation that, if not avoided, will
result in death or serious injury. This
signal word is to be limited to the most
extreme situations, typically for ma-
chine components that, for functional
purposes, cannot be guarded.
Indicates a potentially hazardous situa-
tion that, if not avoided, could result in
death or serious injury, and includes
hazards that are exposed when guards
are removed. It may also be used to
alert against unsafe practices.
Indicates a potentially hazardous situa-
tion that, if not avoided, may result in
minor or moderate injury. It may also
be used to alert against unsafe prac-
tices.
SIGNAL WORDS:
Note the use of the signal words
DANGER,
The Safety Alert symbol identifies
important safety messages on the
Tamarack Heat King and in the
manual. When you see this symbol,
be alert to the possibility of personal
injury or death. Follow the instruc-
tions in the safety message.
This Safety Alert symbol means
ATTENTION! BECOME ALERT!
YOUR SAFETY IS INVOLVED!
WARNING
and
CAUTION
with the safety
messages. The appropriate signal word for
each message has been selected using the
following guide-lines:
SAFETY
SAFETY ALERT SYMBOL
DANGER
-
Indicates an imminently hazard-
WARNING
-
CAUTION
-