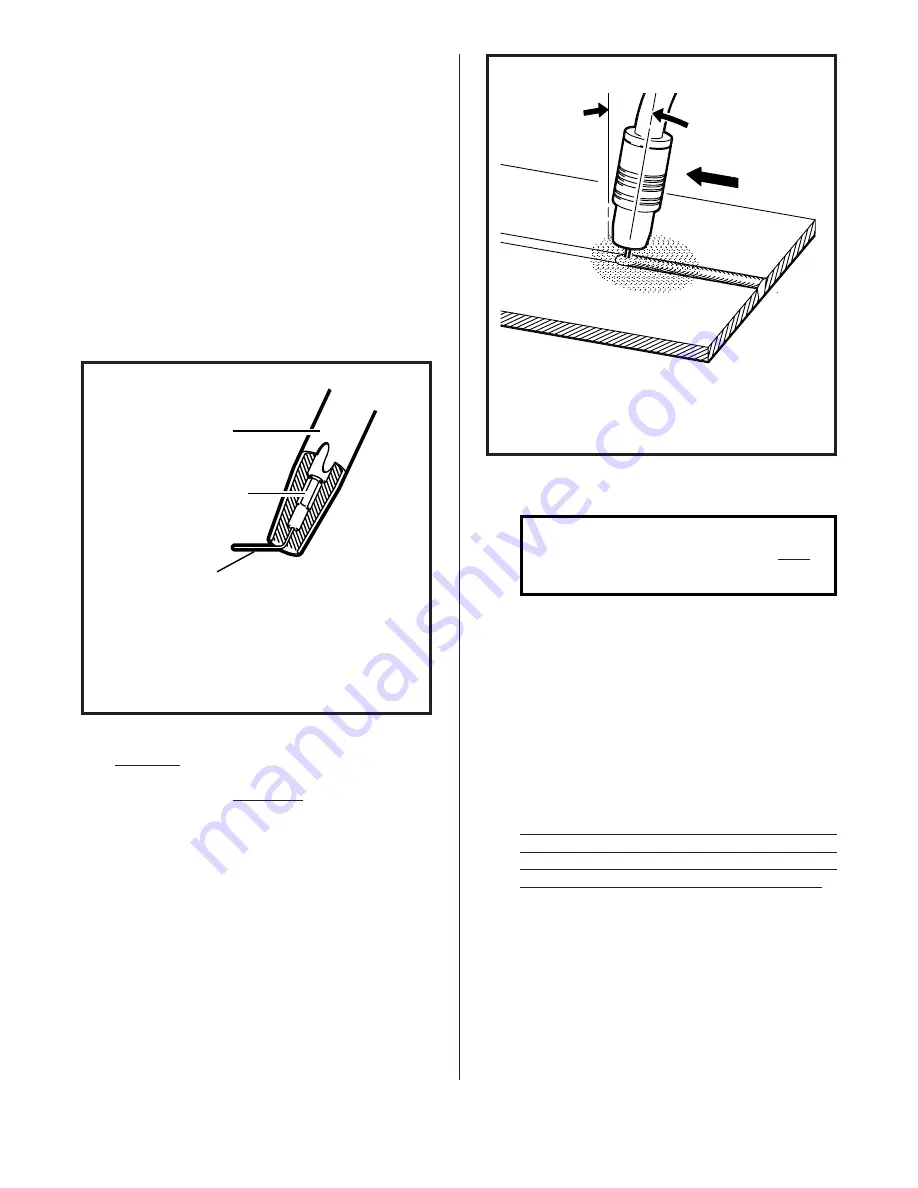
Systematics , Inc. 1025 Saunders Lane West Chester, PA. 19380
11
CONTINUOUS WELDING
ON ALUMINUM
(Optional Nylon liner and 100%
Argon shielding gas are
required)
1. Trim the electrode wire, leav-
ing approximately 1 inch stick-
out beyond the end of the
nozzle. Bend the wire over as
shown, to allow for a scratch
start. The contact tip should
be recessed inside the nozzle
approximately 3/8 inch. This
helps prevent the welding wire
from burning back to the con-
tact tip.
DIRECTION
OF TRAVEL
WORK
10 DEGREES
SHIELDING GAS
NOZZLE
CONTACT TIP
(RECESSED 3/8")
ELECTRODE
WIRE
(1" STICKOUT)
2. DO NOT spray any anti-spatter
material on the torch or base
metal and DO NOT attempt to
lubricate the aluminum wire in
any way. Weld contamination
will occur unless the wire,
base metal, torch and work area
are kept clean.
3. Bring the torch nozzle to 1/2 to
5/8 inch from the workpiece.
The recommended position of the
torch and direction of travel
for welding aluminum are shown
in figure 13.
4. Follow steps 4 and 5 as in
"Continuous Welding on Steel".
FIGURE 12.
NOZZLE ADJUSTMENT
FOR WELDING ALUMINUM
MIG SPOT WELDING ON STEEL
(OPTIONAL)
NOTE
MIG Spot Welding is NOT
recommended for aluminum.
1. Trim the electrode wire so the
stickout from the contact tip
will be flush with the nozzle
face, and fit the spot nozzle in
place.
2. Set the VOLTAGE control to "6",
the WIRE SPEED control to "9",
the Function Switch to "SPOT",
and the TIME control to "2",
then adjust the various con-
trols to obtain a perfect weld.
Refer to the Parameter Chart,
located on the access door to
the wire feed compartment, for
basic setup recommendations.
(continued on following page)
FIGURE 13. TORCH POSITION
FOR WELDING ALUMINUM