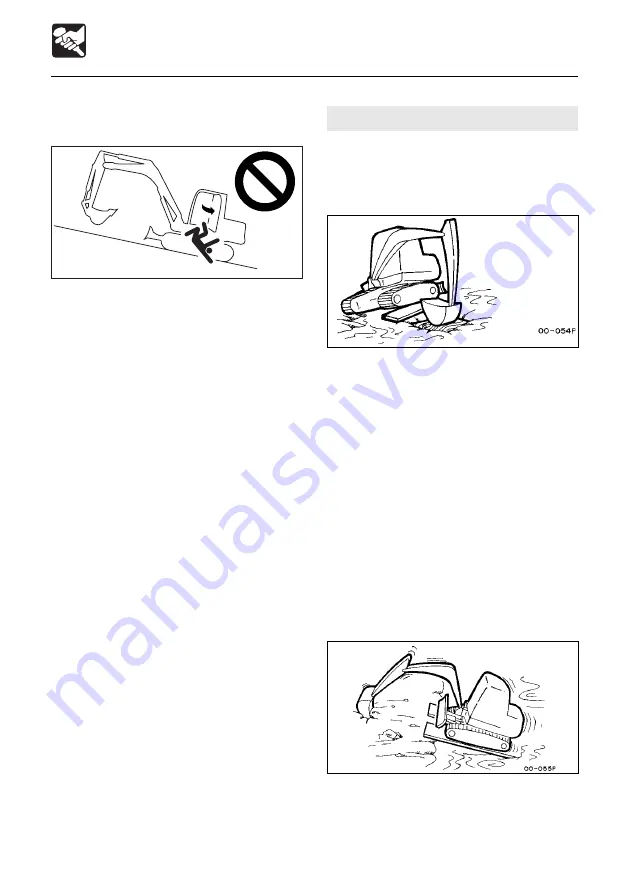
81
OPERATION
Operating Procedures
Getting Out of Mud
If the machine gets stuck in mud, use the
procedure below to get it out.
If one crawler is stuck
1. Slew the bucket to the side which is stuck.
2. Set the arm and boom to an angle of 90 to
110
°
.
3. Press the bottom of the bucket (not the
teeth) against the ground.
4. Place a plank, etc., under the lifted crawler.
5. Lift the bucket and slowly move out of the
mud.
If both crawlers are stuck
1. Perform steps 1 to 4 above for both
crawlers.
2. Dig the bucket into the ground in front of
the machine.
3. Pull with the arm and travel forward
simultaneously to slowly move out of the
mud.
Do not open the door while traveling on
slopes
Opening the door while traveling on slopes
is dangerous, as the force required to open
and close the door changes abruptly. Always
keep the door closed when traveling on
slopes.
E4D048
Summary of Contents for AF4E001
Page 6: ...4...
Page 8: ...6...
Page 36: ...34...
Page 91: ...89 TRANSPORT Loading and Unloading 90 Securing the Machine 91 Cautions on Transporting 92...
Page 153: ...151 MEMO...
Page 154: ...152 SPECIFICATIONS Machine Dimensions J1K001 N L M D Q P J H K C F G A S E B R T U...
Page 156: ...154 SPECIFICATIONS Operating Range J1K002 D J H K C F G A E B...
Page 158: ...156 MEMO...
Page 162: ...160...
Page 167: ...165 OPTIONS Safety Signs Decals 1 No 03593 32200 2 No 03593 32300...
Page 168: ...166 MEMO...
Page 173: ...171 MEMO...
Page 174: ...172...
Page 175: ...173 INDEX...