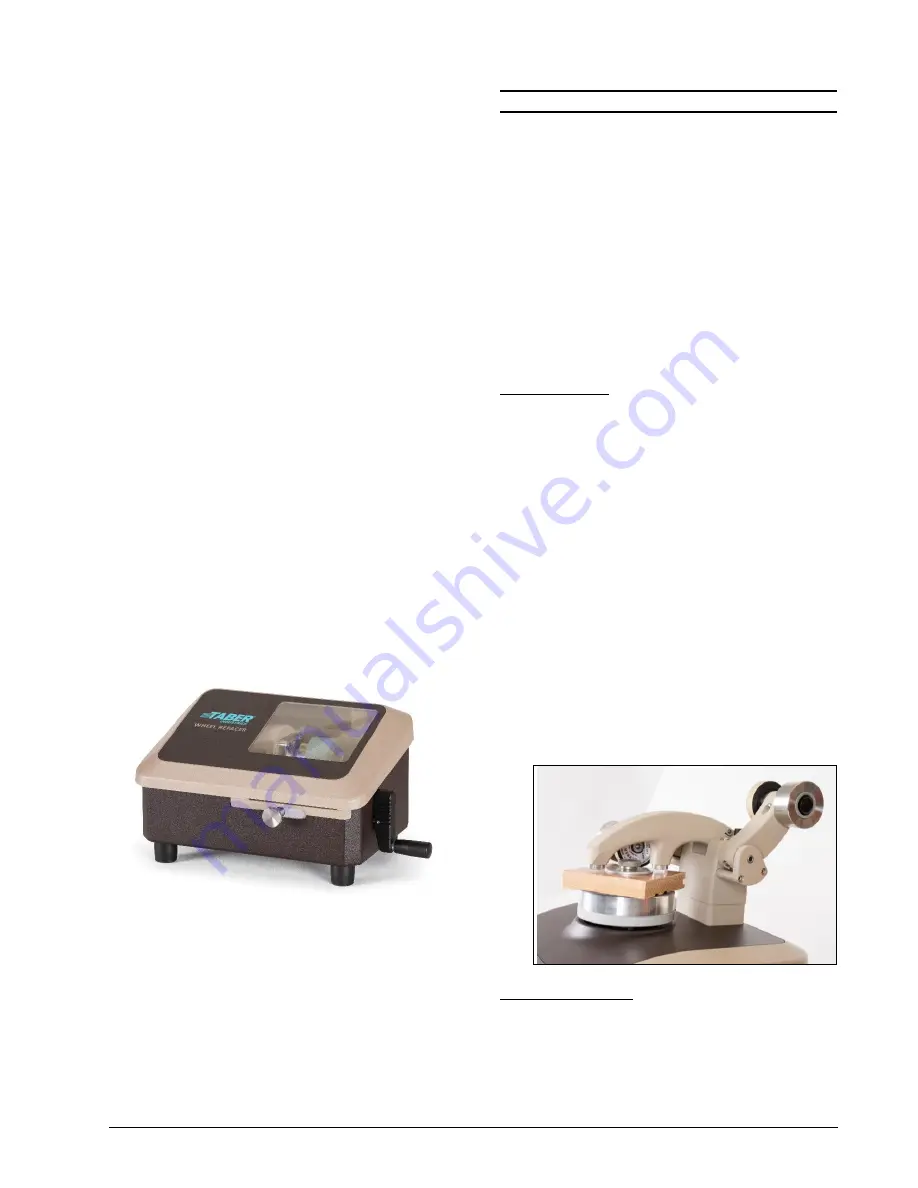
Model 1700 / 1750 Rotary Platform Abraser
15
Operating Instructions ver. 1.0
p/n 135505
Refacing Vitrified Wheels (Calibrade)
All Calibrade wheels are diamond trued at the
factory and may be used continuously without
further refacing until the abrading surfaces show
indications of becoming:
Worn out of round
– Occasionally, wheels
become out of round due to an uneven surface
of the test specimen or other reasons. The
normal abrading surface of the wheels should
be concentric with the hub.
Crowned
– The working surfaces of wheels
that are “crowned” appear slightly rounded. To
check for this condition, place a straight edge
on the two wheels. The straight edge should be
in contact with the full width of the wheels.
Clogged
– “Clogged” wheels can be identified
as adhesive buildup of wear debris on the
working faces of the wheels and should not be
confused with the discoloration caused by
abrading dust.
Refacing is also advised when starting a series of
comparative tests or changing to an entirely
different material. In some instances, where there
is a tendency for the working surfaces of the wheels
to pick up excess material, it may be desirable to
reface the wheels before testing each specimen.
To properly reface Calibrade wheels, a Taber
Wheel Refacer must be used. This instrument
utilizes a diamond tool that is traversed across the
working surface to precision dress the abrading
wheels.
NOTE:
Refacing Calibrade wheels may leave a sharp
edge that may sever threads when testing textile fabrics.
It is acceptable to remove this sharp edge prior to testing.
To do so, cut a small strip from an S-11 refacing disc and
hold it lightly against the outer edge of each wheel.
Manually turn the nut to rotate the motor shaft. Reverse
the wheels on the arbor and round the opposite corners.
Only the extreme sharpness of the edges should be
removed. A radius of 0.4 mm is sufficient.
SPECIMEN PREPARATION
As you start testing, use of these guidelines should
assist in developing a test procedure that will yield
reproducible test results, accurate within the
variations of quality inherent in the material itself.
The suggested number of test specimens from
each laboratory sampling unit is a minimum of
three (3).
All specimens should be labeled to maintain
specimen identity.
Specimen Size
Rigid Materials
– Rigid specimens are often cut
from a larger sheet utilizing an appropriate cutting
method. Specimens should be approximately 100
mm square with surfaces plane and parallel. A
6.5mm diameter hole must be drilled in the center
of the specimen to secure it to the standard
specimen holder (SH-125). The material thickness
that can be evaluated with the Taber Abraser
without additional accessories, is 6.5 mm or less.
NOTE:
The width of the wear path is 12.7 mm, and
located 31.75 mm from the center of the specimen.
NOTE:
Optional “Drive Pin” specimen holder (SH-19) is
available for testing rigid materials that are difficult to drill
a center hole in.
NOTE:
Optional accessories are available to test
specimen thickness greater than 6.5 mm. Materials
greater than 6.5 mm but less than 12.7 mm can be
evaluated using the S-21 Extension Nut. The Arm Height
Extension modification will permit testing up to 40 mm in
thickness.
Flexible Materials
– Flexible specimens are
typically circular and require the use of the hold-
down ring. A 130 mm - 135 mm diameter specimen
is required so the hold-down ring will grip the
overlapped material. If a mounting card is used, the
specimen should be approximately 108 mm in
diameter.