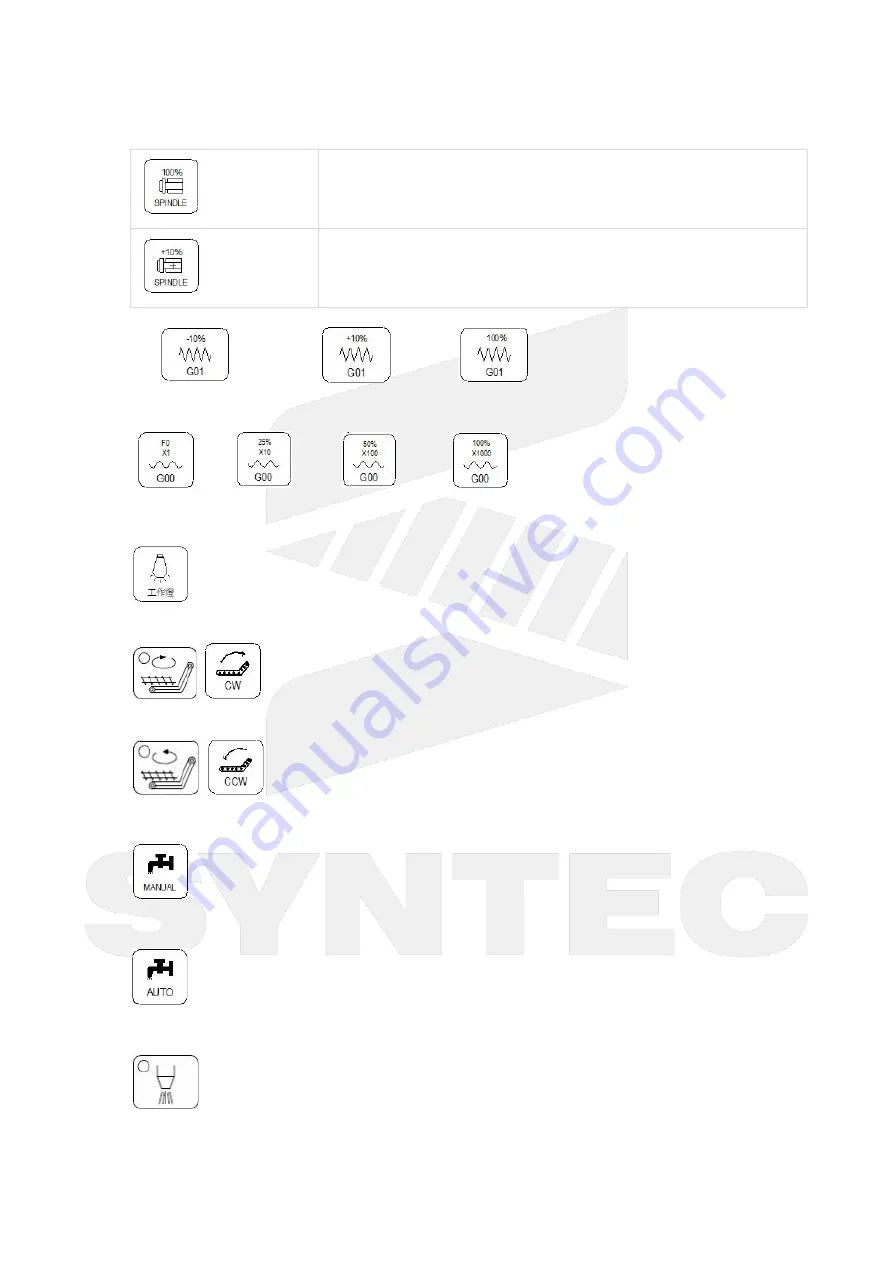
机床产品
/Machine Tool Products
–
610-E5/610-H5 5-Axis Wood Operation Manual
Machine Operation Panel
–
•
•
•
•
•
•
•
•
•
•
•
•
•
•
Spindle rate 100%: Spindle will rotate with 100% speed.
Spindle rate acceleration: Spindle speed will accelerate by 10%.
G01 Segments
Decrease G01 rate by 10% Increase G01 rate by 10% G01 rate 100%
G00 Segments
G00 rate x1 G00 rate x10 G00 rate x100 G00 rate x1000
Those function key can be regard as G00, MPG or INJOG segments.
Working LED
Working LED On/Off
Chip Conveyor Machine Clockwise Rotation
Switch chip conveyor machine to clockwise rotation
Chip Conveyor Machine Counterclockwise Rotation
Switch chip conveyor machine to counterclockwise rotation
Cutting Fluid
Working liquid On/Off
Auto Cutting Fluid
The cutting fluid M code of machining program will only be enabled after applying this function.
Blowing