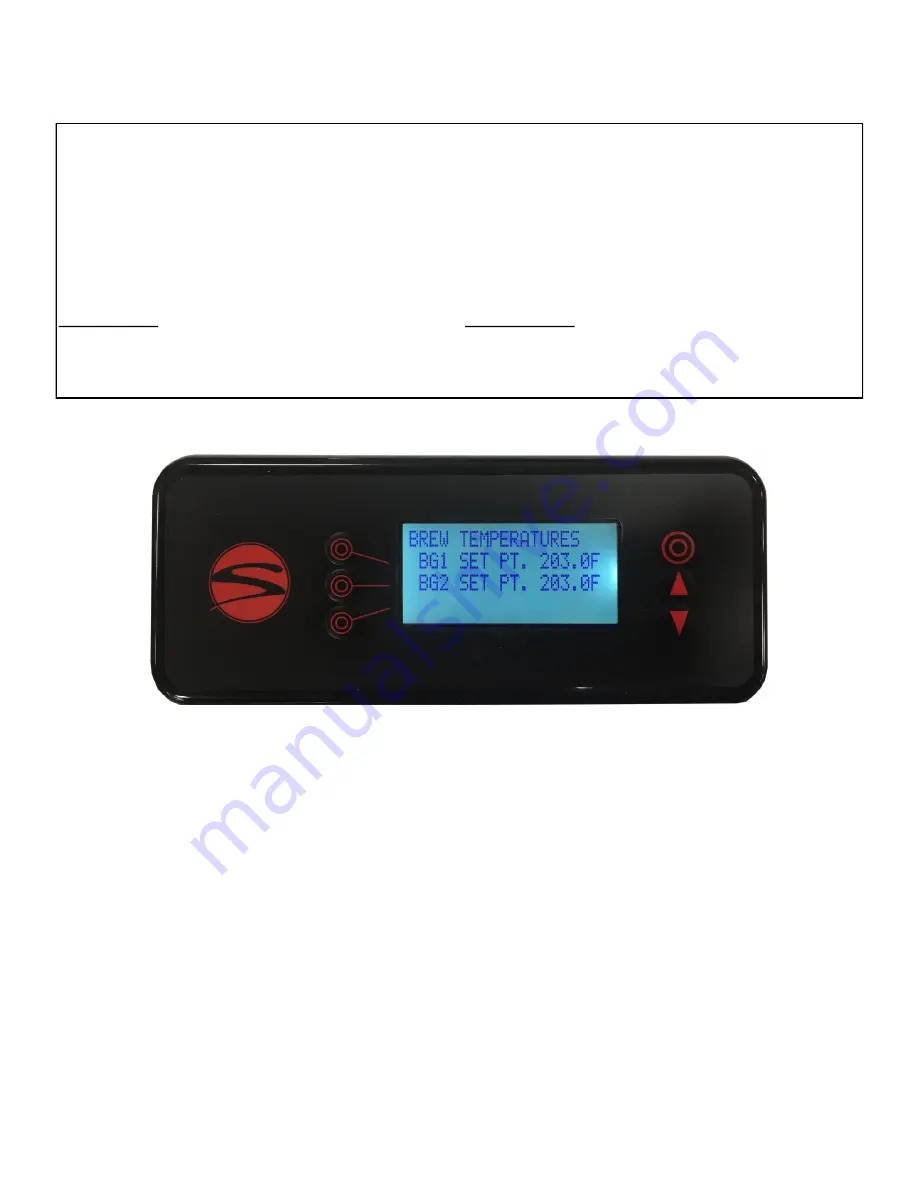
19
PROGRAMMING
Factory Settings:
The factory settings for your machine are as follows:
Brew Group Temperature
203°F
Steam Tank Temperature
250°F
Program Mode
Universal (2 programs)
Temperature Units
Fahrenheit
Left program:
Right program:
Pre
-
Infusion
4 seconds
Pre
-
Infusion
4 seconds
Total Water Count
280
Total Water Count
380
The set point is a goal temperature for the brew tank. The tank will heat to reach the set point, then use a PID
based algorithm to remain stable and balanced at that temperature when in use.
Allow 10
-
15 minutes for a brew group to adjust to a large set point change. Smaller changes take less time to
restabilize.
Line 2 indicates the set point for brew group 1, in this example
“203.0
F
”.
Line 3 indicates the set point for brew group 2, in this example
“203.0
F
”.
To cycle to the next display screen, press the down button.
Menu Level 1: Brew Temperatures