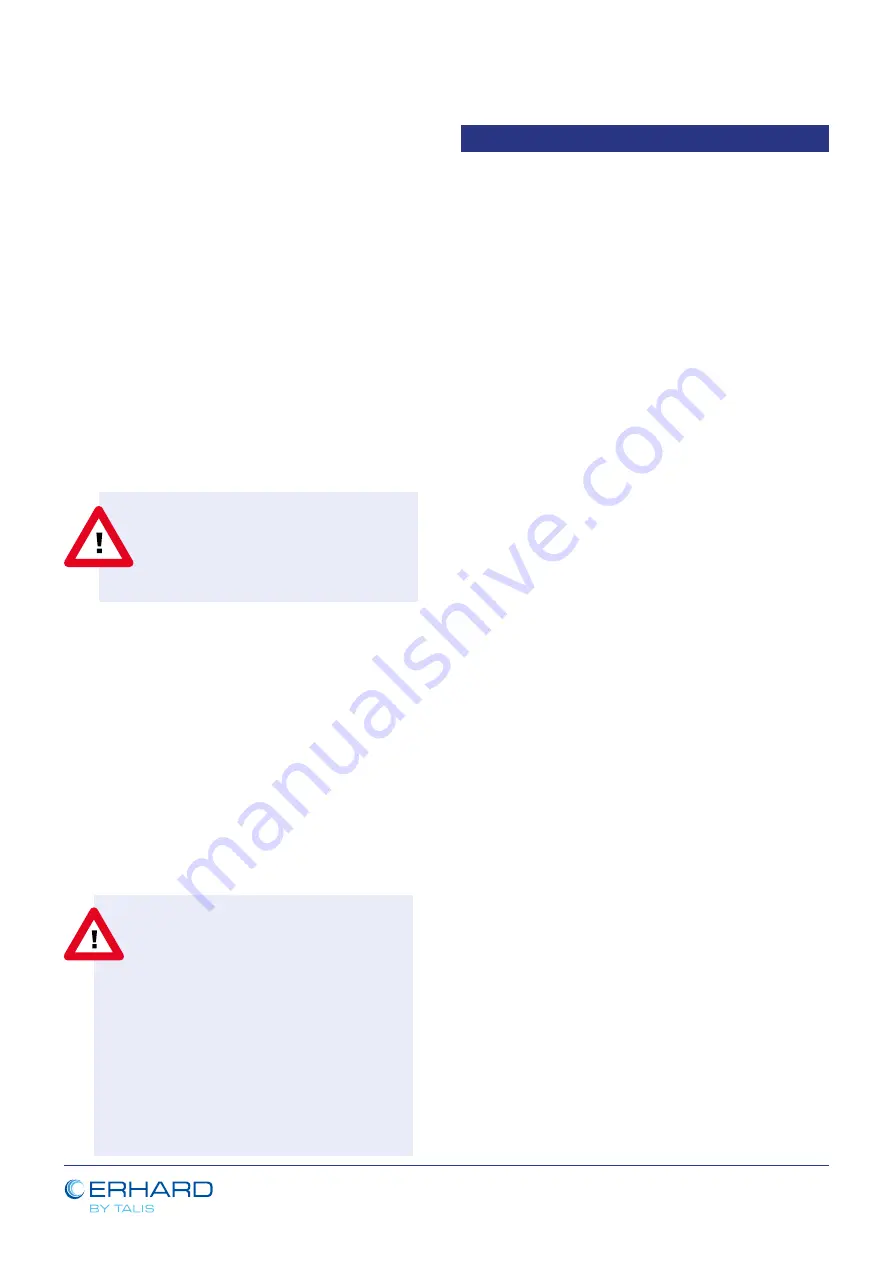
P13
/19
IOM_FIH210201_HALIOS STD-PREM_EN
The technical data and performance may be modified
without prior notice depending on the technical advances.
7 - MAINTENANCE
7.1 Maintenance recommendations
If they are used correctly, our underground fire hydrants are
maintenance-free. However, the performance and operating
conditions of parts of the system must be checked at regular intervals.
Visual and functional inspections and the resulting maintenance
work on the hydrant must only be carried out by qualified persons
(DVGW W400-3 (A)) and must be documented. In accordance with
DVGW leaflet W 392 / W331, monitoring of the functional capability
and tightness at MOT should take place at regular intervals, at least
≤4 years with regard to:
• Visual inspection to the maximum extent (integrity of corrosion
protection, presence of the identity disc, integrity of the claws for
the standpipe insert, complete emptying of the body, the condition
of the foreign matter deflector and / or presence and correct seat
of the cover of the claw, etc).
• Functional inspection by opening and closing the valve over an
entire stroke (easy mobility of the shut-off, complete emptying of
the body, …).
• Check for smooth operation and tightness at MOT values.
If the torque necessary to close or open the hydrant is above MOT
values, a proper maintenance must be done including changes of the
damaged components.
The operating/maintenance visits must be increased to an adapted
frequency if the gate valves are used with raw water or water that
tends to form deposits (limestone, etc) and incrustations, or in the
case of highly abrasive water, strong hydraulic conditions, strong
environmental variations.
Lubricant/grease must be approved for potable water application, and
must be appropriate to the functions it must fulfill. Recommended
lubricants for all types of maintenance (see paragraph 7.3) and for
flow medium water is: Klüber Synth VR 69-252 as unique grease
(silicone-free lubricant).
NOT ALLOWED OPERATION
Continuous operation in throttle position leads to
cavitation damage due to the high flow velocity.
An extension of the operating key by use of a lever
or similar is not allowed.
It is not permitted to open the hydrant against a
closed inspection or revision valve.
Do not exceed operating temperature limits and
operating pressure limits.
Closed valve may only be loaded up to nominal
pressure.
To avoid overpressure in the body and thus damage
to the shut-off cone insert, do not close the hydrant
against a closed standpipe or a closed outlet fitting.
The nominal pressure in the pipeline should not exceed the allowable
operating pressure that the hydrant can support.
On our hydrant, the materials and the corrosion protection are resistant
to the commonly used disinfectant products. Take care not to affect
hydrant materials when using cleaning / disinfecting products.
TO OPEN
• Carry out traffic safety procedure.
• Clean the outside street cap area of road dirt.
• Loosen the tight-fitting cover of the street cap, if necessary use a
suitable cover lifter.
• Take out the cover and swing it sideways.
• Clean the claw and the claw-cover of dirt, then lift the cover, then
rinse it without the standpipe.
• Insert the standpipe with the claw nut screwed down into the claw
and turn it to the right until fixed and tight seating is achieved.
• Fully open the outlet of the standpipe so that the air can escape
when the hydrant is opened.
• Turn the key C (according DIN 3223) slowly, anti clockwise till the
water flushes and clean the hydrant and the standpipe with the
escaping water.
• Close the outlet fitting on the standpipe and connect the hoses.
• Open the outlet fitting on the standpipe in order to get water.
WARNING
If this order is not followed, there is a risk
of polluting the drinking water.
TO CLOSE
• With the outlet fitting slightly open, close the hydrant completely
by turning clockwise till the stop. Then it`s recommended to turn
¼ turn to the left to decock the inner valve.
If the outlet fitting
of the standpipe is not open at the closing process, a positive
pressure may build up. If necessary , unscrew the hoses
(uncoupling).
• Once the hydrant is closed, loosen the standpipe by turning to
the left.
• Observe whether the water level in the body drops during
emptying.
• Close the claw with his cover
• Close the street cap
• Remove traffic safety