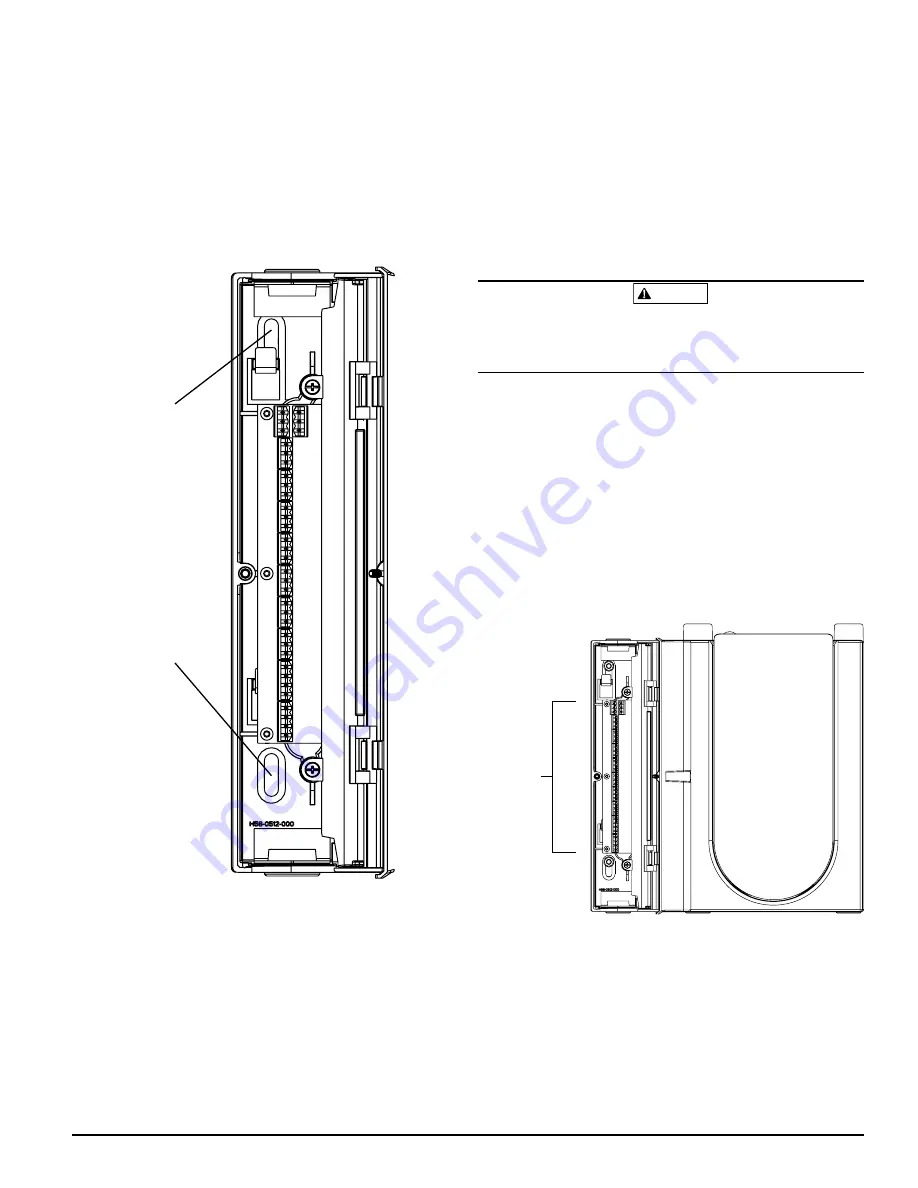
SS-400-012 3 I56-3749-006
Mounting
Slot
Mounting
Slot
ASP17-00
FIGURE 2. MOUNTING SLOTS FOR MOUNTING STUDS
Connecting the Air Sampling Pipe
The input and output ports are designed to accept standard one inch pipe (25
mm) OD. The input ports are tapered to provide fast, easy, push-fit connection
of the sampling pipe to the unit. Perform the following procedure to connect
the air sampling pipe to the unit.
1. Square off and de-burr the end of the sampling air pipe. Ensure that the pipe
is free from any particles that might interfere with the pipe connection.
2. Remove the input plug from the input port being used (either the top or
bottom of the unit).
3. Insert the sampling air pipe into the input port, ensuring a snug fit.
DO NOT glue these pipes.
Mounting the Detector to the Bracket
Once the mounting plate is attached, the unit is ready to be mounted onto the
plate. Perform the following procedure to mount the unit.
1. Before installing the unit onto the bracket, remove the appropriate con-
duit cap from the top or bottom-left side of the unit to match the orienta-
tion of the wiring. See Figure 14 for location of the wiring access plugs.
2. Line up the unit with the four mounting clips and the mounting studs on
the left side.
3. Push the unit down onto the mounting clips and secure it with the sup-
plied washer and nut on at least one of the two mounting studs protrud-
ing through the mounting slots shown in Figure 2.
Exhaust Pipe
The device should always be exhausted into the space that it is monitoring.
There are some circumstances when it may be necessary to connect a pipe to
the exhaust port to divert the exhaust away from the location of the unit. The
output ports are tapered the same as the input ports, to provide fast, easy,
push-fit connection of an exhaust pipe to the unit. Perform the following pro-
cedure to connect the exhaust pipe to the unit.
1. Square off and de-burr the end of the exhaust pipe. Ensure that the pipe
is free from any particles that might interfere with the pipe connection.
2. Remove the exhaust plug from the output port being used (either the top
or bottom of the unit).
3. Insert the exhaust pipe into the output port, ensuring a snug fit. DO NOT
glue these pipes.
WIRING
WARNING
Before working on the FAAST system, notify all required authorities that the
system will be temporarily out of service. Make sure all power is removed
from the system before opening the unit. All wiring must be in accordance
with local codes.
Power Cables
Use the power ratings of the unit to determine the required wire sizes for each
connection. Use the power ratings of the connected products to determine
proper wire size.
Conduit Usage
If electrical conduit is used for system wiring, terminate the conduits at the cable
entry ports on the top or bottom of the unit, using the appropriate conduit con-
nectors.
1. Run all wiring, both power and alarm, through the conduit and into the
left side of the unit enclosure, as shown in Figure 3.
2. Attach the appropriate wires to the supplied Euro connector. Follow ap-
propriate local codes and electrical standards for all cabling.
3. Plug the appropriate connector into the mating connector on the unit.
Power and Alarm
Connections
ASP16-00
FIGURE 3. POWER AND ALARM CONNECTION CONNECTOR BLOCK