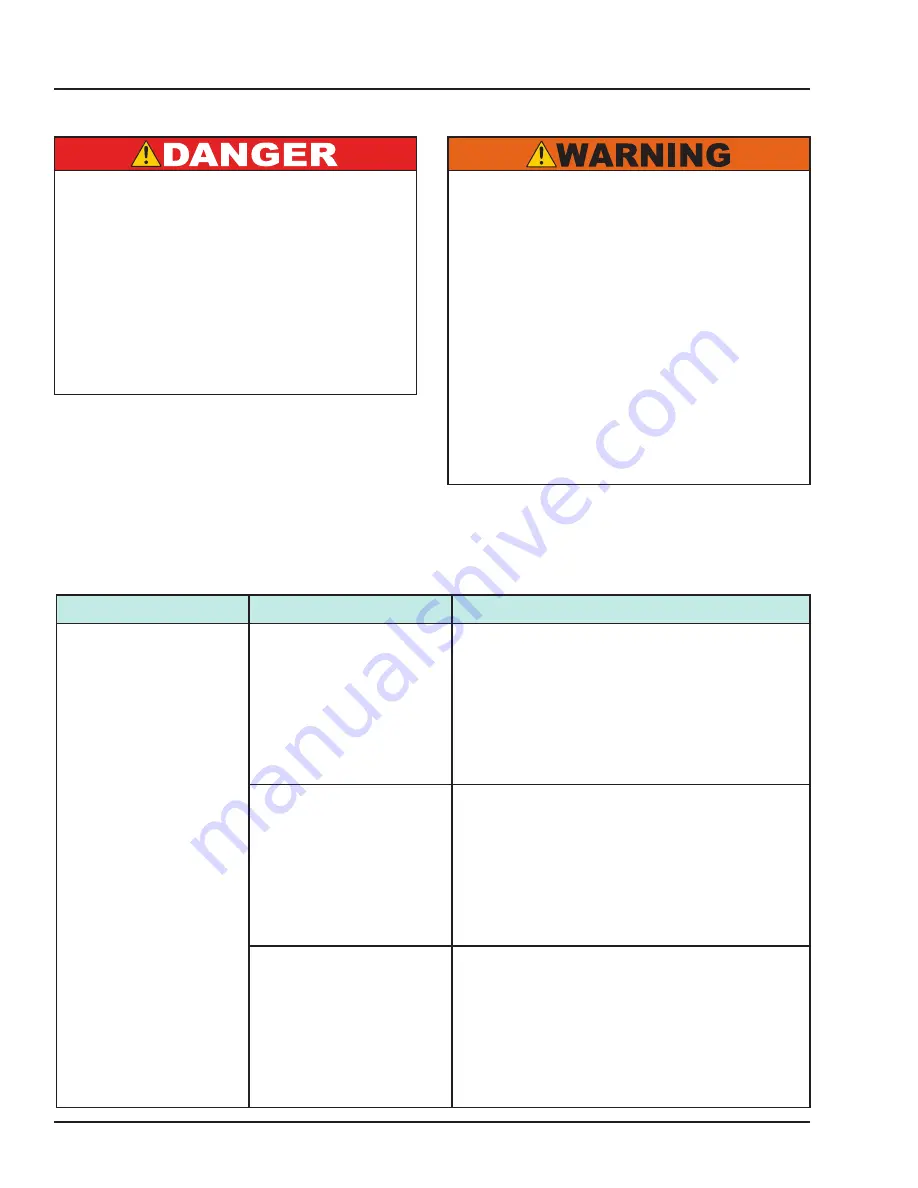
30
4111-0014 — Apr. 2020
© 2020 Systems, LLC
Symptom
Possible Cause
Solution
Restraint will not raise or
lower.
Debris/damage.
Remove debris guard; check for debris jammed in
or damage to scissor mechanism.
Inspect track for debris.
Improper lubrication.
Lubricate latch release leveler.
Lubricate pivot points on scissor mechanism.
Damaged parts.
Damaged or missing compression spring.
Damaged or missing scissor mechanism springs.
Worn out or damaged flanged bearings in scissor
mechanism.
Damaged scissor mechanism.
TROUBLESHOOTING
When service under the dock leveler is required,
always lock all electrical disconnects in the OFF
position after raising the platform and engaging the
maintenance prop.
Always post safety warnings and barricade the
work area at dock level and ground level to prevent
unauthorized use of the dock leveler before
maintenance is complete.
A hard hat or other applicable head protection
should always be worn when working under or
around a dock leveler.
Always stand clear of platform lip when working in
front of the dock leveler.
Unless the dock leveler is equipped with a tethered
remote, two people are required to engage the
maintenance prop: one person to operate the unit,
the other person to engage the maintenance prop.
In addition, it is recommended and good safety
practice to use an additional means to support
the dock platform and lip anytime when physically
working in front of or under the dock leveler. This
additional means may include, but is not limited to a
boom truck, fork truck, stabilizing bar or equivalent.
All Units