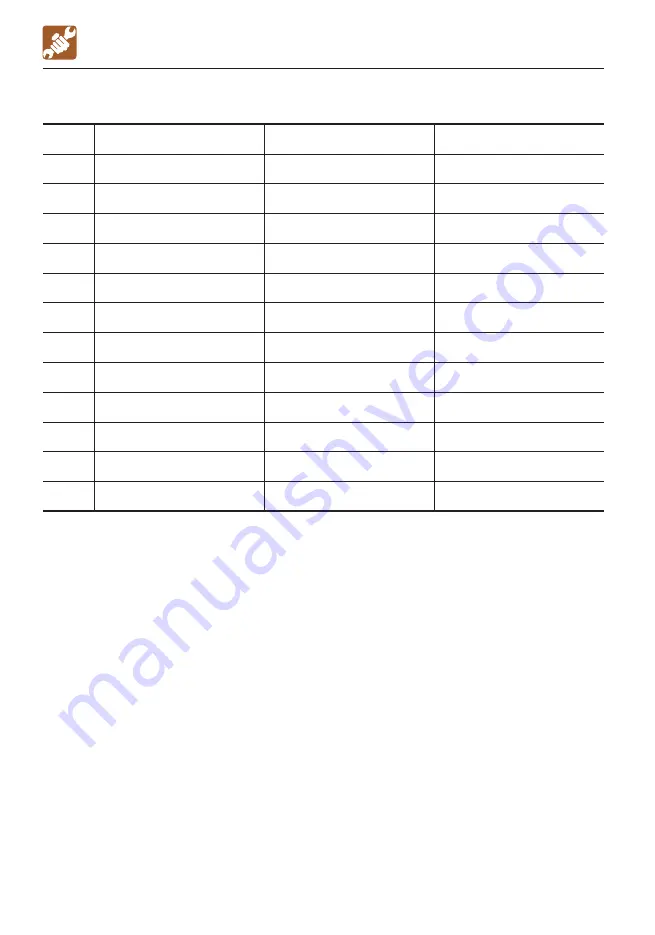
5-8
MAINTENANCE
SERVICE DATA
LIST OF TOOLS
Code
Part name
Part No.
Remarks
1
Spanner
19100-47081
10 - 12
2
Spanner
19100-47082
14 - 17
3
Screwdriver
19100-06112
(+) (–) replaceable shank
4
Filter wrench
19100-96081
5
Monkey wrench
16904-00250
250 mm
6
Pliers
16905-00200
200 mm
7
Spanner
16901-00013
13
8
Spanner
16900-01922
19 - 22
9
Spanner
16909-00026
26
10
Tool case
16914-00005
11
Grease gun
16910-60600
600 cc
12
Drain connector
15545-12201
Summary of Contents for TB215R
Page 10: ...0 8 ...
Page 11: ...1 1 SAFETY SAFETY ...
Page 44: ...1 34 SAFETY SAFETY SIGNS DECALS ...
Page 45: ...1 35 SAFETY SAFETY SIGNS DECALS No 00085 01011 ...
Page 46: ...1 36 SAFETY SAFETY SIGNS DECALS ...
Page 47: ...1 37 SAFETY SAFETY SIGNS DECALS ...
Page 48: ...1 38 ...
Page 49: ...2 1 CONTROLS ...
Page 77: ...3 1 OPERATION ...
Page 107: ...4 1 TRANSPORT ...
Page 112: ...4 6 ...
Page 113: ...5 1 MAINTENANCE ...
Page 149: ...5 37 MEMO ...
Page 169: ...6 1 TROUBLESHOOTING ...
Page 183: ...7 1 SPECIFICATIONS ...
Page 185: ...7 3 MEMO ...
Page 186: ...7 4 SPECIFICATIONS MACHINE DIMENSIONS MACHINE DIMENSIONS ...
Page 188: ...7 6 SPECIFICATIONS OPERATING RANGES ...
Page 190: ...7 8 MEMO ...
Page 192: ...7 10 SPECIFICATIONS LIFTING CAPACITIES ...
Page 193: ...7 11 SPECIFICATIONS LIFTING CAPACITIES ...
Page 194: ...7 12 ...
Page 195: ...8 1 OPTIONS ...
Page 203: ...8 9 ...