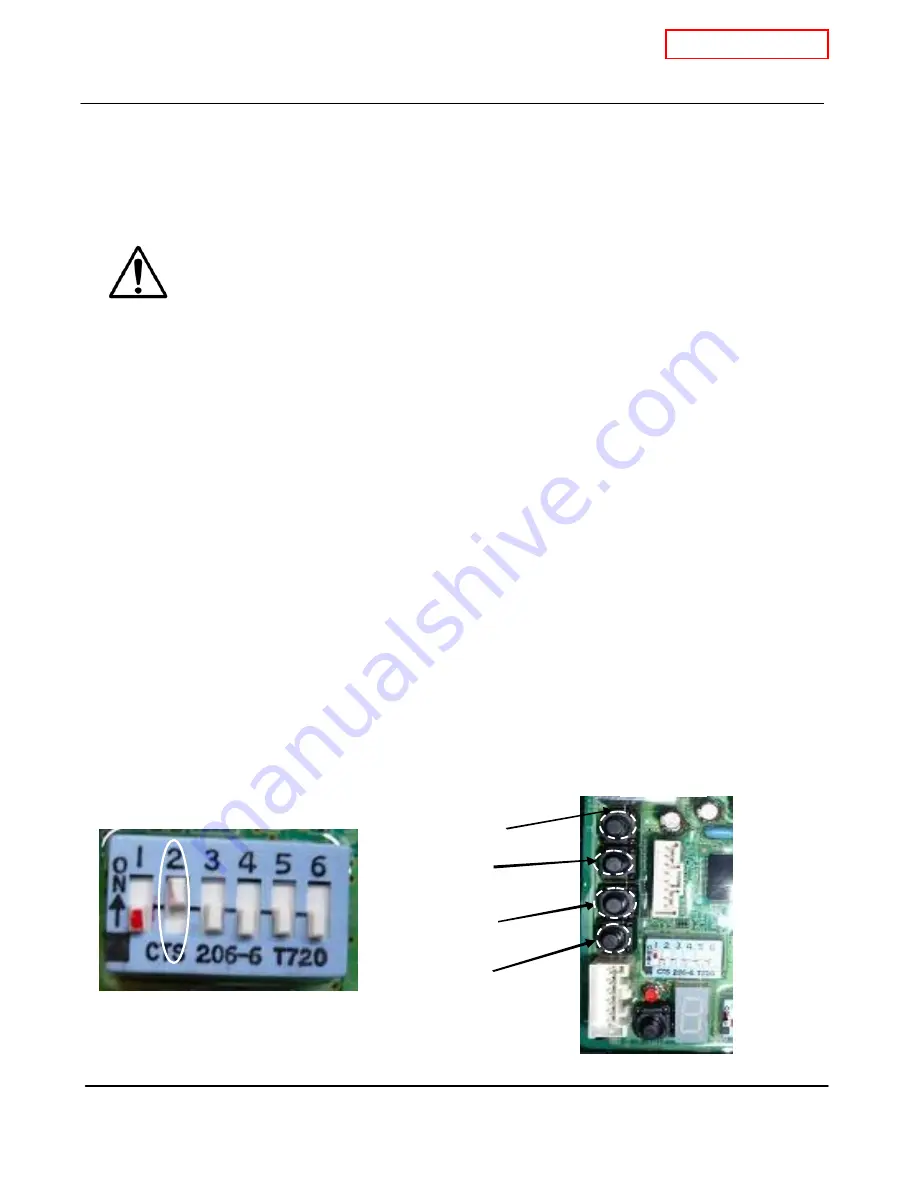
T-K3 Service Manual
Ver. 1.05
59
CONFIDENTIAL
Figure 2
12-15. Manually adjusting the fan motor speed
While the FM+ dipsw itch will automatically increase the fan speed by 6%, the fan motor
speed on the T-K3 can also be manually adjusted. In order to perform manual
adjustments to the speed, a TM-RE10 or TM-RE30 remote controller is required.
Manually adjusting the fan motor speed of the T-K3 w ill change the amount of intake
air for combustion, w hich can cause excess CO emission from the exhaust chamber
if the fan motor speed is set incorrectly. Therefore, this procedure should
never
be
performed unless Takagi USA has given consent and author ization.
Adjusting maximum fan motor speed
1. While T-K3 is in operation, set dipsw itch No.2 to the “ON” position. ( Figure 1)
2. On the temperature remote controller, display mode #3 (fan motor speed) by entering the
“Diagnostics mode” (Refer to Section 12-1).
3. Press and hold dow n the
“MAX”
button on the computer board. While holding dow n the
“MAX” button, press either the
“INCREASE”
or
“DECREASE”
button to increase or decrease
the fan motor speed, respectively (Figure 2). Refer to the remote controller display to verify that
speed has been set to desired value.
4. After fan speed has been set, set dipswitch No.2 back to the “OFF” position.
Adjusting minimum fan motor speed
1. While T-K3 is in operation, set dipsw itch No.2 to the “ON” position. ( Figure 1)
2. On the temperature remote controller, display mode #3 (fan motor speed) by entering the
“Diagnostics mode” (Refer to Section 12-1).
3. Press and hold dow n the
“MIN”
button on the computer board. While holding dow n the
“MIN” button, press either the
“INCREASE”
or
“DECREASE”
button to increase or decrease the
fan motor speed, respectively (Figure 2). Refer to the remote controller display to verify that
speed has been set to desired value.
4. After fan speed has been set, set dipswitch No.2 back to the “OFF” position.
W ARNING
T-K3 computer board
Decrease button
Increase button
MIN button
MAX button
Figure 1
Dipsw itch settings