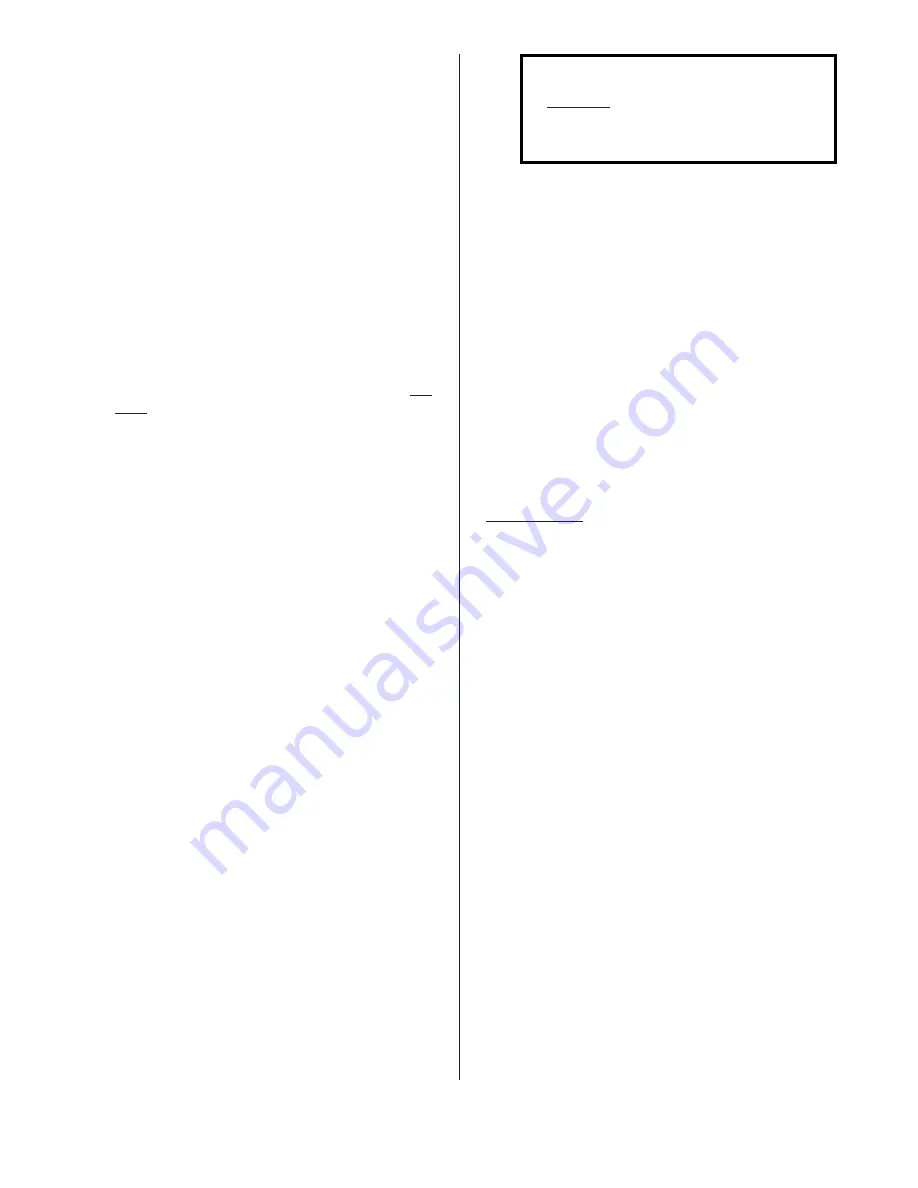
Systematics , Inc. 1025 Saunders Lane West Chester, PA. 19380
13
OPERATING HINTS
BURN BACK
In the event the welding wire
burns back into the contact tip:
1. Remove the nozzle from the
torch.
2. Unscrew the contact tip from
the gas diffuser using a pair of
pliers as the tip will be very
hot.
3. Free the wire from the contact
tip and clean the end of the tip
so the new wire will slide
smoothly through the hole. DO
NOT use a drill or reamer to
clean the hole as that will
enlarge it and cause an erratic
arc. Replace the contact tip if
it is badly damaged.
4. Install the contact tip in the
torch and tighten it firmly
with an appropriate wrench.
5. Reinstall the torch nozzle.
6. If the wire continues to burn
back, check for erratic wire
feed, or speed up the wire by
increasing the WIRE SPEED con-
trol setting or reducing the
VOLTAGE control setting.
SPATTER
Before beginning to weld and
periodically during welding, the
torch nozzle must be removed and
the spatter (small globules of
melted metal) cleared from the
inside of the nozzle and the
outside of the contact tip and the
gas diffuser. Spatter buildup be-
tween the contact tip and the
nozzle can cause a short circuit
and consequently, failure of the
torch or welding machine. The
frequent use of anti-spatter spray
will help prevent the adherence of
spatter to the torch components.
NOTE
DO NOT use any anti-spat-
ter spray when welding
aluminum or stainless
steel.
Restricted gas flow, holding the
torch too far from the work piece,
and the use of CO2 gas rather than
75% Argon - 25% CO2 will increase
the spatter levels.
MAINTENANCE
To ensure that this equipment
maintains its operating efficiency,
the following maintenance schedule
and procedures are recommended.
These routines should be performed
regularly by the operator.
REGULARLY - Usage and shop condi-
tions determine frequency.
1. Remove and clean the torch
nozzle and contact tip. The use
of anti-spatter spray will re-
duce the adherence of spatter
and makes its removal easier.
2. Blow out the torch liner prior
to the installation of each new
spool of wire. The contact tip
and gas diffuser must be re-
moved, but it is not necessary
to remove the liner.
3. If the torch cable assembly is
bent severely, a kink may de-
velop in the steel liner. This
can cause wire feeding problems
so a new liner should be in-
stalled.
(continued on following page)