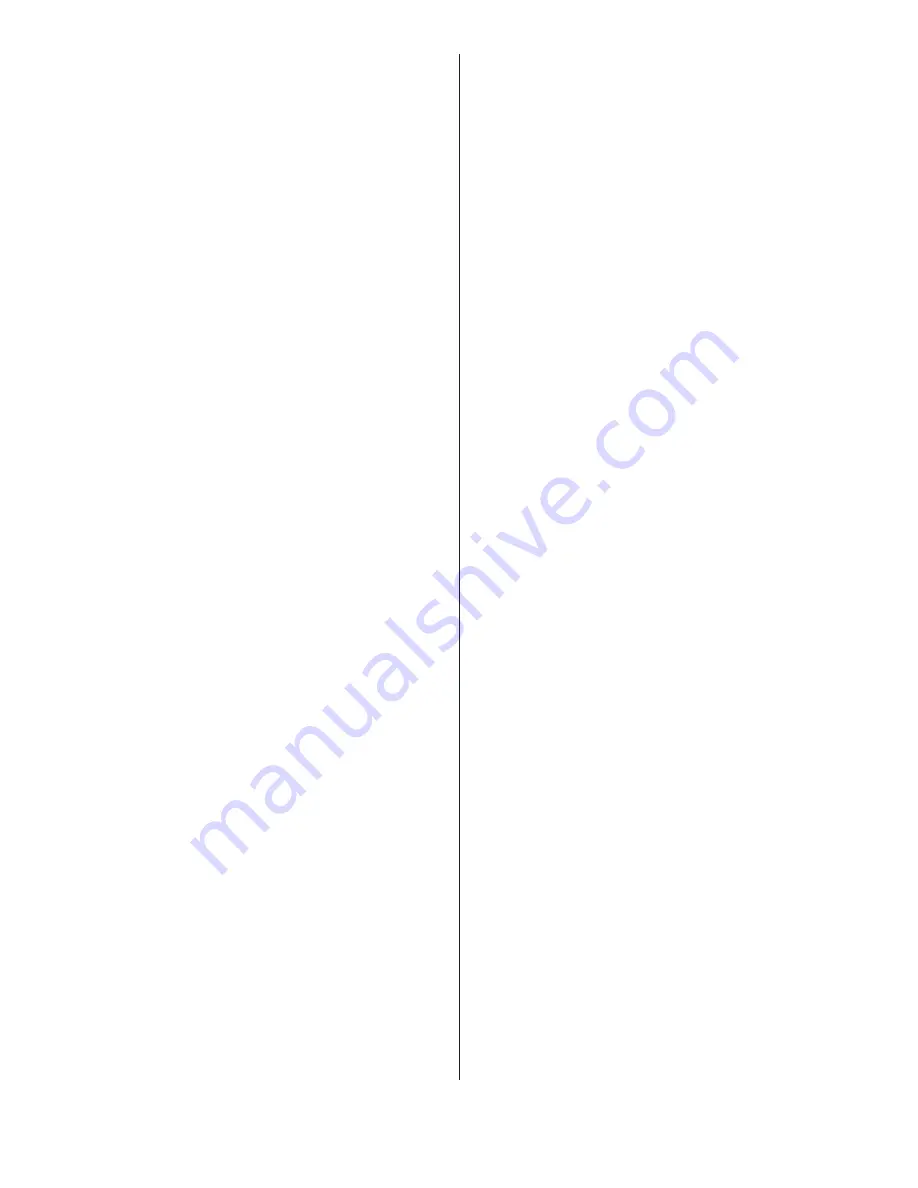
Systematics , Inc. 1025 Saunders Lane West Chester, PA. 19380
3
DESCRIPTION
The MP140 consists of a combina-
tion MIG welding power source and
wire feed unit, a MIG torch with 10
foot cable, a ten foot work (ground)
cable with ground clamp, a fifteen
foot power input cable, a gas
regulator/flowmeter, a torch ac-
cessory kit, and a built-in cylin-
der rack and industrial wheel kit.
Welder controls are simple and
clearly marked. The output voltage
is controlled by a six position tap
switch, providing six voltage se-
lections. Voltages can be moni-
tored by the voltmeter on the
control panel. Wire feed speed is
controlled by the wire speed poten-
tiometer.
An OPTIONAL SPOT/STITCH WELD
(SSTP-2)control module with ad-
justable timer circuit provides
Consumable MIG Spot Welding or
Stitch Welding capabilities of
light gauge steel.
SPECIFICATIONS
PART NUMBER:
MP140
INPUT POWER REQUIREMENTS:
Voltage
115 volts AC
Phase
single phase
Frequency
50/60 hertz
Current
(see OUTPUT POWER)
OUTPUT POWER @ 100% Duty Cycle:
15 Amps Input Current =
100 Amps
20 Amps Input Current =
120 Amps
OUTPUT POWER @ 60% Duty Cycle:
30 Amps Input Current =
140 Amps
DUTY CYCLE TIME PERIOD:
10 minutes
OPEN CIRCUIT VOLTAGE:
18 - 33 volts DC
SPECIFICATIONS (Cont.)
ARC VOLTAGE:
14 - 24 volts DC
WELD CURRENT RANGE:
30 - 140 amps
WIRE TYPES:
mild steel,
stainless steel, aluminum,
bronze, flux cored, flux cored
-
gasless
WIRE SIZES:
.023" - .045" steel,
3/64" aluminum,
(.023" - 3/64" alum. w/ Spool Gun)
.030" - .035" bronze,
.030" - .045" flux cored
(gas shielded or gasless)
WIRE FEED SPEED RANGE:
50 - 500 inches per minute
SHIELDING GASES:
For Steel
Argon/CO2 mix or CO2
For Aluminum, Bronze
Argon
For Stainless Steel
Argon + 2% Oxygen
For Flux cored
Argon/CO2 mix or
CO2
DIMENSIONS:
Height
31 in.
Width
14-1/2 in.
Depth
35-1/2 in.
Weight
175 lbs.
TORCH SPECIFICATIONS
NECK ANGLE:
60 degrees
LEAD LENGTH:
10 feet
OVERALL LENGTH:
10 feet
COOLING METHOD:
gas (air)
RATING - 60% DUTY CYCLE:
With Argon/CO2 gas
200 amps
With CO2 gas
225 amps