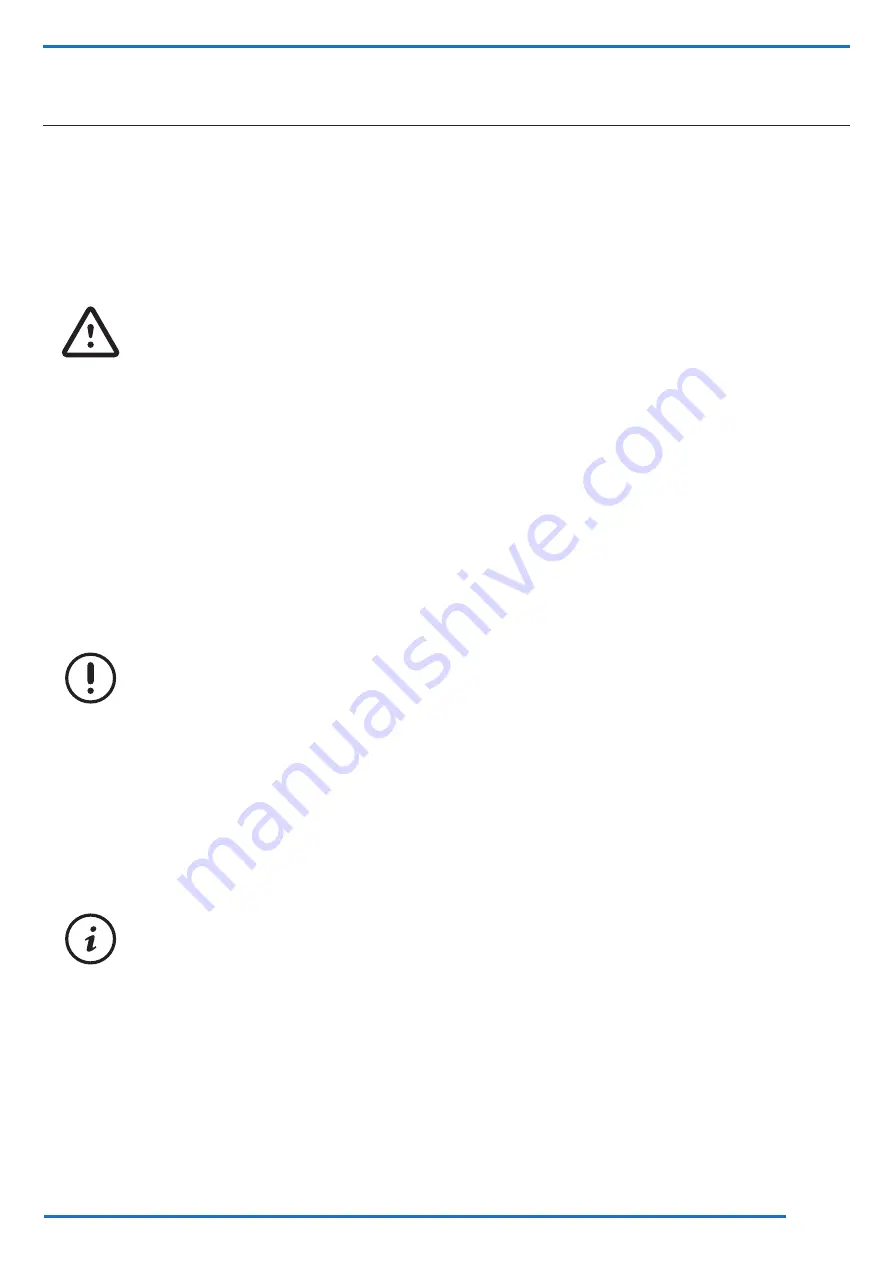
57
We reserve the right to make changes without any prior notice.
Translation from original instructions
8.2 Internal cleaning
It is essential to keep the installation site clean and tidy for correct maintenance of the unit and to keep it in good working
order.
8.2.1 Cleaning the unit
Keep the inside of the electrical control panel and (where present) the compressor compartment clean.
After working on the unit, always clean the electrical control panel of any work remnants and extraneous components.
Restore the safety devices and protective devices that had to be removed in order to carry out the work.
Use a vacuum cleaner to eliminate small objects, work remnants and/or any dust.
Do not use compressed air
If you have to carry out work on compressors inside the compartment, before closing it again, check that the electrical box
of the compressor is closed correctly and that any refrigerant circuit valves are in the correct state, and make sure you do
not leave any materials inside the compartment.
8.2.2 Cleaning the plate heat exchangers
Thanks to the generally very high level of turbulence, in plate heat exchangers, a self-cleaning effect takes place in the
channels.
However, in some applications the tendency to scaling and/or the formation of deposits in the heat exchanger can be very
high (e.g. use of very hard water at high temperatures).
An increase in head losses on the hydraulic circuit and a decrease in temperature difference between water inlet and outlet,
are a sign that the exchanger is becoming fouled.
In such cases, the heat exchanger can always be cleaned by circulating an in-situ cleaning fluid (CIP).
When carrying out the operations described here, adopt all the technical and organisational measures provi-
ded for by workplace safety laws and regulations; use the personal protective equipment in accordance with
the instructions in the safety data sheets for the chemical products used.
Also, all technical and organisational measures for waste water treatment must be applied in accordance
with current environmental laws and regulations.
To reduce the extent of scaling and residues, use a 5% solution of oxalic acid (COOH)
2
at 20°C as washing fluid: cleaning
with acid solution must be carried out for no longer than 15 minutes.
After finishing cleaning with acid detergent solutions, use a 2% solution of sodium bicarbonate (NaHCO
3
) at 20°C to neu-
tralise the acid solution.
The flow rate of the acid and basic solution must be at least 1.5 times the operating flow rate with reverse circulation mode.
Then wash with plenty of clean soft water until all traces of acid and basic solution have been removed from the heat
exchanger. Any traces of acid or basic fluids left inside the heat exchanger can cause serious damage to property and
people.
If it is thought that the exchangers will need to be washed regularly, installing CIP valves in the hydraulic
circuits will make this operation easier.