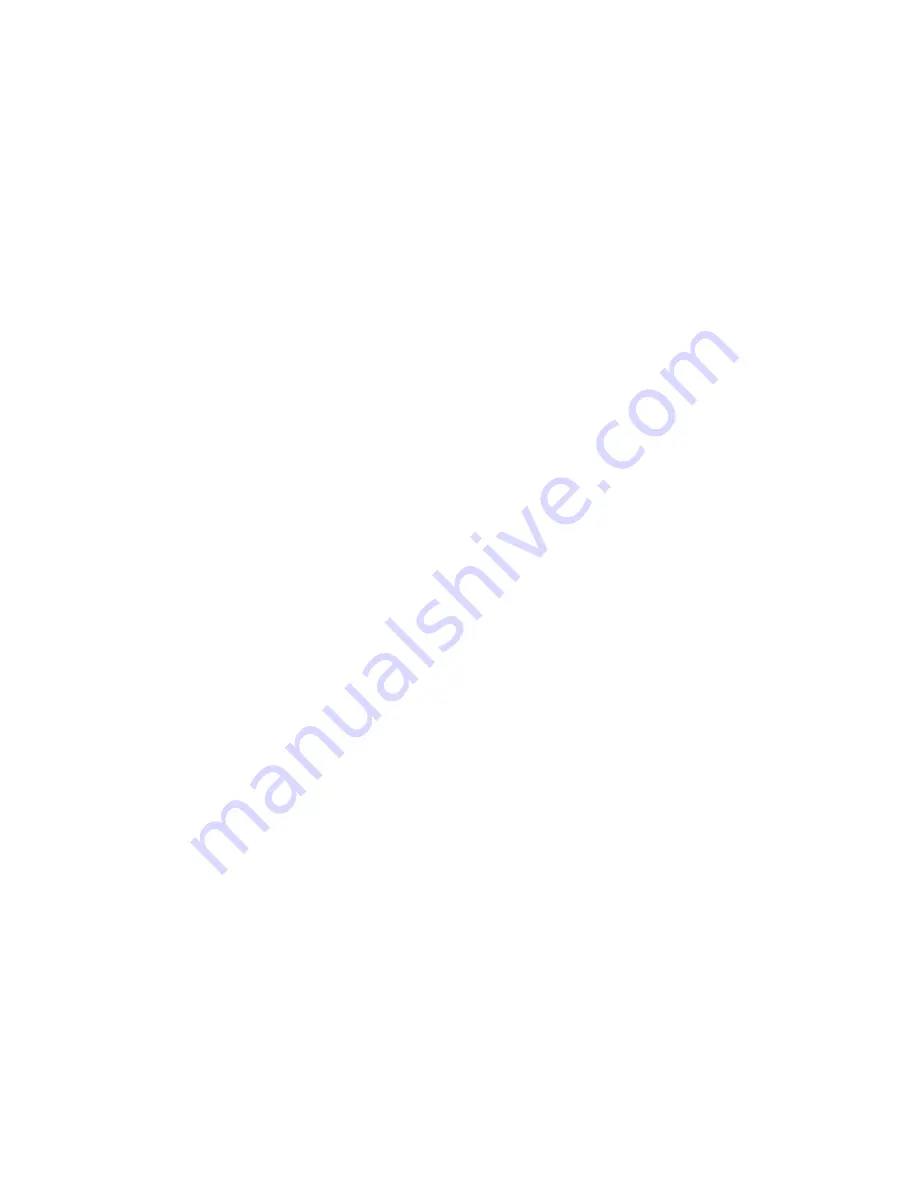
22
Synrad
Firestar OEM v30
reference guide
Operation
(cont.)
5
Turn on the +30 VDC power supply. The
PWR
LED should illuminate green.
6
If the laser has a Diode Pointer installed, remove its aperture dust cover.
7
Apply a
Laser Enable
signal to the appropriate
Interface Connector
. The yellow
RDY
lamp turns on to indicate that,
after a five-second delay, lasing is enabled when a PWM Command signal is received.
8
Press the UC-2000’s
Lase On/Off
button. The
Lase
indicator on the UC-2000 should illuminate.
9
Use the
PWM Adj Knob
on the UC-2000 Controller to slowly increase power. The v30
LASE
LED illuminates red
when PWM Command pulses are long enough to produce laser output. The spot where the beam hits the beam block
should increase in brightness, indicating an increasing power output.
If you are not using a UC-2000 to control the laser, apply tickle pulses (a +5 VDC, 5 kHz square wave of 1 µs dura-
tion) between
PWM Positive
(Pin 1) and
PWM Negative
(Pin 6) on the appropriate DB-9 or RJ45 connector. After
five to ten seconds, slowly increase the PWM duty cycle of the square wave. The v30
LASE
LED illuminates red when
PWM Command pulses are long enough to produce laser output. The spot where the beam hits the beam block should
increase in brightness, indicating an increasing power output.
10
Press the UC-2000’s
Lase On/Off
button to remove the PWM Command signal from the laser. The
LASE
LED turns
off. If your v30 laser fails to lase, refer to the Troubleshooting section for troubleshooting information.
If you are not using a UC-2000 to control the laser, remove the PWM Command signal from the laser and re-apply
tickle pulses every 200 µs. If your v30 laser fails to lase, refer to the Troubleshooting section.
Technical reference
v30 interface connectors
Two built-in interface options are available for integrating the OEM v30—a DB-9 and an RJ45 8-8 interface connector. The
RJ45 connector (
Interface B
) is useful when integrating a v30 into existing integrated laser systems previously configured for
an RJ45 interface. Use the DB-9 connector (
Interface A
) for new Firestar installations. Although both interface connectors
provide the same functionality, the DB-9 connector contains an additional output,
Lase Indicator
, that activates when the
OEM v30 is actively lasing.
The v30’s PWM input (
PWM Positive
) is optoisolated, however all other inputs and outputs operate using standard 5V logic
levels (0 V – logic low; 5 V – logic high). Inputs and outputs are ESD protected, but are
not
optoisolated; all input signals
sent to the laser must be clean or conditioned by the user. Signals for each interface connector, A or B, are described below.
Important Note:
Do not connect both
Interface A
and
Interface B
connectors at the same time as this will damage the
laser’s control board. Wire only one interface into your control system.
Note:
OEM v30 outputs are voltage sources. They can provide only 20 mA typical, 40 mA maximum, to a ground
referenced load.
The control board will be damaged if this current maximum is exceeded
. For either connector,
Interface A
or
Interface B
, the ground reference (GND) is Pin 8.
Interface A connector (DB-9)
The DB-9
Interface A
connector provides a +5 VDC auxiliary output (
DC Out
), two inputs, and four status outputs as de-
scribed in Table 5. Two user inputs,
Laser Enable
and
PWM Positive
, enable lasing and provide output power control.
Apply a +5 V signal to the
Laser Enable
input to enable lasing (after a five-second delay). Connect your PWM Command
signal (+ 5 VDC, 5 kHz nominal) between
PWM Positive
and
PWM Negative
inputs to control laser power. There is no inter-
nal tickle signal generated by the OEM v30 control board. Users
must
provide a 5 kHz, 1 µs tickle pulse between applied
PWM Command signals.