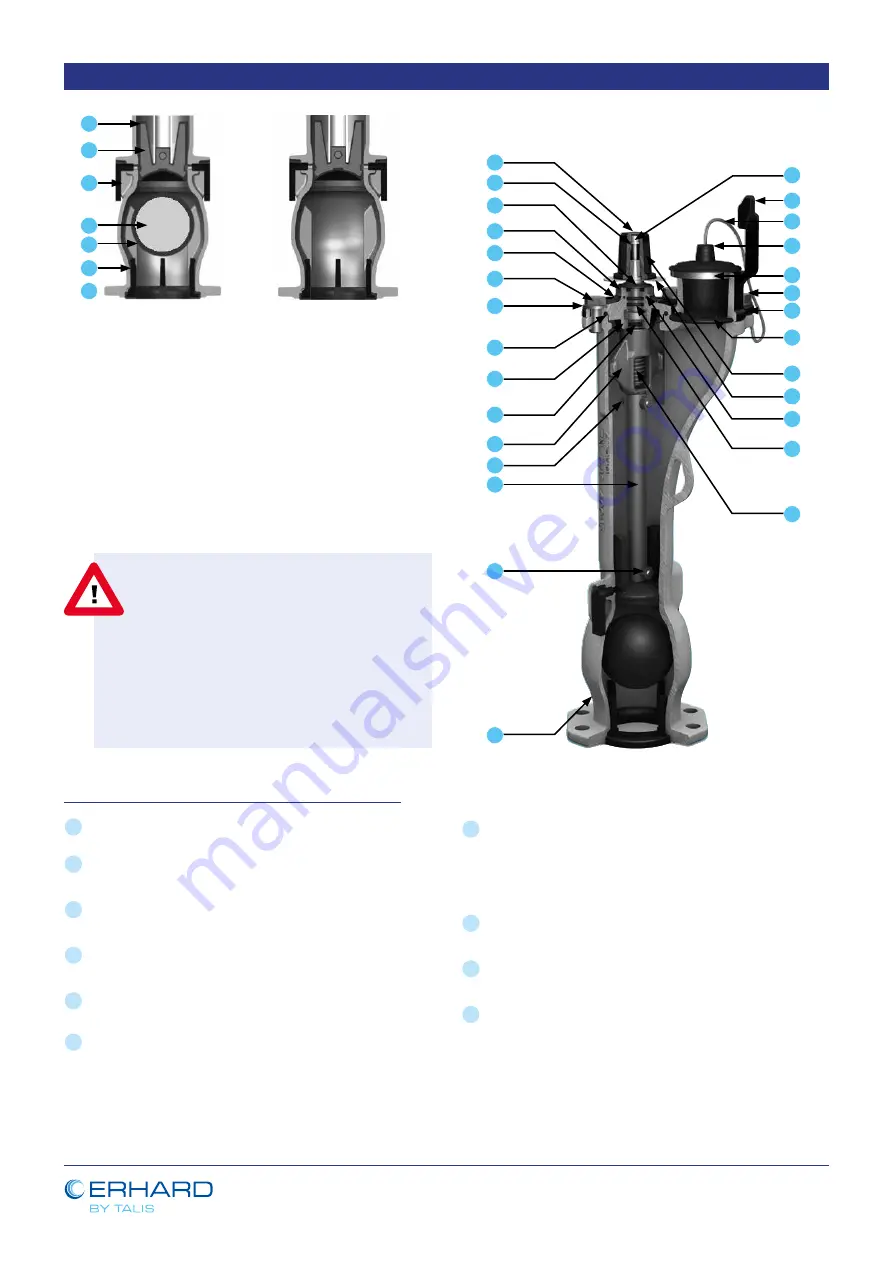
P15
/19
IOM_FIH210201_HALIOS STD-PREM_EN
The technical data and performance may be modified
without prior notice depending on the technical advances.
Our underground fire hydrants are maintenance free.
However, the complete bonnet, the operating inside trim, and
the complete outlet claw (including foreign matter deflector
and cap) can be removed and installed from the road through
the street cap (see section 7.4 for composition of spare parts
set). In the event that it is necessary to replace any part of
the hydrant, follow the instructions below. Replacement of the
shut-off ball, inlet flange gasket or drain tube can be done only
if the hydrant is totally disassembled from the water network.
7.3 Replacement
WARNING
Before carrying out inspection or any repair work on the
hydrant, the pipe section in which the hydrant is installed
must be depressurized and safe, e.g. by closing the gate
valve and emptying. A built-in double shut-off and / or
closed gate valve installed upstream of the hydrant are
no guarantee that the hydrant inside is depressurized.
After maintenance works, when putting back under
pressure, it is essential to operate the hydrant very
slowly when opening because some air under pressure
might have become trapped.
16
27
8.4
8.1
7
13
10
25
26
2
5
3
6
12
1
15
18
17
13
12
20
21
19
14
11
8.3
8.2
9
4.2
4.1
22
23.1
23.2
24.1
24.2
Double shut-off (UHAD)
Single shut-off (UHA)
7.3.1 Replacement of the complete bonnet:
1
Isolate the network section where the hydrant is installed
(upstream).
2
Depressurize the network section where the hydrant is
installed.
3
The hydrant should be fully closed by turning the square
cap (14) clockwise.
4
Completely unscrew the hexagonal bolts (13) of the bonnet
(7).
5
Turn the square cap (14) anti-clockwise until the operating
stem (9) is out of the operating nut (2).
6
Remove the complete bonnet (7) including the bonnet
O-ring (10).
7
Replace the complete bonnet by a new one (7) including
a new bonnet O-ring (10). Before installation, lubricate the
operating stem (9) and wedge nut (2) and bonnet O-ring
(10) with a small amount of appropriate grease (see in the
paragraph 7.1).
8
Re-assemble the complete bonnet (7), repeating these
operations in reverse order.
9
Make a full opening and closing of the hydrant without
pressure.
10
Check the correct operation of the product under pressure.
When opening, be careful of the release of air that might have
become trapped under pressure.