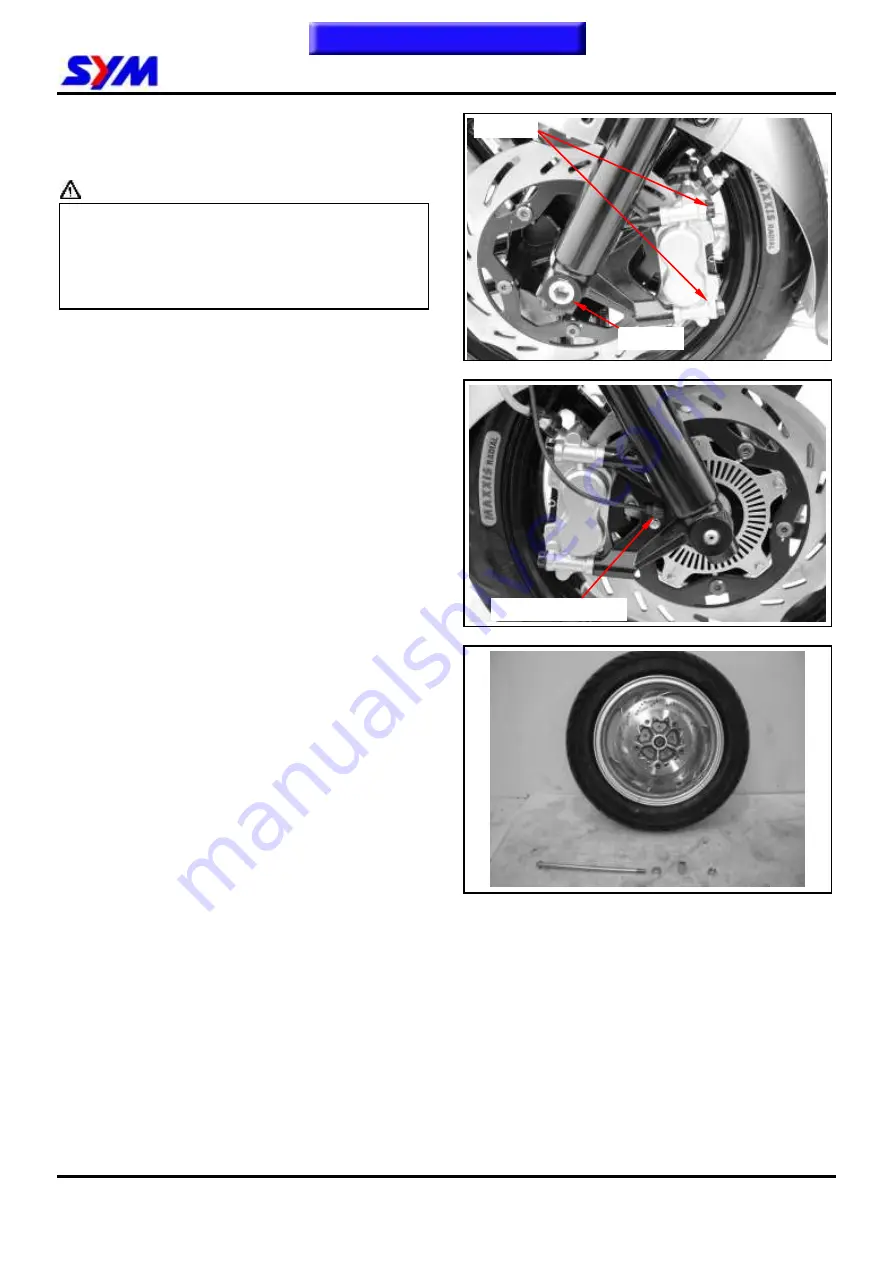
15-5
Front Wheel
Loosen 2 bolts from the front brake caliper and
remove it
Caution
Care shall be taken not to push the brake
lever to avoid the brake pad being squeezed
out. In case that the brake pad is accidentally
squeezed out, use a screwdriver to force it
back to the place.
Loosen screw & remove speedometer cable.
Turn loose the axle nut.
Pull out the front wheel axle.
Remove the front wheel and both side collar.
2 screws
To this chapter contents
Axle nut
Speedometer cable
Summary of Contents for MAXSYM 400i
Page 23: ...1 General Information 1 18 NOTE To this chapter contents...
Page 75: ...4 Fuel Injection System 4 30 EFi System Circuit To this chapter contents...
Page 104: ...4 Fuel Injection System 4 59...
Page 109: ...5 ENGINE REMOVAL 5 5...
Page 132: ...7 Cylinder Piston 7 7...
Page 136: ...7 Cylinder Piston 7 11 NOTE To this chapter contents...
Page 171: ...11 Crankshaft Crankcase 11 8 NOTE To this chapter contents...
Page 183: ...12 Cooling System 12 12 NOTE To this chapter contents...
Page 199: ...13 Body Cover 13 16 NOTE To this chapter contents...
Page 219: ...14 Brake System 14 20 NOTE...
Page 231: ...14 Brake System 14 12 NOTE To this chapter contents...
Page 253: ...17 Electrical System 17 5 Fuse Fuse circuit diagram To this chapter contents...
Page 270: ...17 Electrical System 17 22 NOTE To this chapter contents...
Page 271: ...18 Wiring Diagram 18 1 18 Homepage Contents...
Page 272: ...18 Wiring Diagram 18 2...
Page 273: ...18 Wiring Diagram 18 3...
Page 274: ...18 Wiring Diagram 18 4 NOTE Homepage Contents...