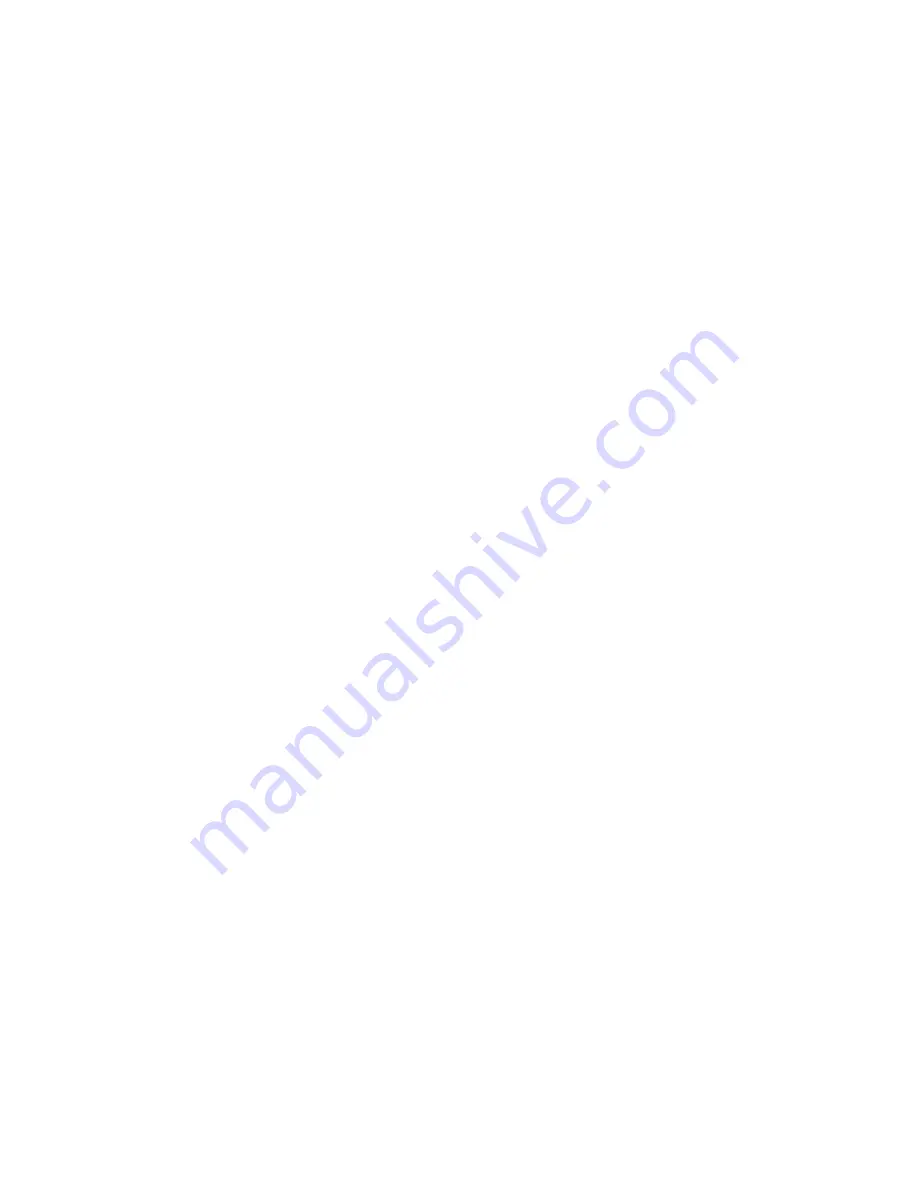
6
(2) Total Head Measurement – The total pumping head consists
of: distance from the water level in the sump (when pumping)
to the center of the discharge pressure gauge, plus the dis-
charge gauge reading, the friction loss through the column
and head, and the velocity head at the discharge.
NOTE: Convert pressure gauge reading to feet of liquid
by multiplying the reading times 2.31 times the specific
gravity of liquid.
(3) Horsepower Measurement – Measure horsepower con-
sumption of the pump by a direct reading of a wattmeter and
applying the reading to the following formula:
Horsepower Formula:
BHP = (KW Input x Eff)
0.746
Pump Efficiency Formula:
Pump Efficiency = (TDH x GPM x SG) / (3960 x BHP)
Where:
BHP =
Brake Horsepower Delivered
KW Input = Real Input Power (KW)
Eff =
Motor Efficiency
SG =
Specific Gravity of Liquid
TDH =
Total Dynamic Head
GPM =
Gallons per Minute
F: ENGINEERING
Customer:
TACO Model:
Lateral:
K Factor:
Impeller Type:
Impeller Adjutment:
Minimum Submergence:
G: MAINTENANCE
G1: GENERAL
1. For normal operation and maintenance of driver, follow the
instructions of the driver manufacturer.
2. If the pump is oil lubricated, check the oil level in the lubrica-
tor and refill on a regular schedule.
3. If the unit requires pre-lubrication, make certain this process
is started with ample time prior to pump start-up to insure that
all bearings are properly wetted.
4. Apply grease to the packing box assembly at the rate of
1
⁄
4
to
1
⁄
2
oz. for each 24 hours of operation. See Section G5
(PREVENTATIVE MAINTENANCE).
5. Bowl bearings are self lubricated by the liquid pumped. Lower
suction bowl bearing is packed at the factory with no mainte-
nance required in the field.
6. The packing box should seldom require adjustment but in the
event that the leakage becomes excessive, see Section F4 for
details. Remember that overtightening wears out the packing
rings prematurely and causes scoring and damage to the top
shaft. Always adjust the gland with the unit running.
G2: BEARING REPLACEMENT
1. Alloy bearings, such as bronze, can be readily pressed in
with an arbor or screw press. If this is not available, they can
be driven in very carefully with a block of wood and a ham-
mer. Make certain that bearing projections are maintained.
2. Graphite and composition bearings do not possess great
tensile or compressive strength and cannot be driven in as
alloy bearings can. They must be pressed in with a slow,
continuous and even motion attained with an arbor or screw
press with a mandrel to fit the bearing properly. The hub bore
and the bearing should be lubricated with water to aid the
pressing operation. DO NOT LUBRICATE WITH OIL OR
GREASE.
G3: WEAR RING (optional) REPLACEMENT
1. Wear rings can be removed by cutting the cross section with
a chisel and prying one end inward until it is loose in the bore.
To install, make a mandrel to fit the wear rings and press in
with an arbor or screw press. In an emergency, the wear
rings can be installed by gently and evenly tapping around
the top edge with a wood block and a hammer or a rubber
mallet.
2. If impeller skirts are equipped with wear rings, cut the wear
ring cross section with a chisel and force off. Heat on the ring
will assist in the removal and installation. To install, make
a mandrel to fit the O.D. of the wear rings and press flush
with the bottom of the impeller skirts. If necessary, gently
and evenly tap around the top edge with a wood block and a
hammer or with a rubber mallet.
G4: PACKING REPLACEMENT
1. When the packing has been compressed to the point that the
gland is about to contact the upper face of the packing box,
remove the gland, add one extra packing ring and re-adjust.
If this fails to reduce the leakage, remove all of the packing
rings and repack with new rings.
2. These are the step-by-step procedures in repacking a packing
box in the pump:
a. Clean out the old packing. This includes the packing below
the lantern ring. Often the old packing below the lantern
ring is not replaced when repacking the gland as it should
be. Flexible packing hooks are available for removing the
packing.
b. Check the shaft for nicks and score marks; remove any
that are present; then clean carefully. Clean up the bore of
the box. Check the lantern ring to make sure the channels
and holes are not plugged up.
c. If the replacement packing is in the form of a continuous
coil or rope, it must be cut into rings before installing. After
cutting on the mark, the first length of packing may be
used as a template for cutting all the other rings. Begin by
installing the first ring. It is recommended that grease or oil
be smeared on at least the outer diameter of the ring.
d. With the aid of a split bushing, push the packing to the
bottom of the box. The O.D. of this split bushing should
be approximately .005 inch smaller than the bore of the
packing box to prevent the formation of a lip on the packing
that is being seated. Seat this bottom ring hard because it
must seal on the face of the packing box bearing as well as
against the shaft and the bore. See Figure G4.d.
e. Repeat this operation with each ring making sure to stag-
ger the gaps formed by the ends of the ring at 90 degree
intervals. See Figure G4.e.
f. If a lantern ring is used, be sure it is properly positioned
so it is centered with the drilling in the packing box. See
Figure G4.f.
g. Position the packing gland. Tighten it down evenly. The
packing gland must not be cocked within the packing box.
An unsquare packing gland causes uneven compression
of the packing rings and, more importantly, damage to the
shaft. Good practice is to allow at least
1
⁄
4
inch from the top